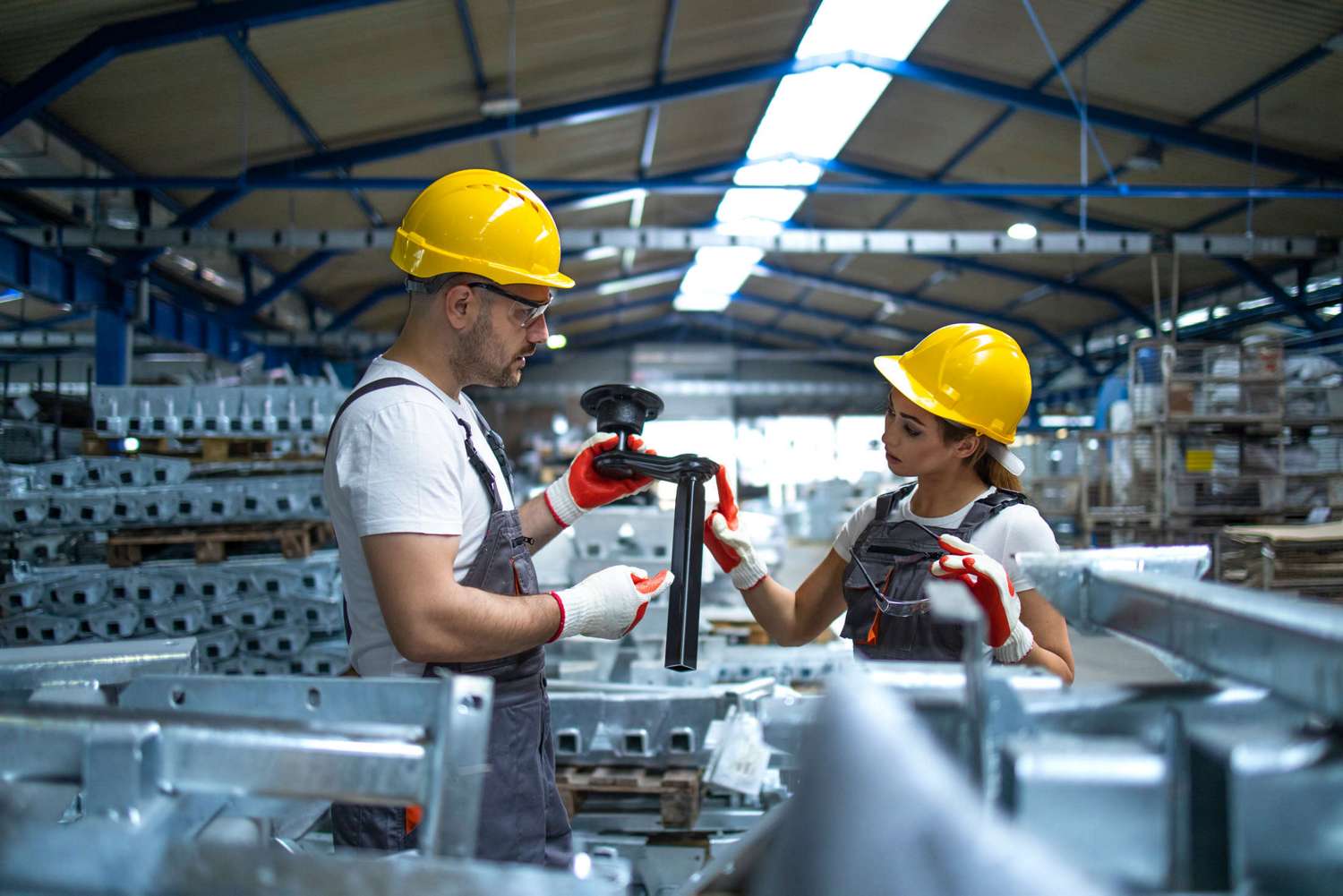
Q5X Jam Detection
Respond to Conveyor Jams Quickly, Reduce False Jams, Boost Productivity
Respond to Jams Faster
Whenever items on a conveyor unexpectedly get stuck and cause a jam, it leads to a potentially costly production delay if not resolved quickly. Over time, frequent jams can add up to a serious drain on throughput and profitability. Additionally, when products get stuck in conveyor jams, they can incur damage from repeated collisions. Therefore, manufacturers should identify jams immediately and resolve them as soon as possible.
The Banner Q5X Jam Detection Sensor is a plug-and-play solution that immediately alerts operators whenever a physical jam occurs. They can then clear the jam and get the line moving again with minimal interruption. This helps reduce overall downtime significantly, particularly for conveyor systems featuring curves, gravity-fed spirals, and other potential bottlenecks.
Traditionally, jam detection on conveyors incorporates a photoelectric sensor beam that products interrupt as they move forward through the system. When one item completely passes the sensor beam, there should be a gap before the next item interrupts it, and these regularly recurring gaps are used to identify individual items and maintain proper automation speed.
By contrast, the Q5X Jam Detection Sensor does not rely on gap identification. Instead, it extends the functionality of Banner's existing dual-mode technology with a built-in jam algorithm. This enables the sensor to detect changes in signal strength and distance between the face of the sensor and the products. With this approach, the sensor can easily detect when items are freely flowing. This is a much more accurate method of detecting conveyor jams when they occur.
A false jam is whenever a sensing system detects a conveyor jam when in fact no jam is actually present. For example, a typical sensor might incorrectly identify a jam in a production line if two packages that are freely moving through the system are simply too close together for a visual gap between them to be registered. These false jams cause lost productivity due to unnecessarily stopping lines, causing downstream processes to be starved for work, and wasted time when maintenance is forced to check on problems that do not exist. The Q5X Jam Detection Sensor drastically reduces false jams—in some instances reducing them by 80–90 percent.
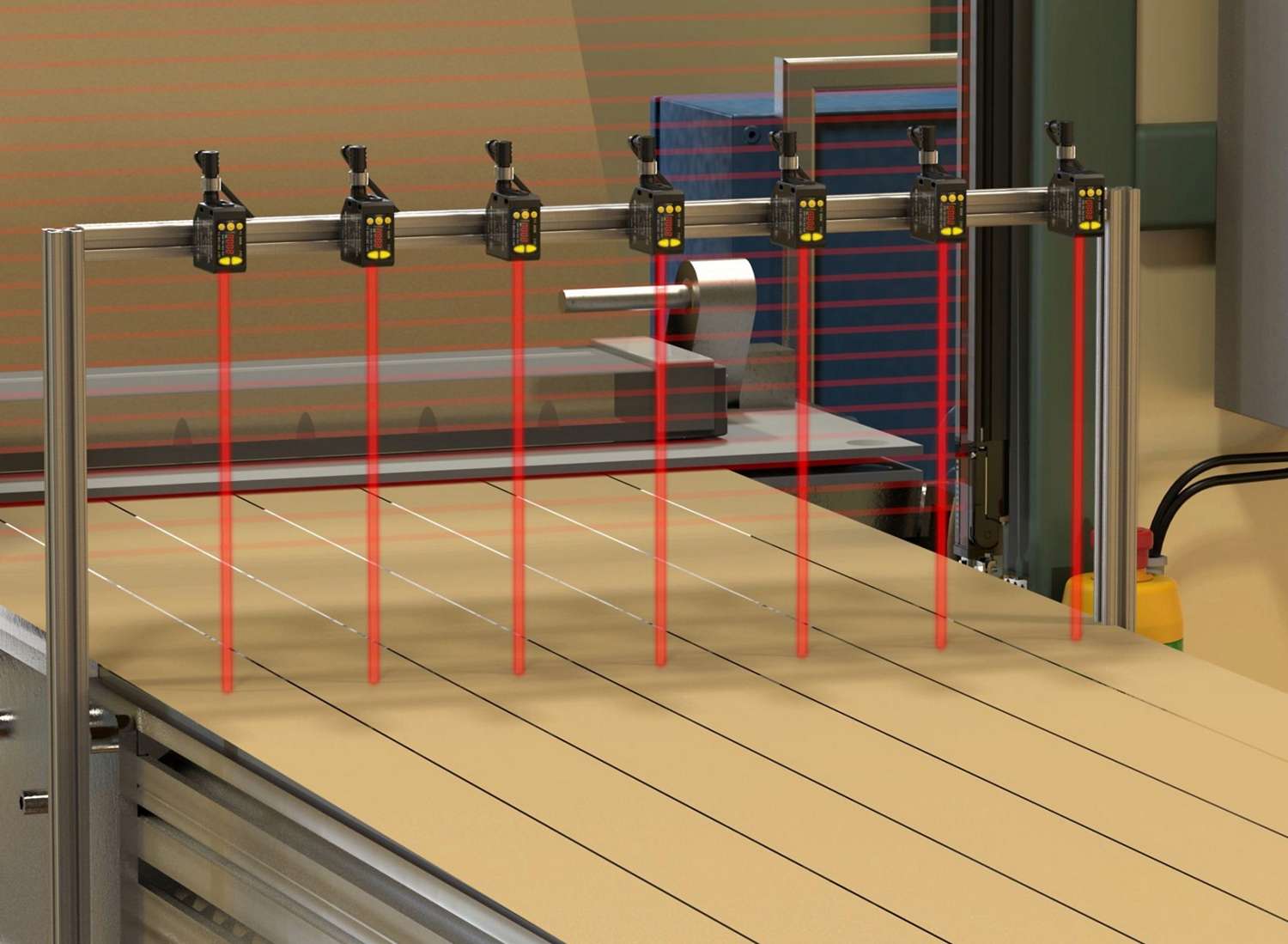
See How Much False Jams Are Costing You
How much money are false jams costing you? In one instance, a customer of ours discovered that 82% of jams detected on conveyors using conventional sensing methods were false jams. The cost of these errors add up and include the following:
- Lost productivity due to conveyors stopping unnecessarily, starving downstream processes.
- Lost time spent on diagnosing a problem that is not actually there.
When products such as packaged items become jammed in a conveyor system, they pile up rapidly, and workers need to physically intervene to clear the congestion. Typically these jams must be cleared manually, either directly by hand or with the use of “jam poles” to dislodge the stuck items. Additionally, some applications may require workers to access hazardous areas to clear jams.
Because the Q5X Jam Detection Sensor detects jams faster and more accurately, workers can clear them before they pile up excessively, potentially toppling or spilling off of conveyors. And in dangerous production environments, having fewer false jam detections will significantly reduce workers potential exposure to hazards.
When jams occur, and packages or other items pile up on conveyors, they can cause added strain to motorized systems, leading to excess wear. This can lead to more frequent, costly, and time-consuming maintenance to repair equipment. However, when a system is outfitted with Q5X Jam Detection Sensors, actual jams can be detected and resolved before items build up, which could contribute to deterioration of machine parts over time.
