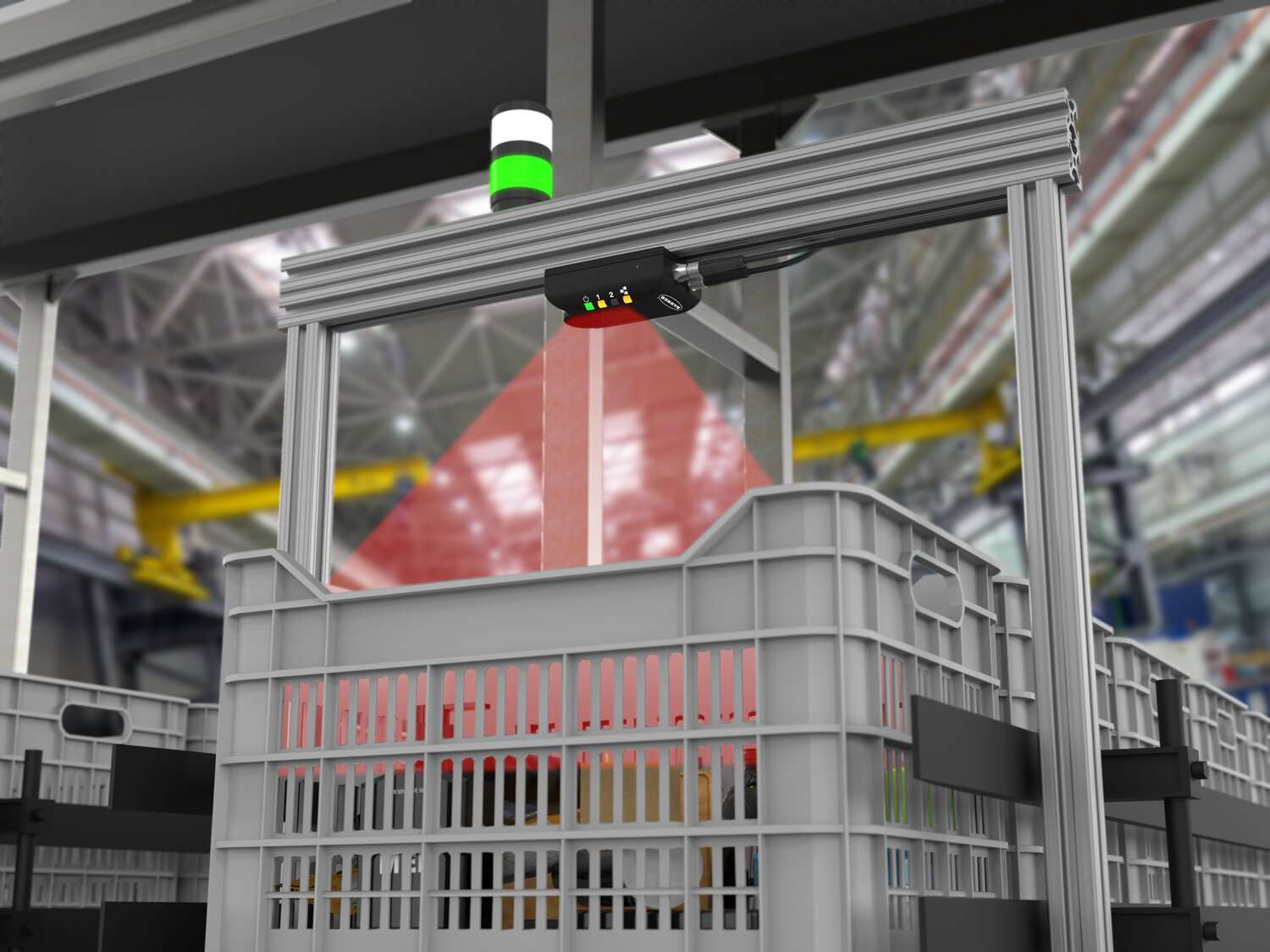
Easily Measure Bulk Container Fill Levels with Technology from Banner
As packages and other products come down a line, an automated sorting system distributes the parcels and sends them to their intended destination. These items usually end up in some sort of bulk container, whether a bin, cart, cage, tote, or basket truck. When these bulk containers are filled, a human operator or robot needs to know they are full and ready to be retrieved. However, accurately measuring the fill levels of these bulk containers can be challenging.
In material handling and logistics automation, these packages rarely fall into a nice, neat stack. Varying sizes and nonuniform shapes can create odd angles and uneven piles with peaks, valleys, and gaps between packages which make precision fill level monitoring very challenging. Even scrap materials that come out of a chute will pile up in one part of a cart and leave other areas unfilled. To solve these fill problems, Banner has multiple solutions for monitoring the fill levels all across bulk containers.
