Case Packing Solutions for Food Packaging
Once empty cases are assembled, they move on to the case packer station where food cartons are staged and then packed into the cases to prepare for shipment. As the sealed cartons move into the packer area, they are counted and prepared for transfer into the cases.
Once the position of each case is confirmed, a robot equipped with vacuum cups will pick up multiple cartons at a time and transfer them into the cases layer by layer until the case is full. Using an automated robot speeds up the packing process and improves efficiency on the line.
Sensors count the food packages and confirm that they are staged correctly while also confirming the presence of the case. The cases’ height is also monitored to ensure that each one is full before moving further down the line. Barcode monitoring is crucial to ensure the correct contents are being packed.
Detection in this area can be challenging since food cartons come in many different colors and sizes and require higher level sensor solutions.
Featured Applications
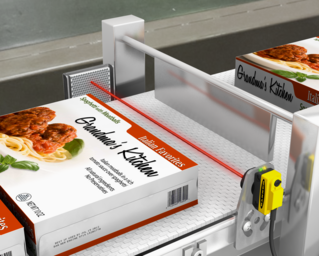
Counting Food Cartons for Correct Packaging
Banner’s WORLD-BEAM QS18LP laser sensor accurately inspects every carton that passes on the conveyor, ensuring the robot is triggered to load cartons into the package. With a visible laser sensing beam, the QS18LP provides precise position control, which is ideal to ensure accurate counting of cartons at a close range. The rugged QS18LP is also ideal for confined spaces and is easily set up along a conveyor for accurate sensing. With highly bright LEDs, operating status is visible from 360⁰.
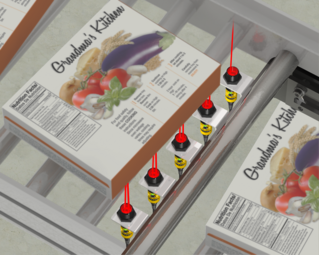
Detecting Different Size Packages on a Conveyor
Banner’s S18-2 barrel sensor is a cost-effective, reliable sensing method for this type of application. Its small size makes it easy to integrate along the manufacturing line, and its competitive price means it is well-suited for applications requiring multiple sensors. With a powerful and bright visible red emitter beam, the S18 sensors are easy to align during set up.