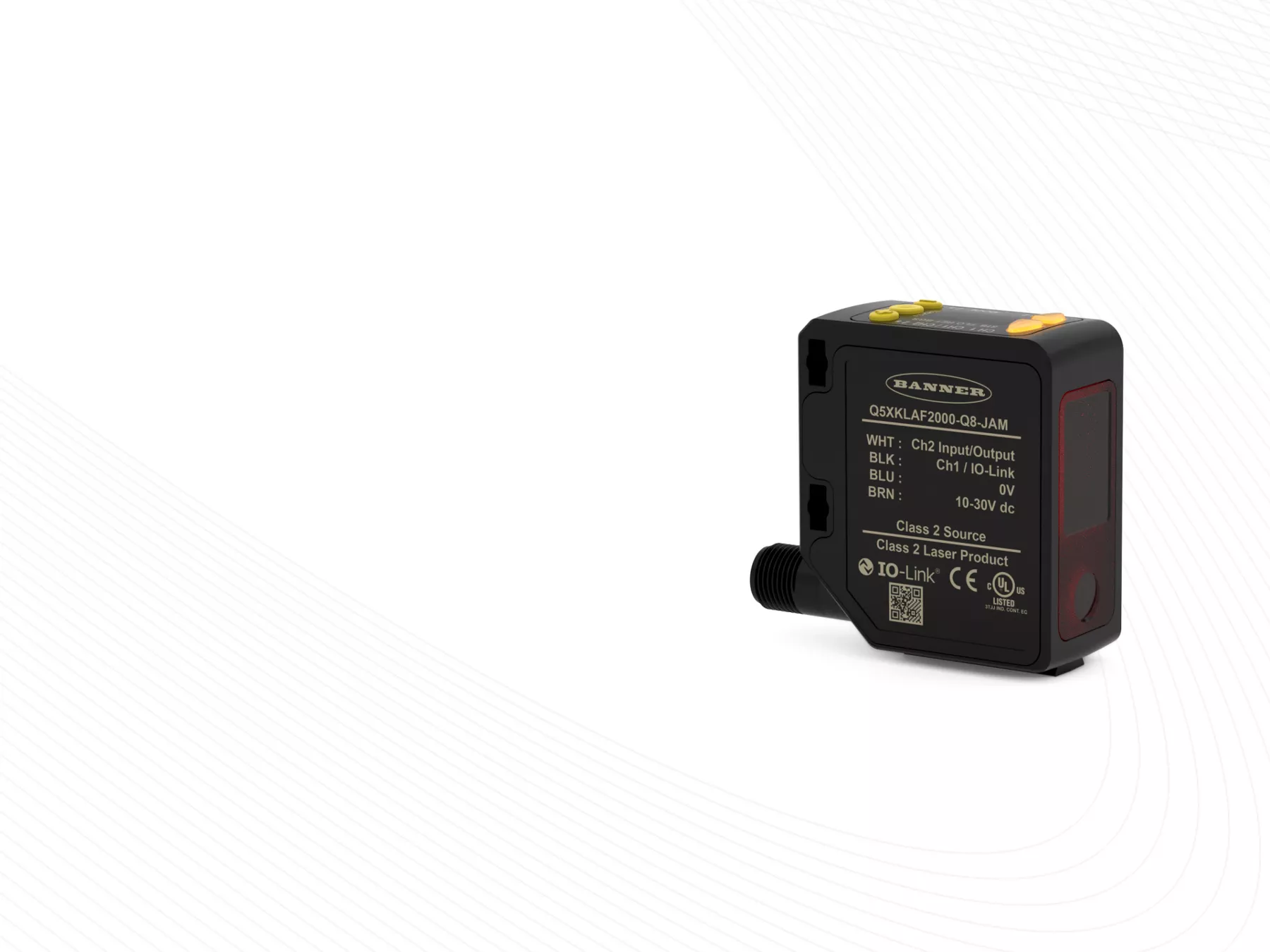
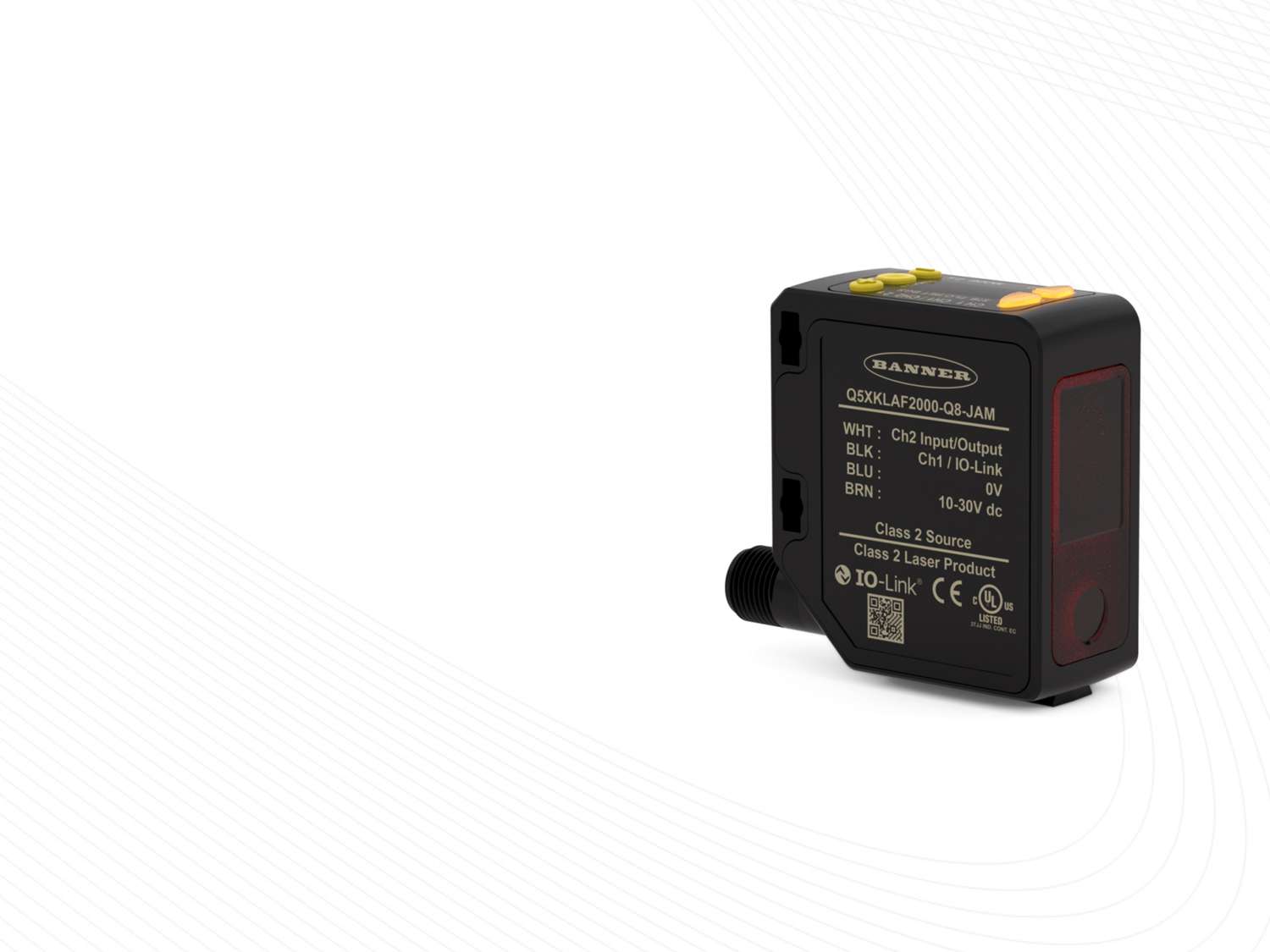
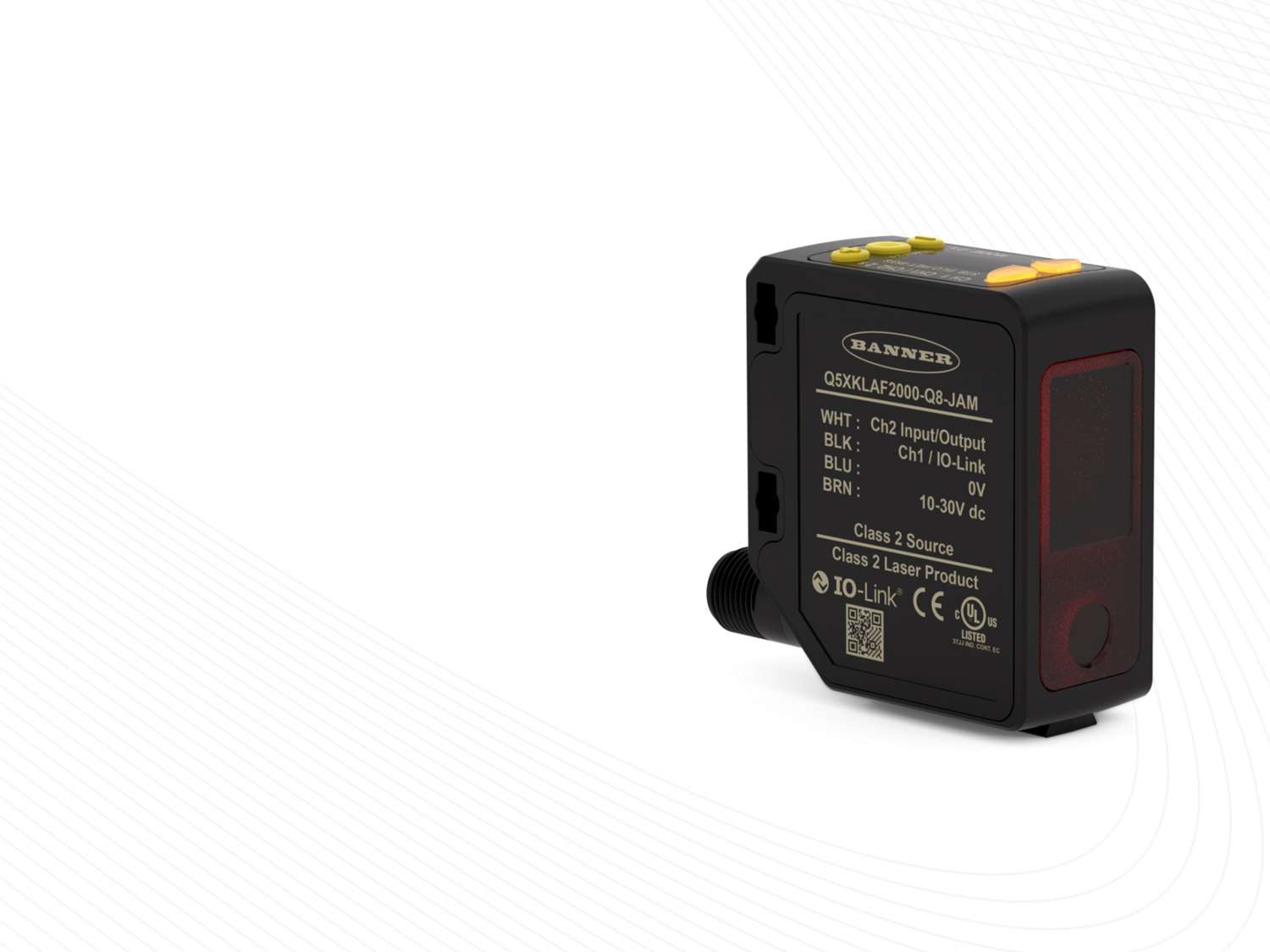