ZMX 3D Measurement Sensor Is the Ideal Single-Sensor Solution for Bin Level Monitoring
Using thousands of laser measurement points, the ZMX 3D Measurement Sensor can measure not only the peak heights of objects in a bulk container, but the volume fill percent as well. This measurement can be performed across a wide area, so only one ZMX sensor is needed to monitor the entire Region of Interest (ROI), whether it is a bag, bin, rolling cage, or Gaylord box. Packing tens of thousands of pixels into its sensing array, the ZMX delivers accurate measurement and detailed fill level representation. It also allows more precise positioning of the ROI, including the ability to reach the very edges of a bin.
Along with its 2.5-meter range, the ZMX 3D Sensor monitors a broad 60° by 45° three-dimensional field of view, detecting fill height variations in items of any shape, size, or orientation. These abilities allow the ZMX to ensure containers are filled to a consistent volume, prevent overfill, or track fill rates and fine-tune processing speeds.
Banner's 3D Configuration Software helps you set up and integrate the ZMX quickly. Mount and position the sensor pointing downward toward the bulk container that needs monitoring, then connect the sensor to power and a PC running the configuration software. The easy-to-use software shows operators what the sensor sees in real-time, aiding the configuration process. Once configured, the ZMX is self-contained, ready to send signals to an indication light, controller, or PLC, letting operators know which bins are filling up and when they need attending.
Once set up, the ZMX operates independently, without any reliance on other devices. An all-in-one design integrates logic directly into the sensor, meaning no PC or controller is needed after setup, and no external lighting is required. Additional features, including Ethernet and on-the-fly configuration, make the ZMX an incredibly versatile bulk container fill level sensing solution.
K50Z Multipoint Sensor Delivers Cost-Efficient Single-Device Measurement
The K50Z Multipoint Sensor is also highly effective for detecting accumulating objects in a basket truck or other bulk container by measuring both nearest distance and average distance. It is similar to the ZMX in that it uses 3D time-of-flight technology to detect in multiple dimensions across a large area, but it does so with 64 different measurement points across an 8 by 8 pixel array. The K50Z has a wide 45° by 45° beam angle with a two-meter range which allows the K50Z to monitor the entire target area of a container.
One especially useful feature of the K50Z is that its two independently configured outputs allow it to monitor two separate areas within its field of view. This ability can be used to monitor two different areas in one container, or used in place of two separate sensors for monitoring two different bins being filled on an automated sorting system. These outputs are easily configured using the intuitive Banner Measurement Sensor Software. This software simplifies both the setup process and sensor configuration by visualizing everything the sensor is detecting in real-time. This gives operators the same view as the sensor, enabling them to easily make both coarse and granular adjustments.
Q2X Series Laser Sensor Brings Versatility to Fill Level Measurement
The Q2X Laser Measurement Sensors use an infrared laser with a larger spot size than typical single-point laser sensors, making it ideal for bin-fill applications with uneven surfaces, peaks, and valleys. Like the ZMX and K50Z, it can measure challenging targets without regard to color, including dark, shiny, or clear objects. But unlike 3D time-of-flight sensors, it cannot measure across a wide area. It offers a more traditional way to detect fill levels, requiring multiple sensors to monitor various parts of a bulk container being filled. However, it can deliver high performance at a lower cost than 3D time-of-flight options, especially if the application only needs one point to be monitored.
Visual Indication Simplifies Container Fill Monitoring
Of course, being able to effectively communicate the fill levels of any receptacle is a crucial component of any automated sorting system. While sensors are great at detecting the fill levels in bulk containers, they need help to clearly communicate this information to operators. This is where visual indication is needed.
Visual indication can come in many different forms, whether small single-colored lights, large multicolored lights, or something in-between. Segmented lights such as Banner’s TL70 Pro Series Tower Light can provide custom indication to operators, communicating status such as when bulk containers need emptying or other attention. The colors and animations of these lights can be configured with Banner’s Pro Editor software.
Programmable multicolor strip lights, however, communicate the most complete information about the precise fill level in any container, converting the sensor data to a series of easy-to-understand colors. Using Banner’s WLS15 and WLS27 Pro Series strip lights in conjunction with fill level sensors give operators a clear understanding of material fill levels changing in real-time. Like the TL70, these strip lights are programmable with Banner’s Pro Editor software. However, the WLS strip lights can communicate much more detailed and specific information. For example, an empty basket truck would be indicated by a solid blue. As the truck begins to fill with boxes, the strip light turns green starting at the bottom and slowly rises to represent the height of the boxes inside the basket truck. As the basket is filled past the halfway point, the rising light turns yellow. When the sensor recognizes that the basket truck is nearly full, the light turns red, and may be programmed to flash if an overfill is about to occur.
Contact Banner to Simplify Your Fill Level Monitoring
Keep your production line moving smoothly and efficiently wherever bins, baskets, boxes, and carts are being filled by deploying appropriate sensors and indicator lights. With a variety of bulk container level sensors and programmable indication, Banner engineers will carefully assess your needs and create a solution that fits your needs both now and in the future. Contact an engineer to get started today.