Beverage: Secondary Packaging
Secondary packaging on a beverage filling line begins with the application of a label to a filled and closed beverage container. Every label must be checked for accuracy, appearance, and position. Date/lot codes are critical in the event of a product recall and must be clearly and accurately printed on each container. The containers are then packaged together in cartons, cases, bliss trays, or shrink wrapped together. Each package must be filled with the correct count of containers and properly sealed.
Used at every step of this process, products and solutions from Banner Engineering help beverage producers package containers with greater accuracy and increased throughput. Our vision and image sensors provide comprehensive inspection capabilities for label verification and date/lot code inspection. LED, laser, and photoelectric sensors from Banner are rugged, easy to use and solve many challenging secondary packaging applications, including regulating product flow and detecting targets with vibrant graphics and clear, shiny packaging. Banner offers a full and expanding line of LED light fixtures that provide brilliant illumination for work stations, equipment, and vision systems. Our LED indicators provide high visibility, at-a-glance notification of equipment status with options for high decibel audible alerts to notify for critical conditions.
Secondary Packaging Beverage Applications
View Applications by Machine Type
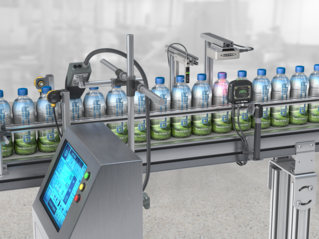
Coding & Marking
The beverage industry has many rules and regulations in place to make sure that the highest quality products are being delivered to customers. In order to keep track of when and where bottles were filled and packaged, date/lot codes need to be present on the bottles.
Featured Applications
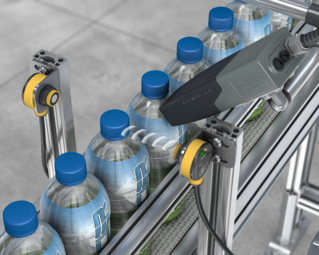
Trigger Sensing on Printer
In the beverage industry, date/lot codes are mandatory on all products in order to identify when and where a product was manufactured. Finding a solution that can accurately identify the bottle caps and then trigger a machine to print the date/lot codes onto the bottle is required.
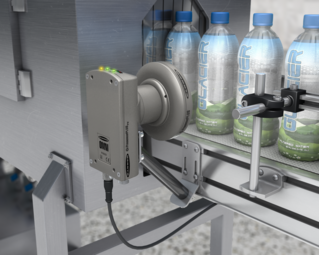
Shrink Sleeve Label Presence and Correct Label Verification
The P4 OMNI vision camera is located immediately after the bottles leave the labeler which assures that the presentation of the label will be in a repeatable manner and therefore can be compared to a stored image for a match. The P4 OMNI is sealed to IP68 and made with nickel plated zinc housing.
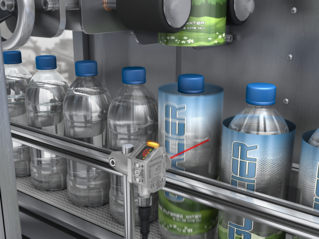
Detecting Clear Bottles to Trigger Shrink Sleeve Labeler
High-speed labeler processing 800 bottles per minute
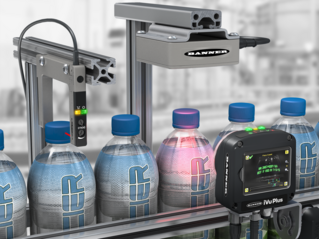
Date/Lot Code Presence or Absence Detection
An SLM series slot sensor and an iVu Series vision sensor are used to detect bottles passing on the line and to verify that date/lot codes have been correctly printed onto the bottles.
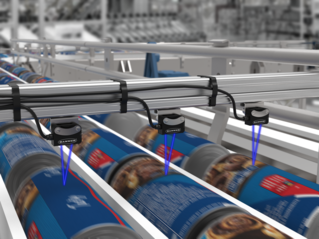
Refrigerated Breakfast Roll Detection on Multi-Lane Conveyor
Dark packaging with multiple colors transitions can be difficult to detect with traditional red LED sensors. Banner Engineering’s miniature VS8 photoelectric sensor with blue LED works well with low reflectivity labels to detect refrigerated food packaged in pressurized cans. The small sensors fit into tight spaces and work well for short range applications. The blue LED works with the small spot size to minimize the effects of color transitions on the labels.