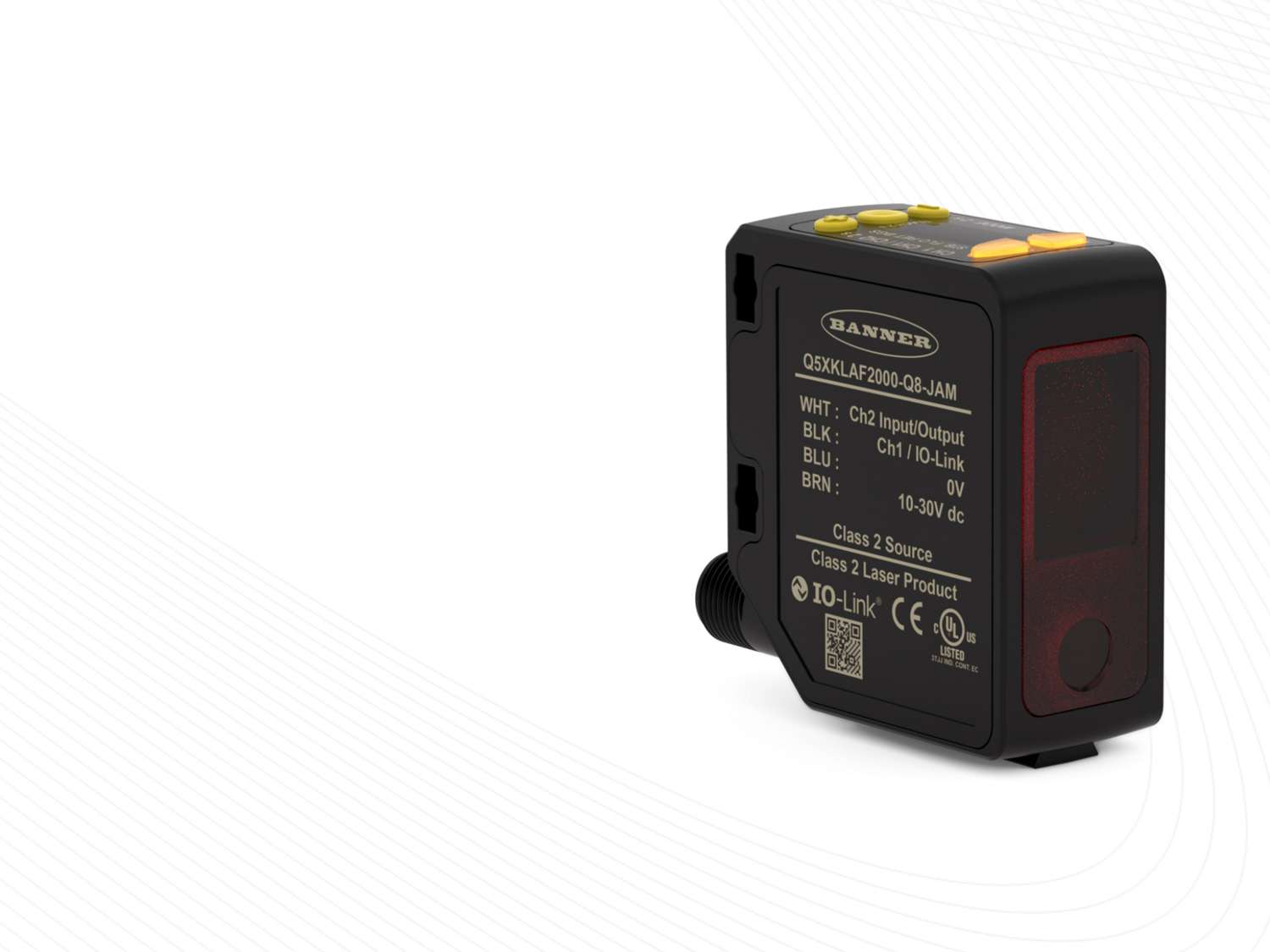
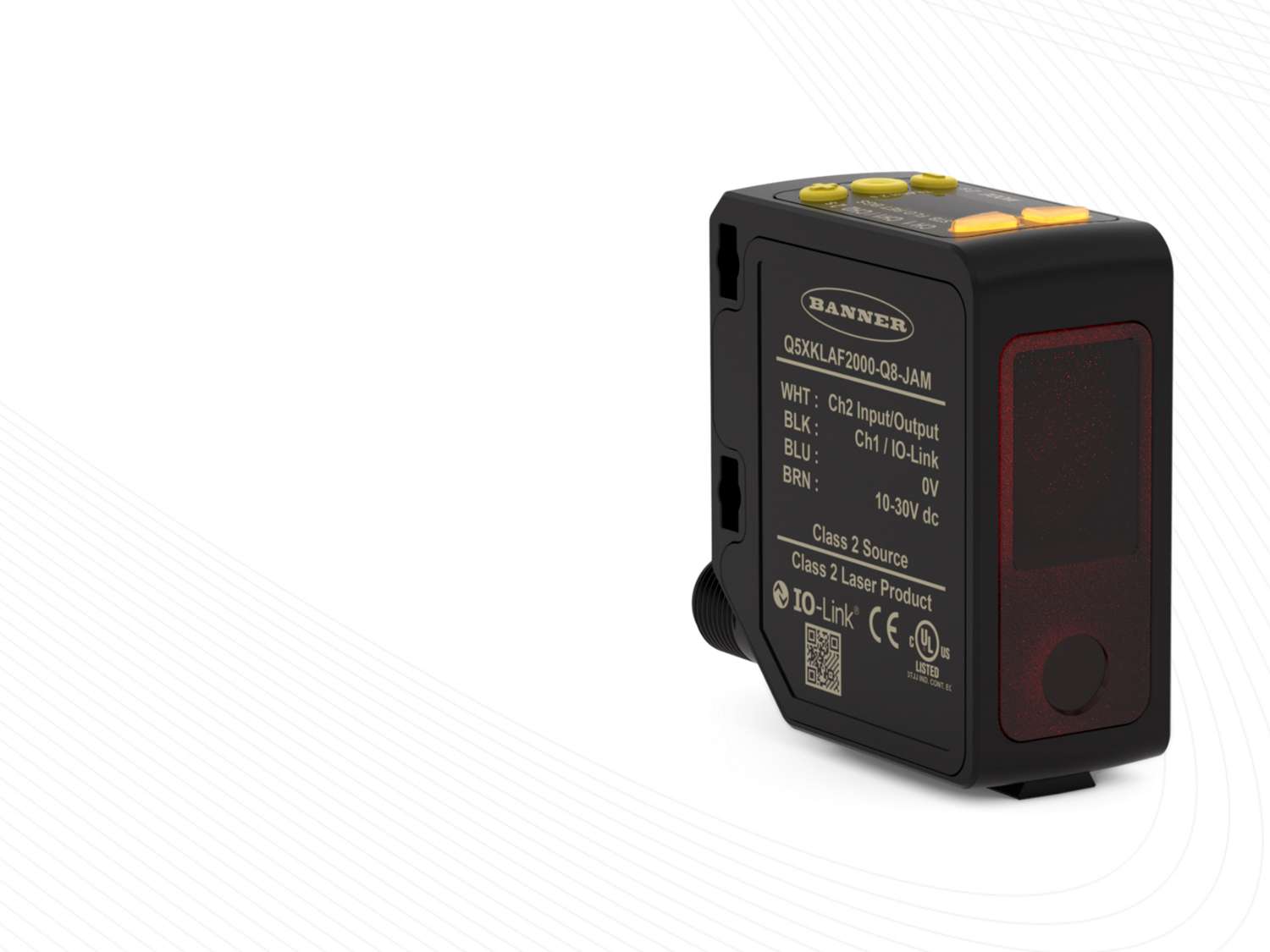
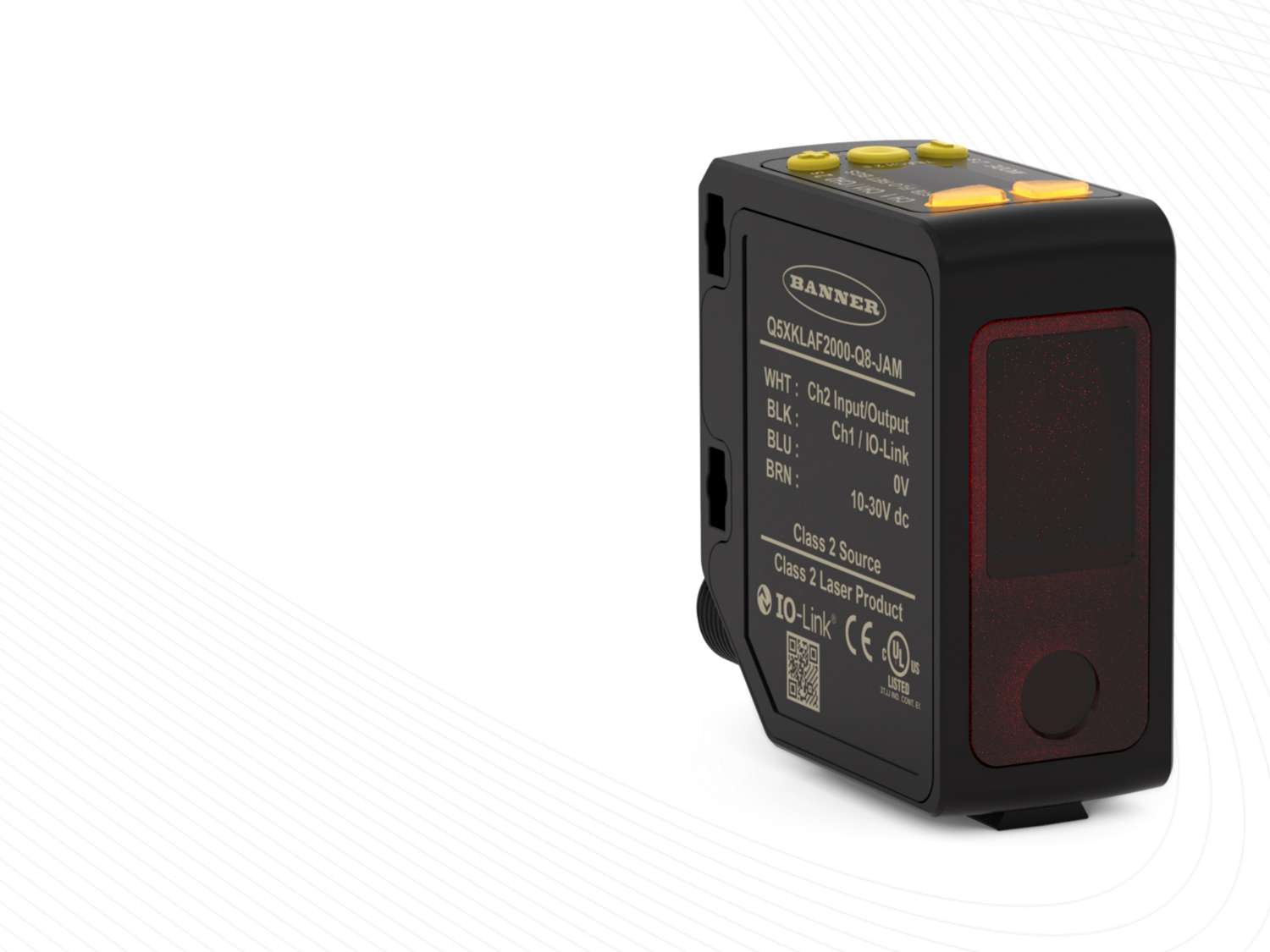
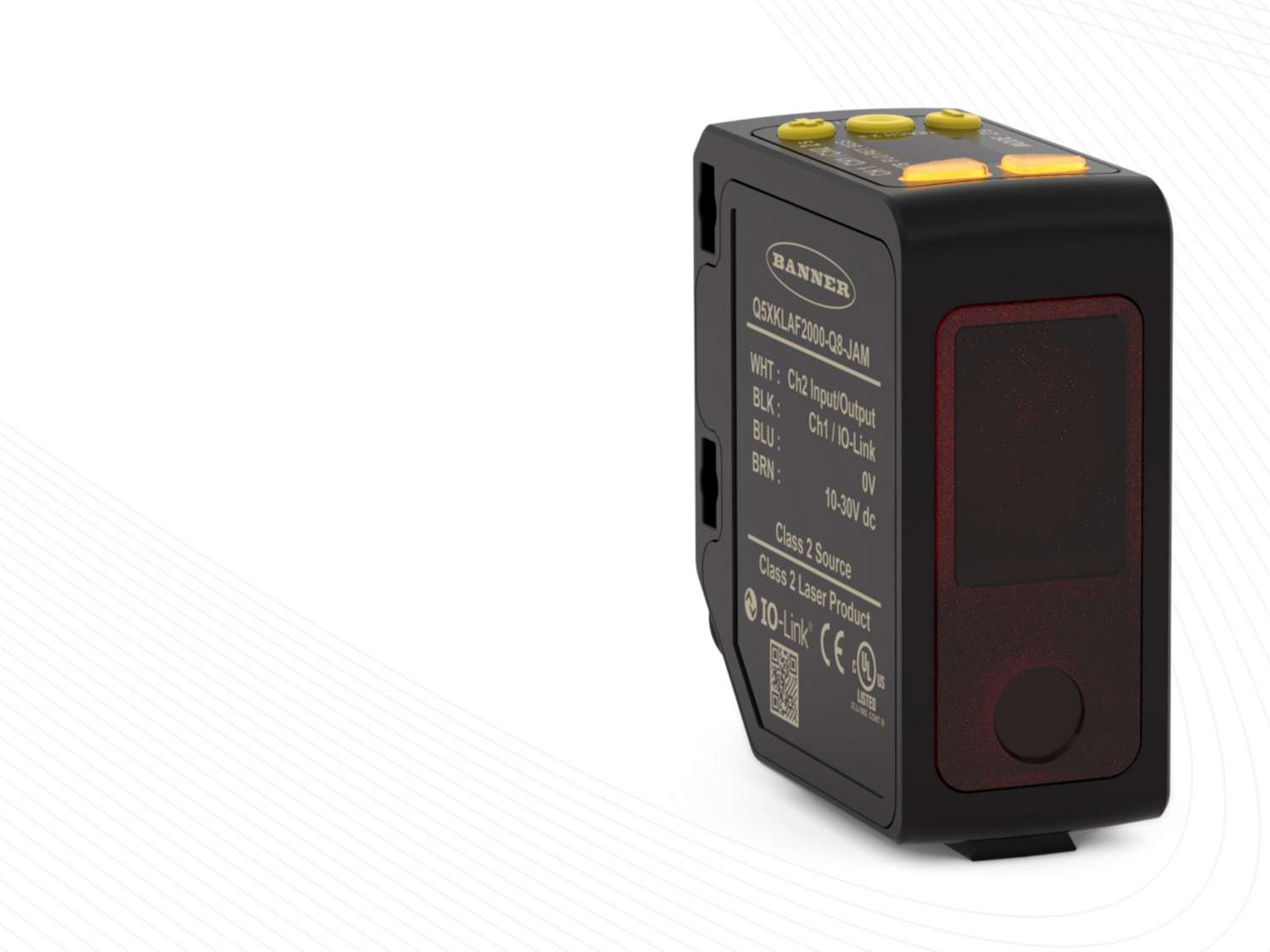
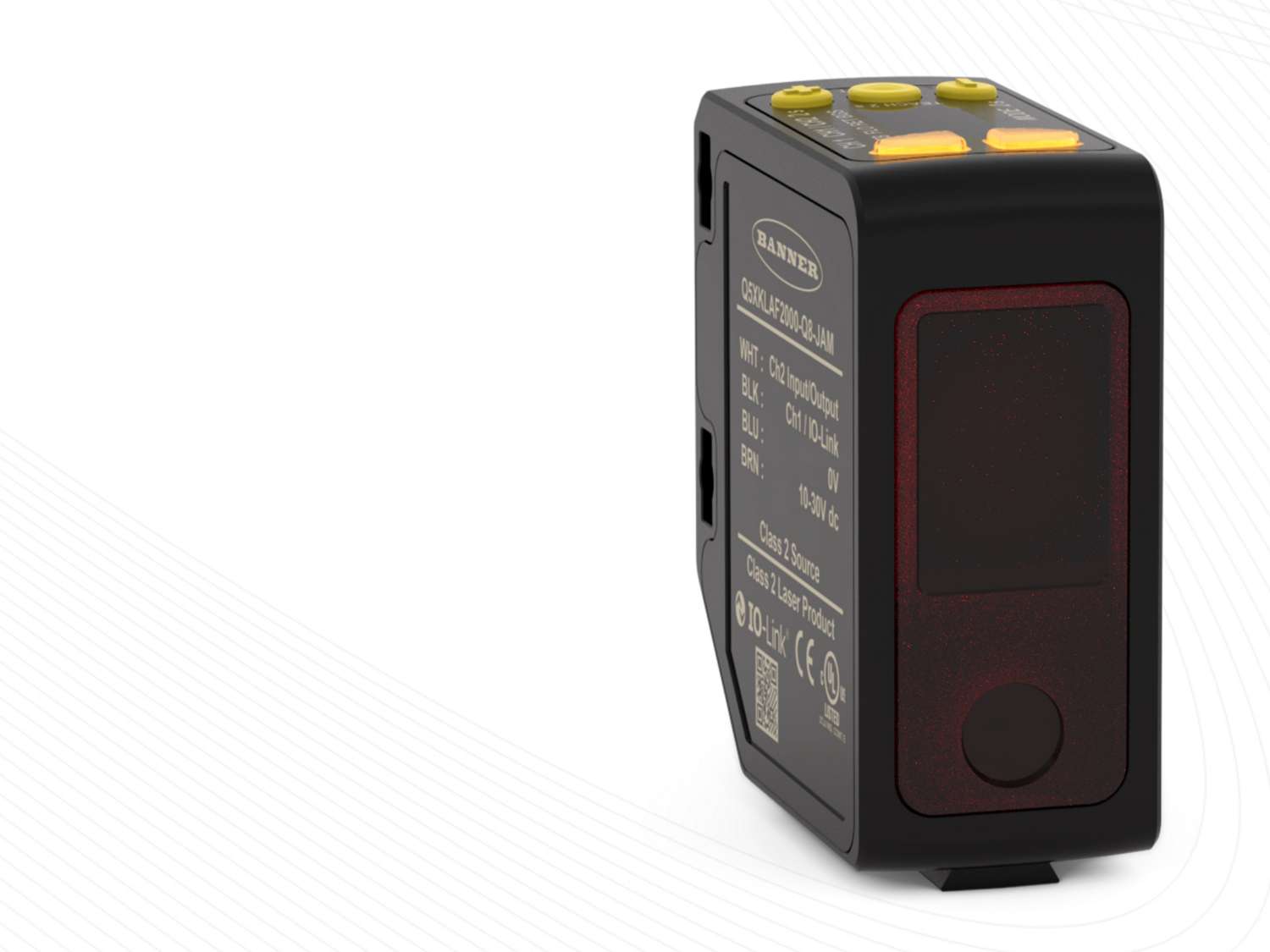
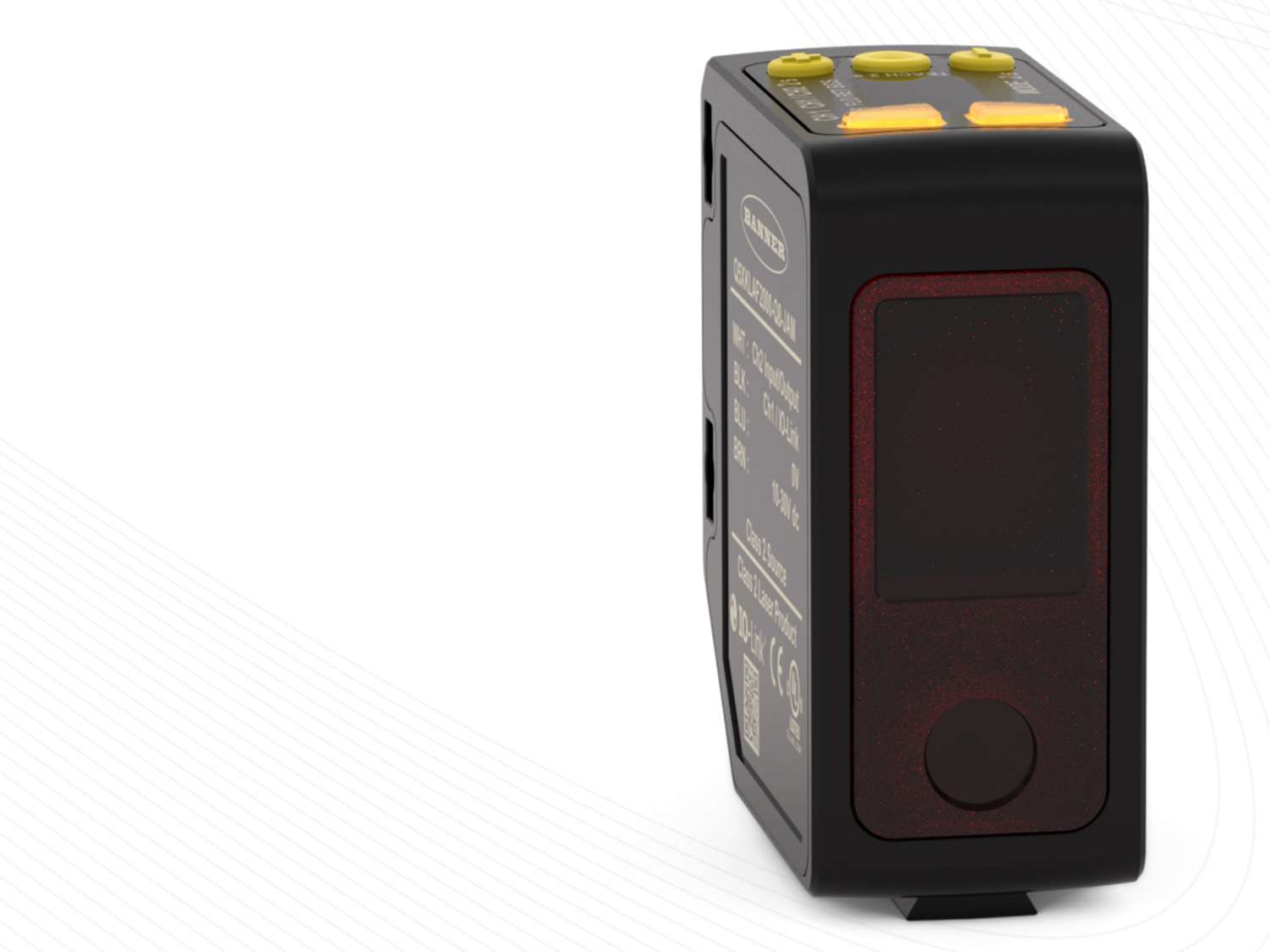
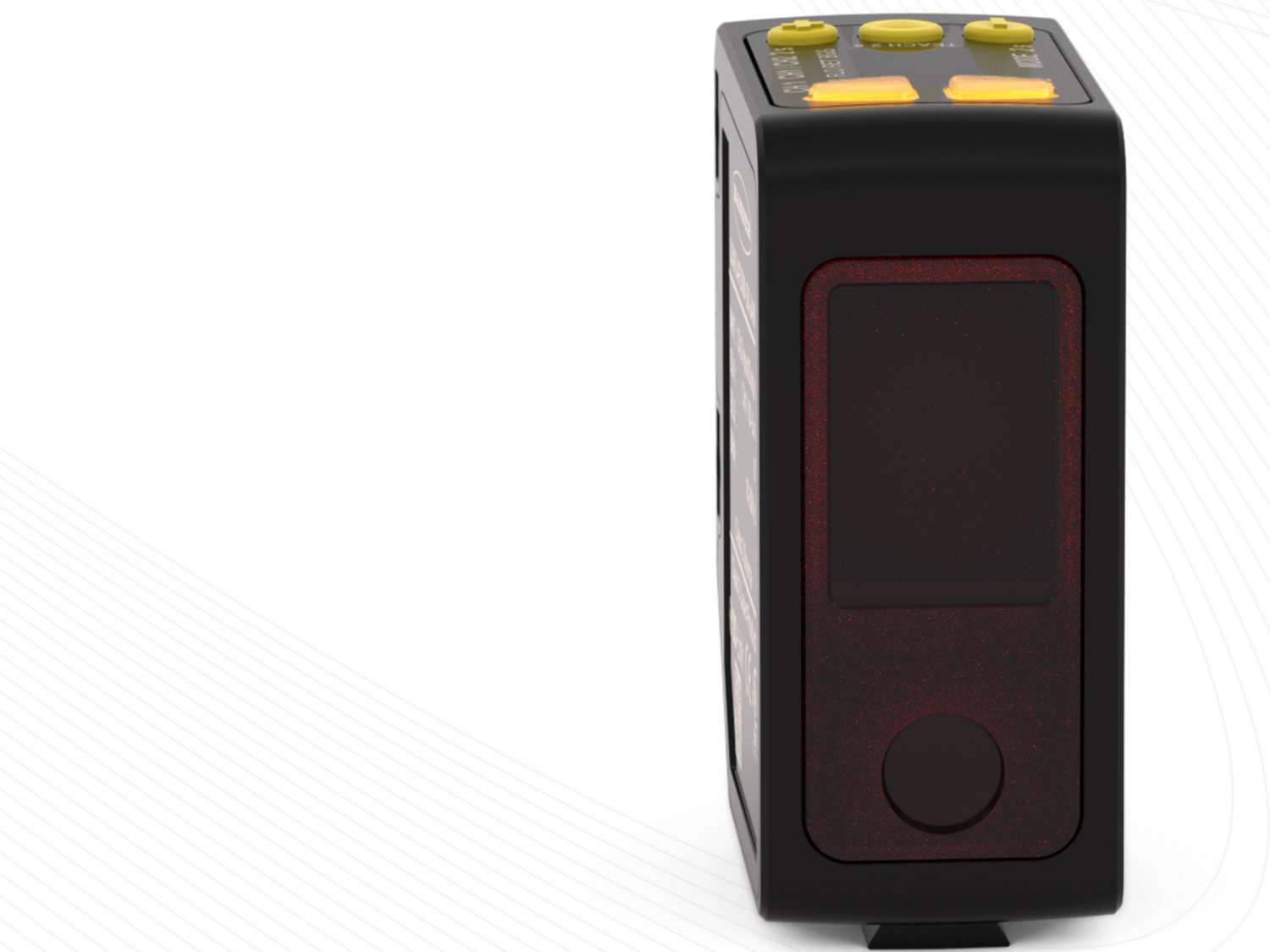
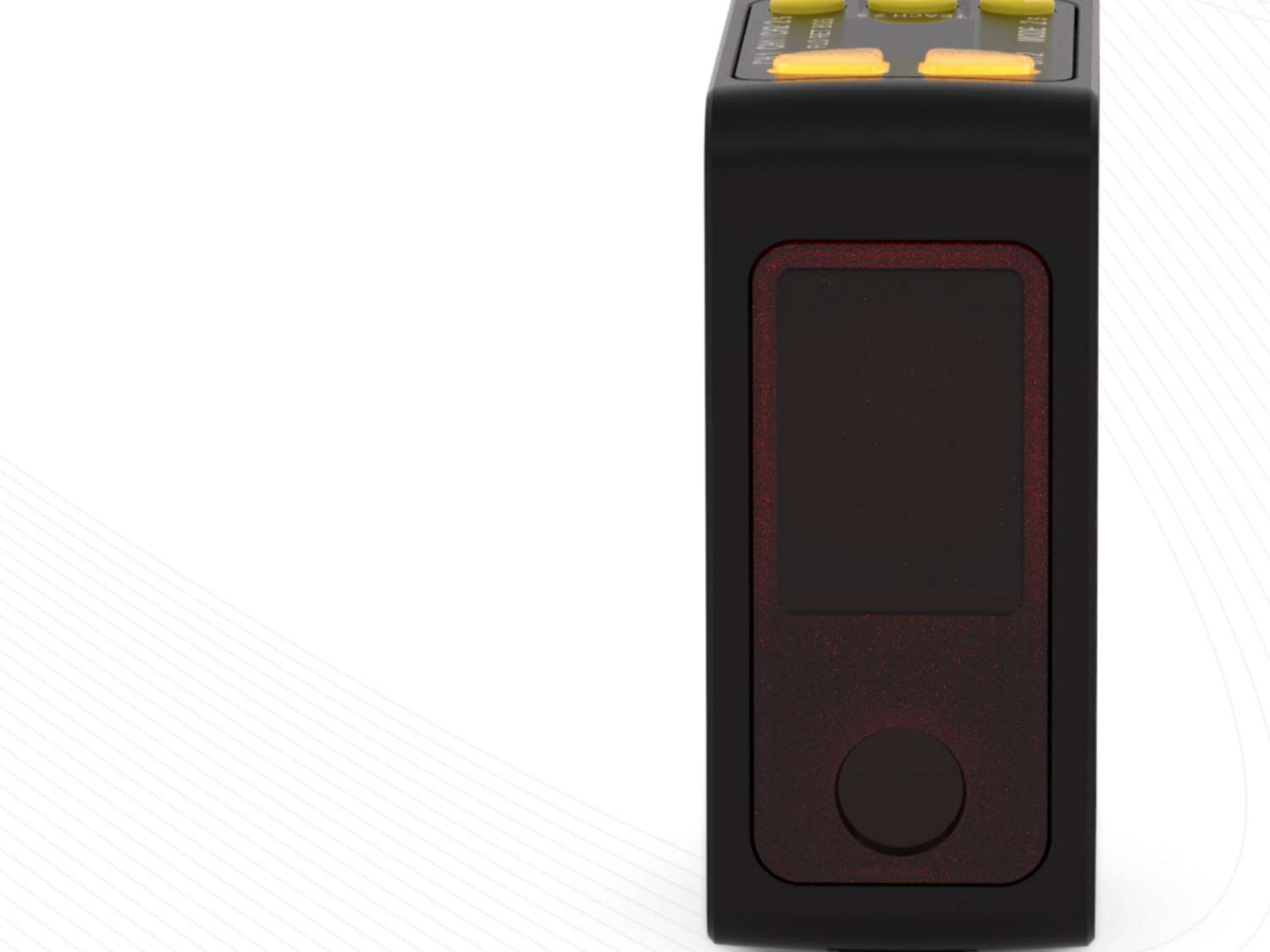
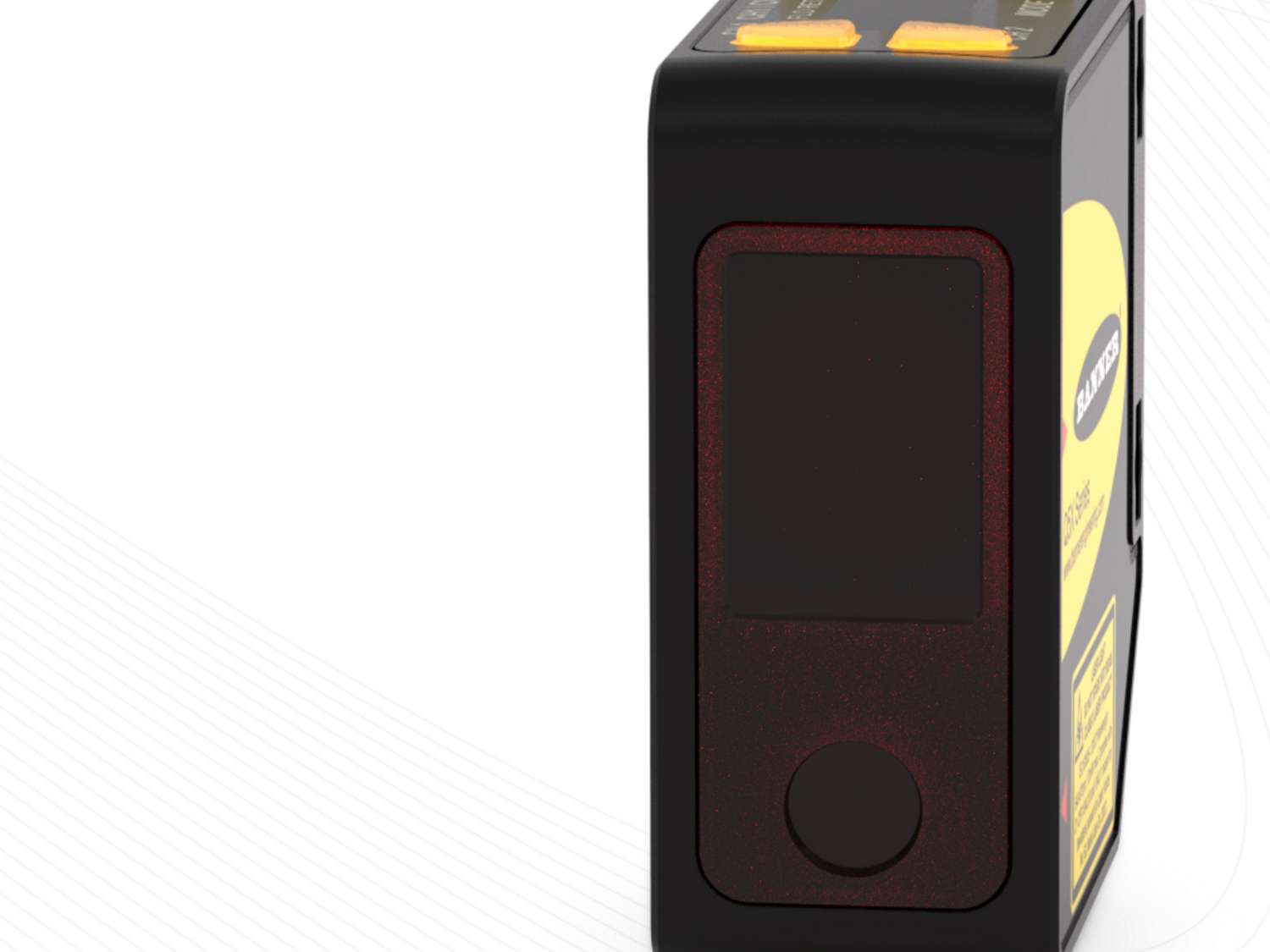
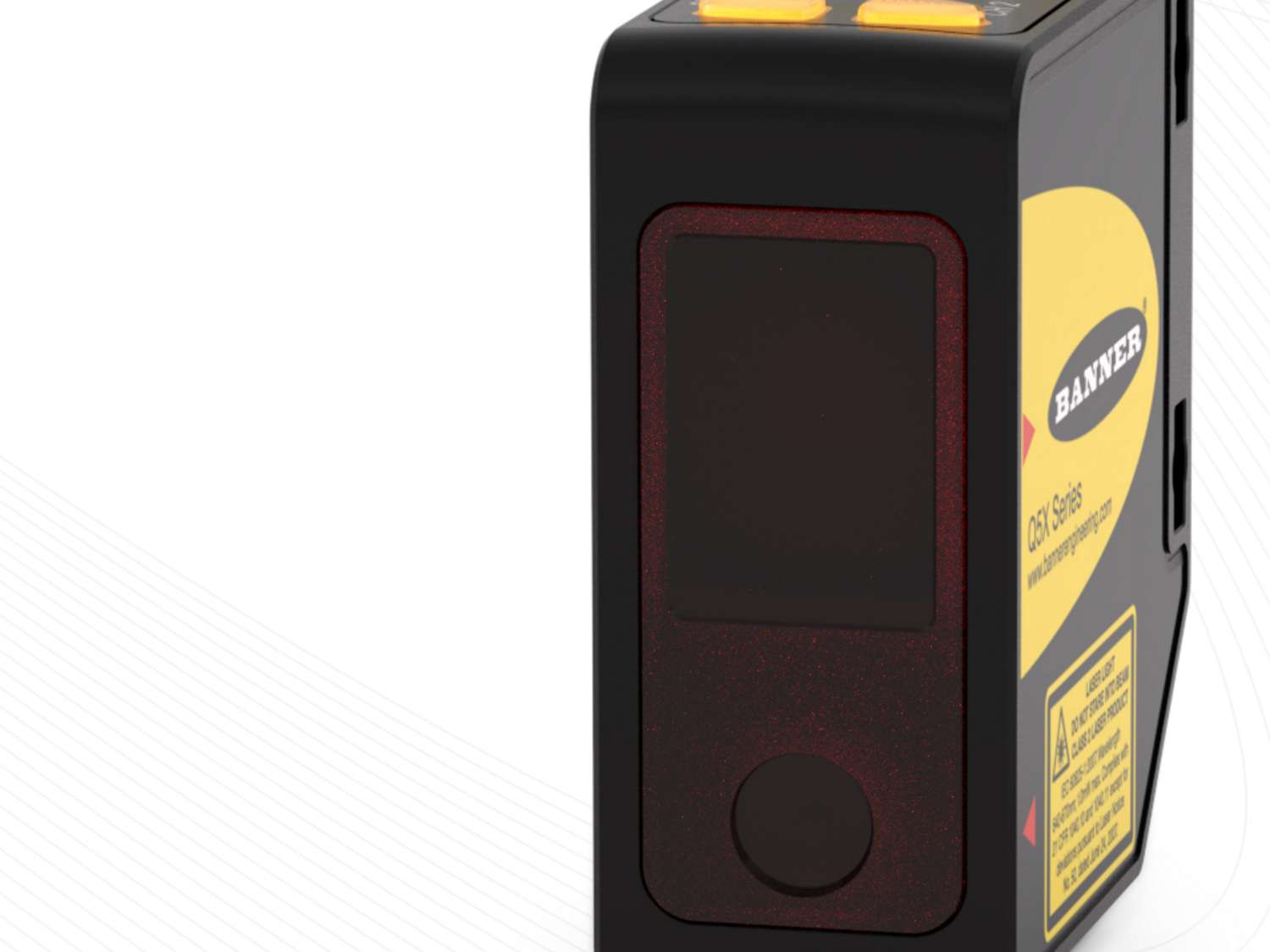
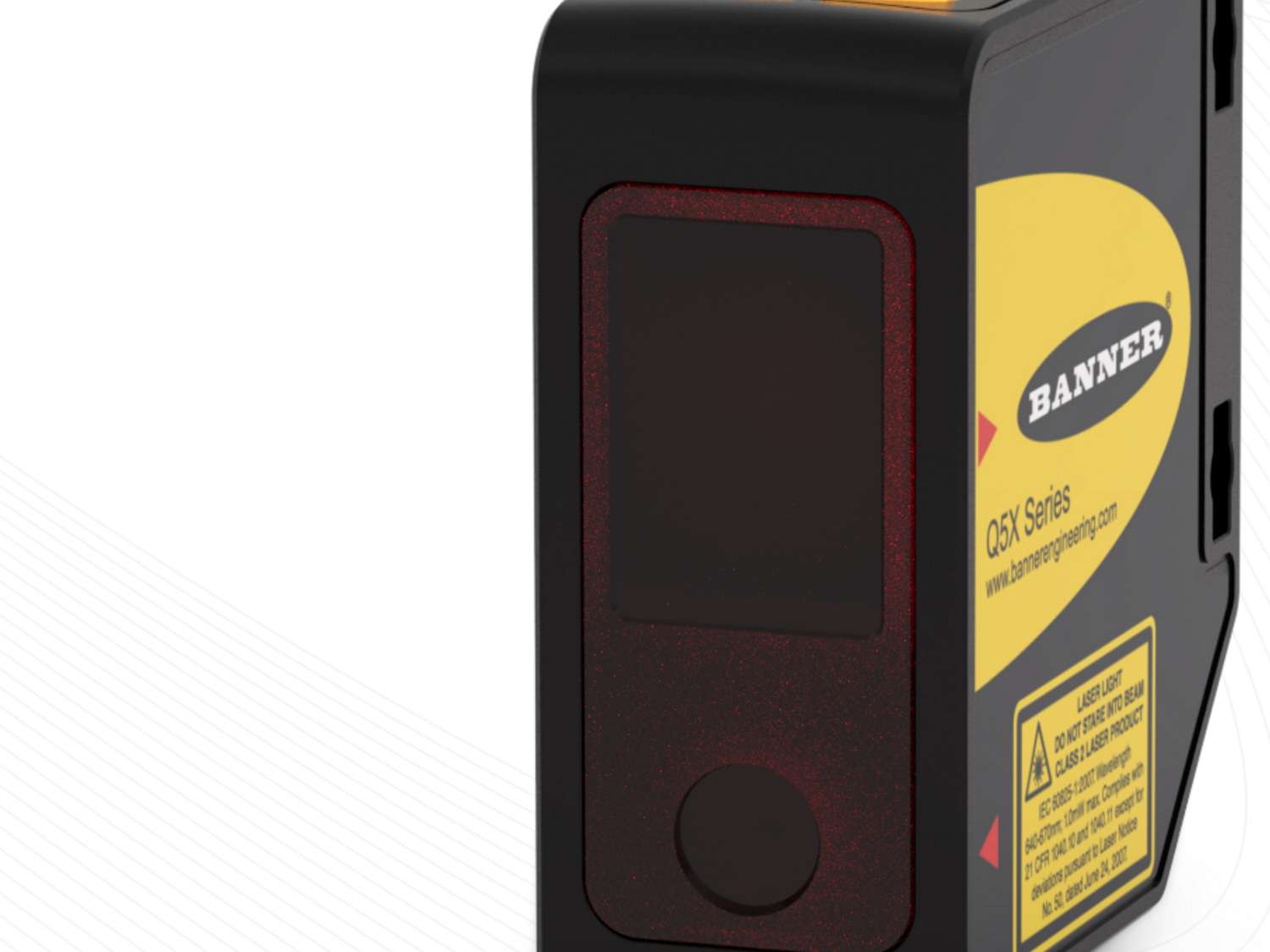
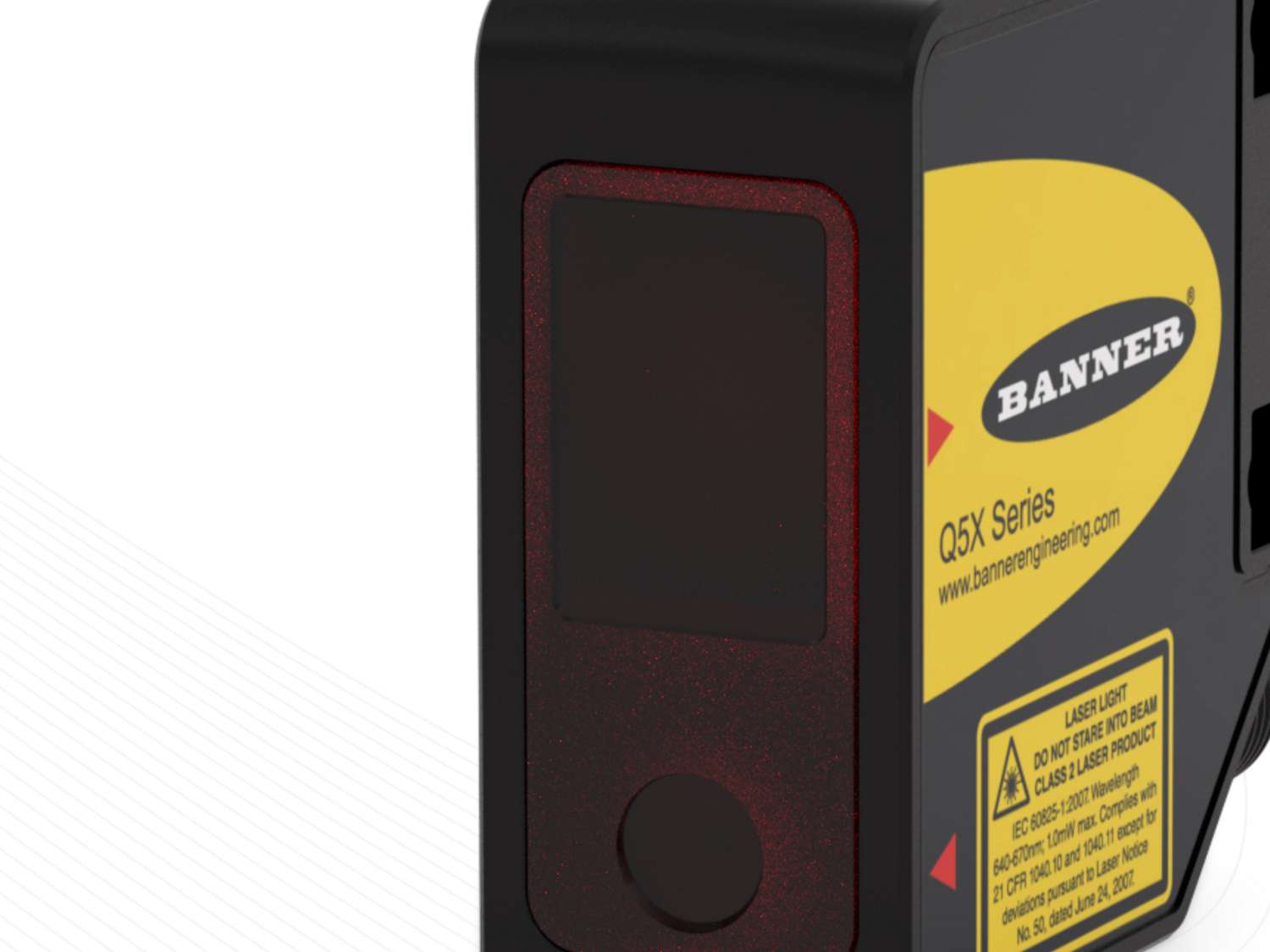
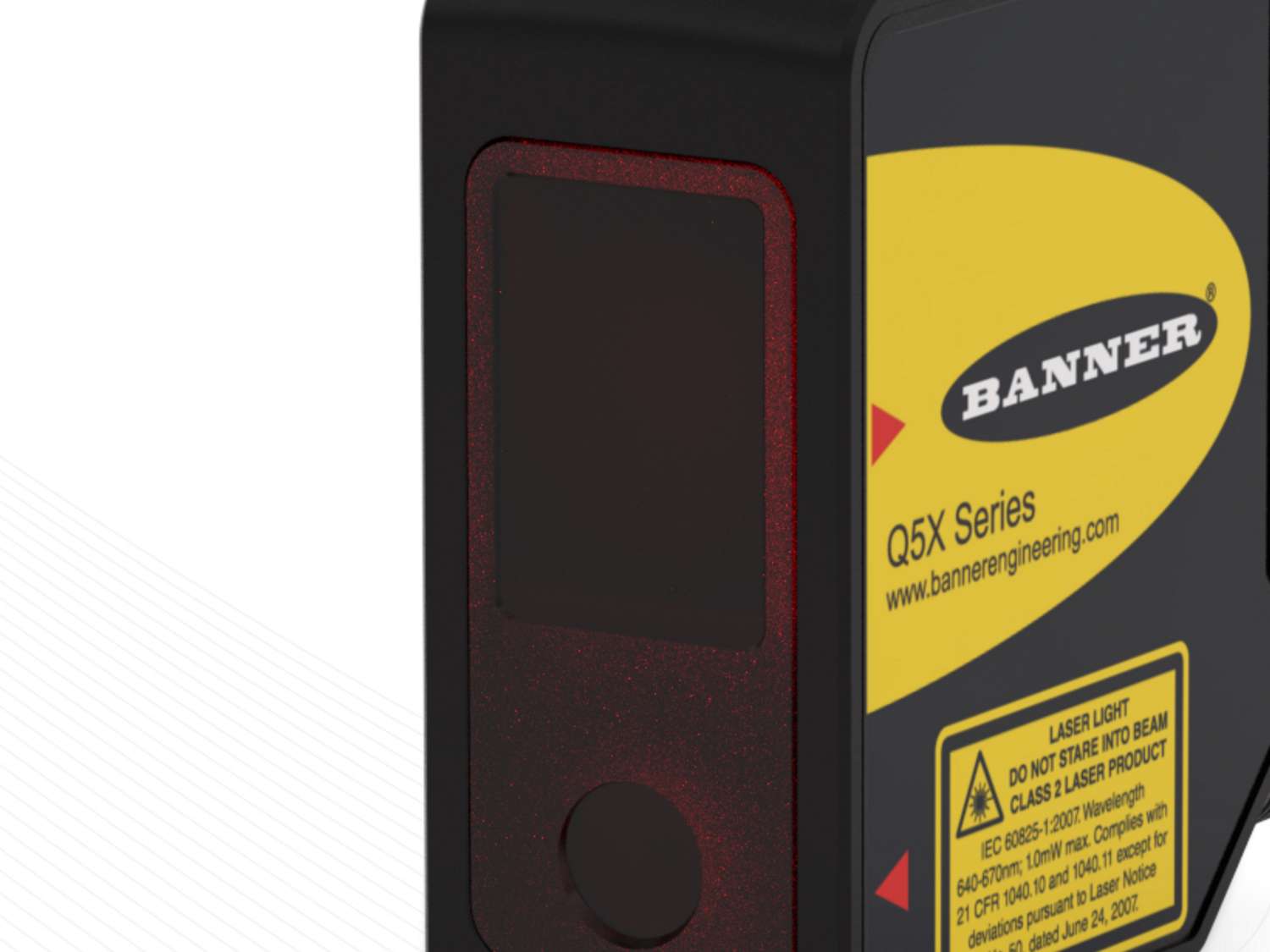
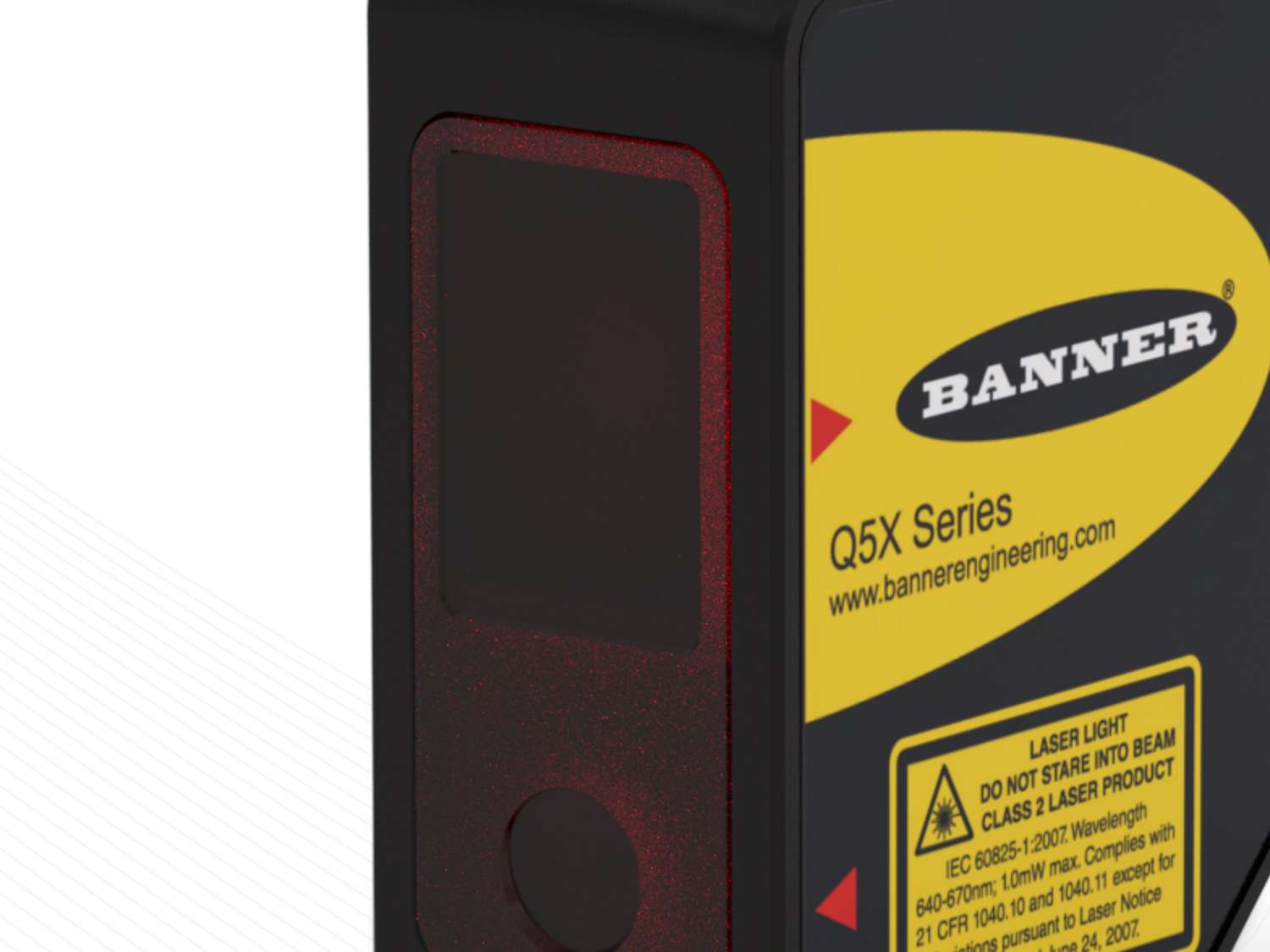
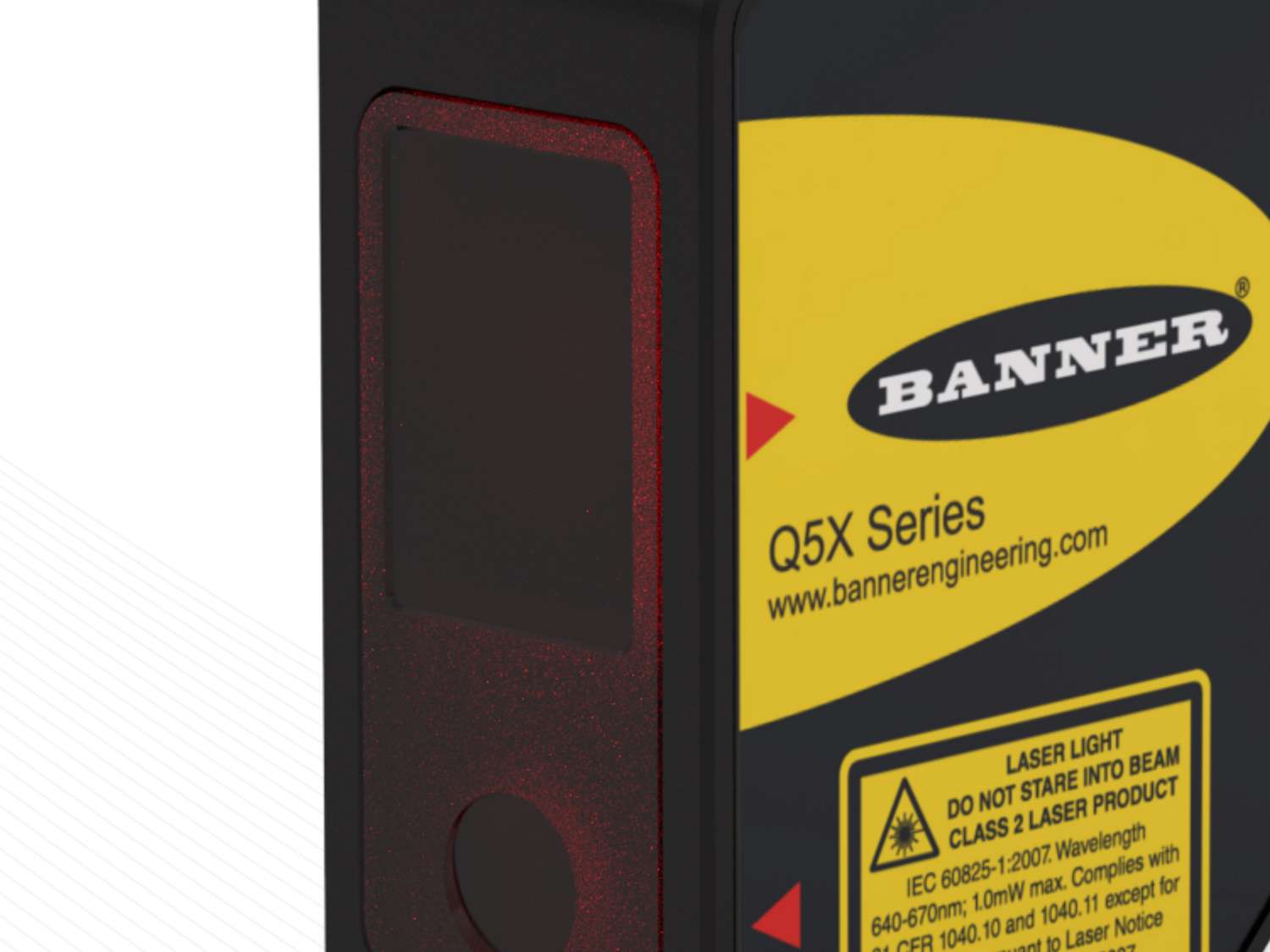
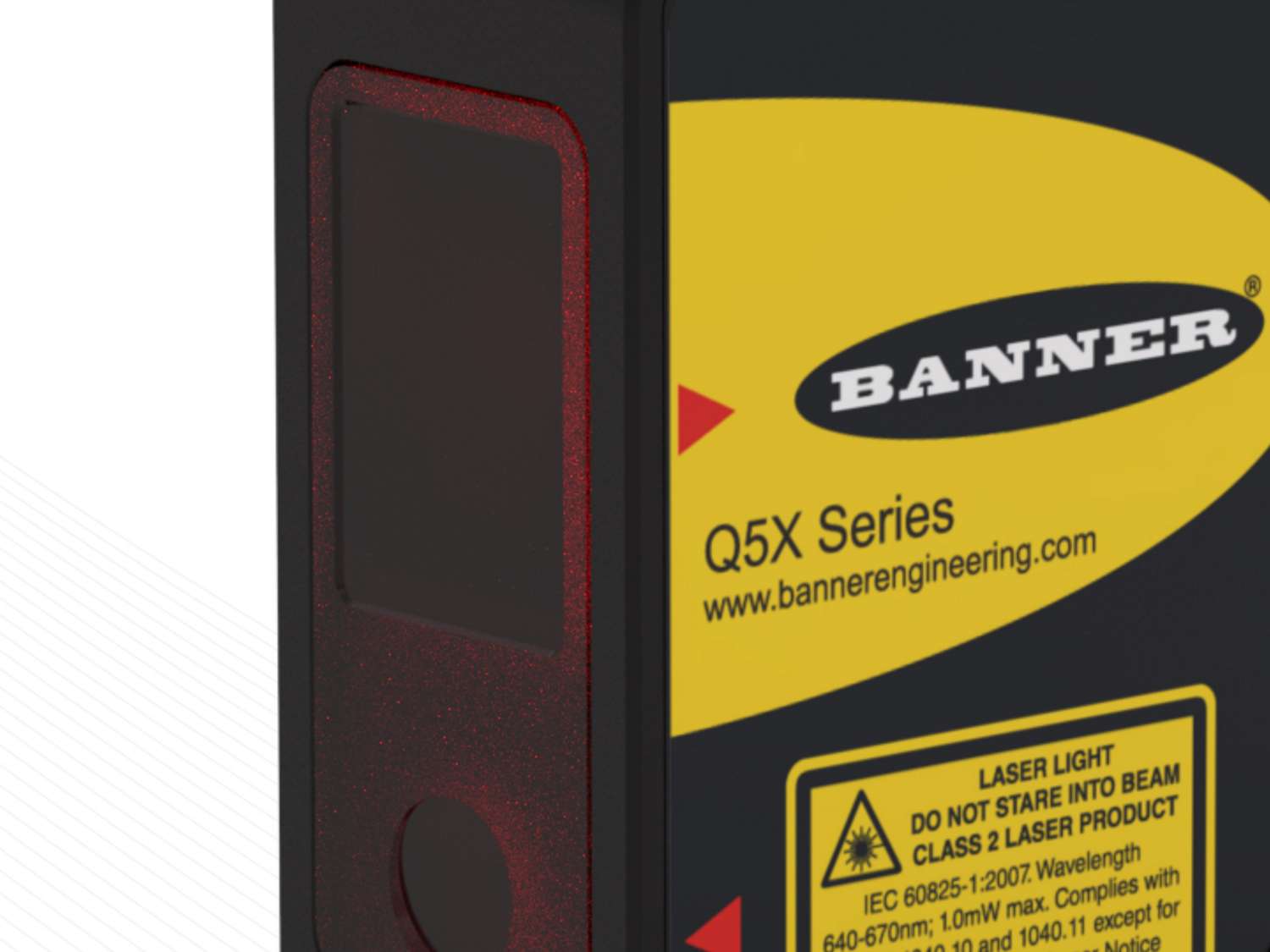

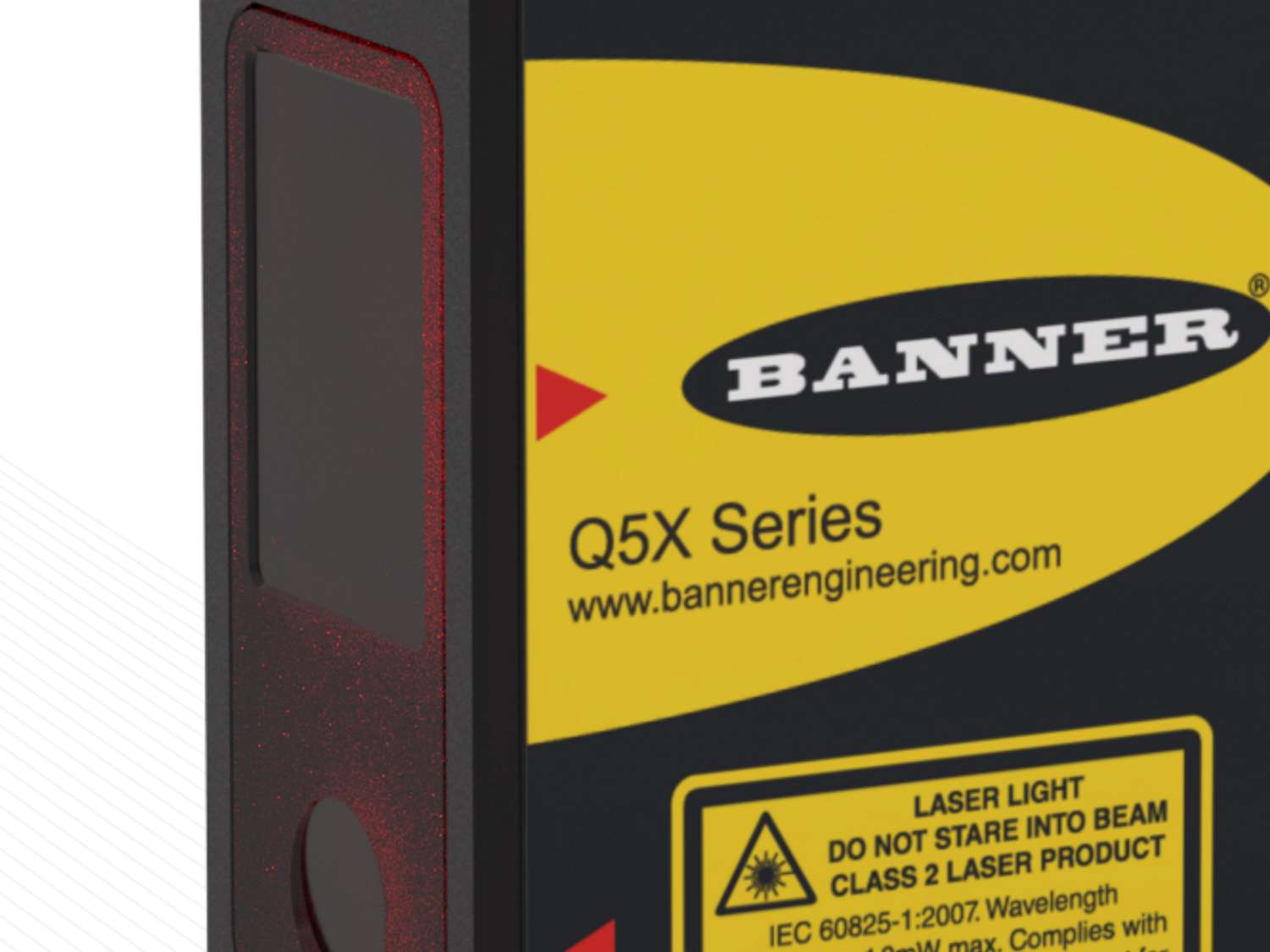
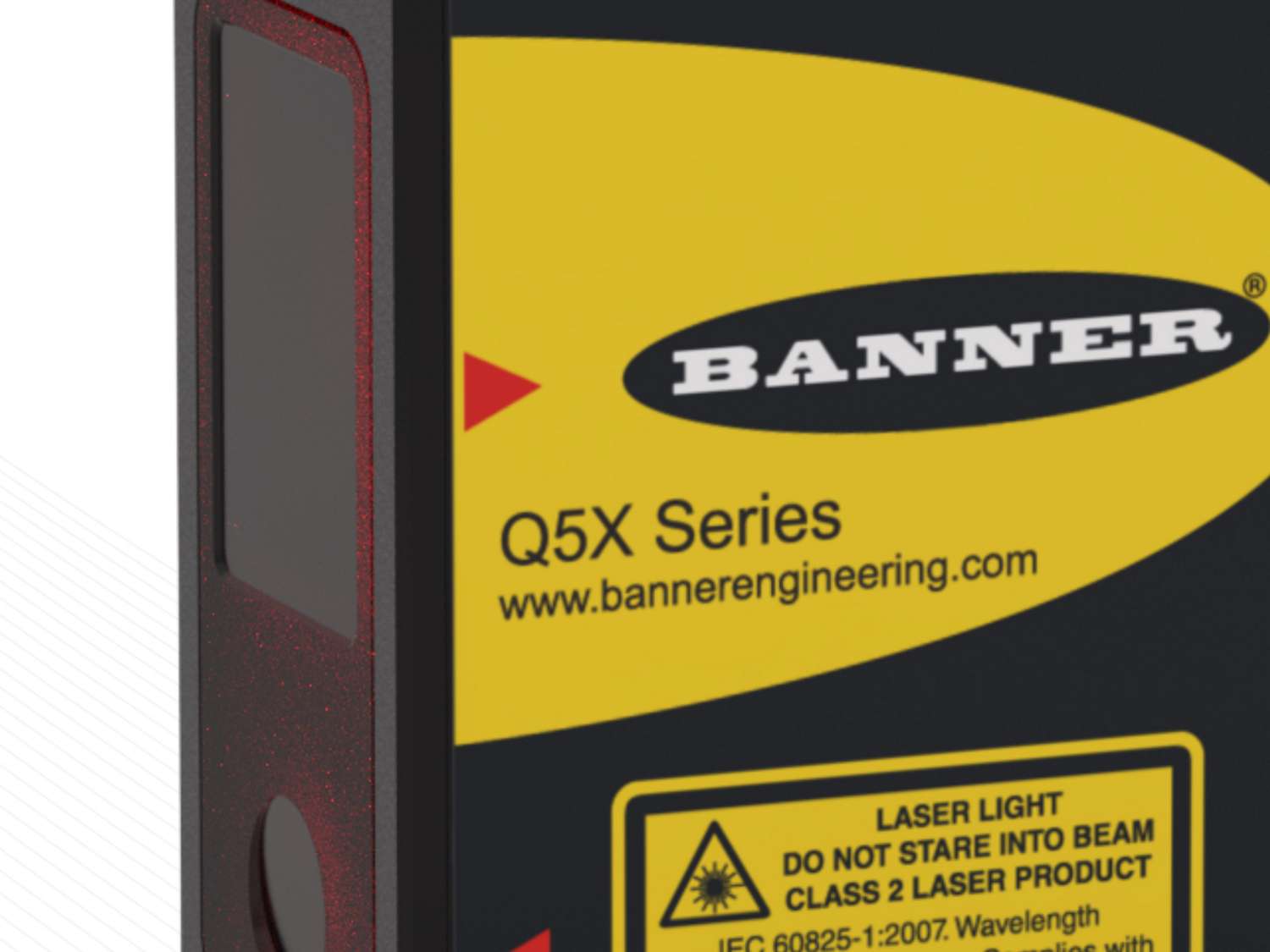
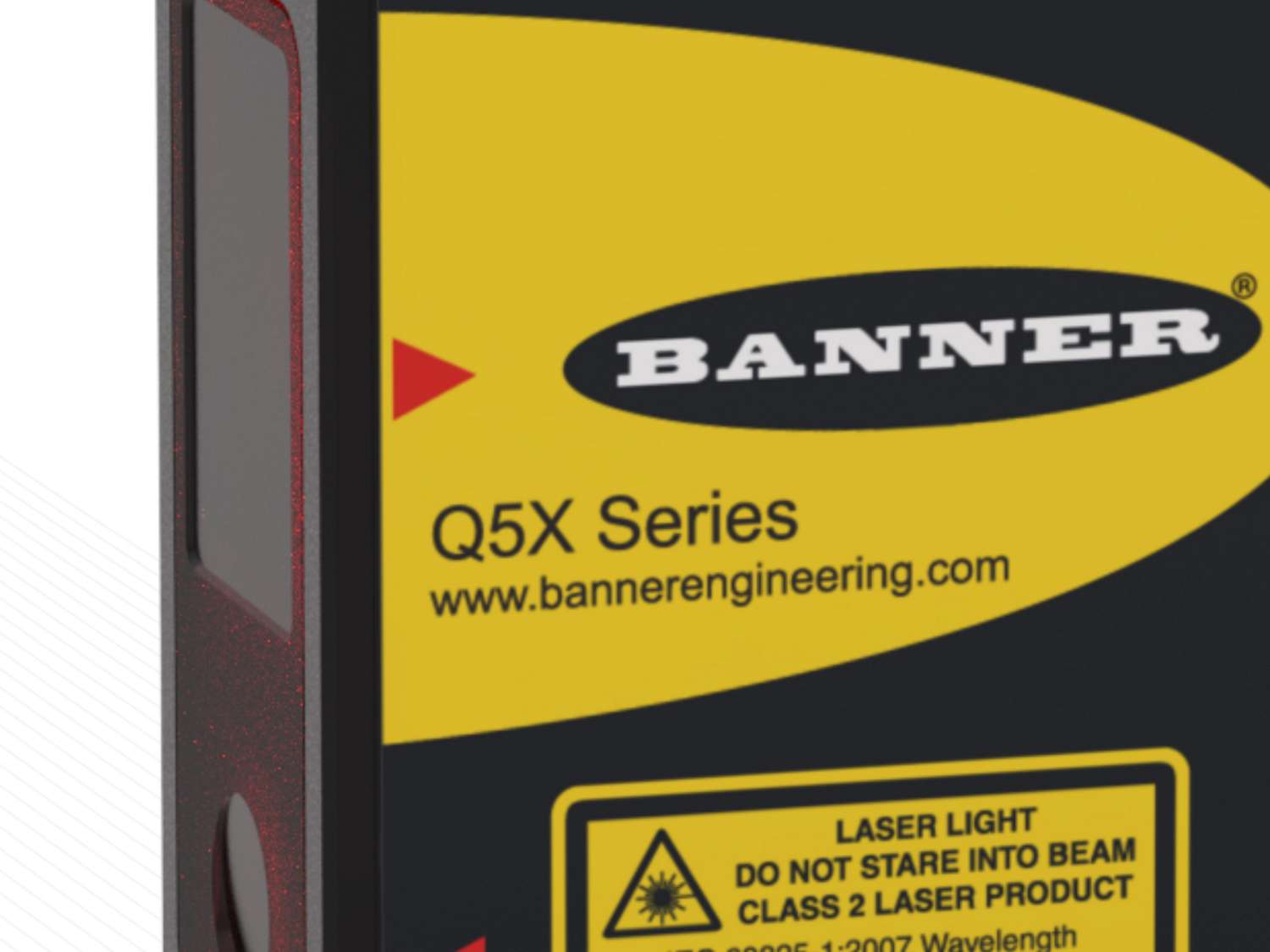
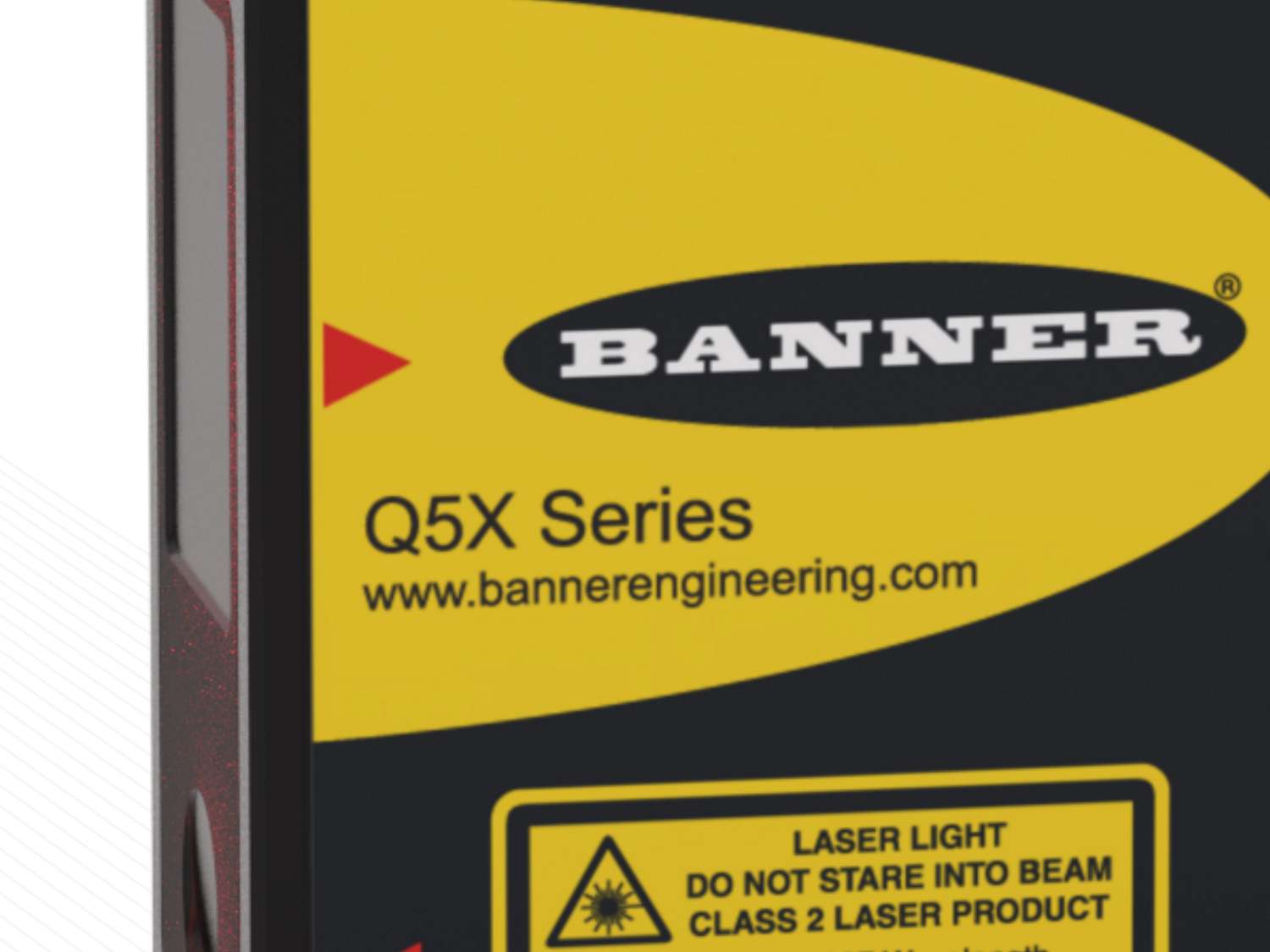
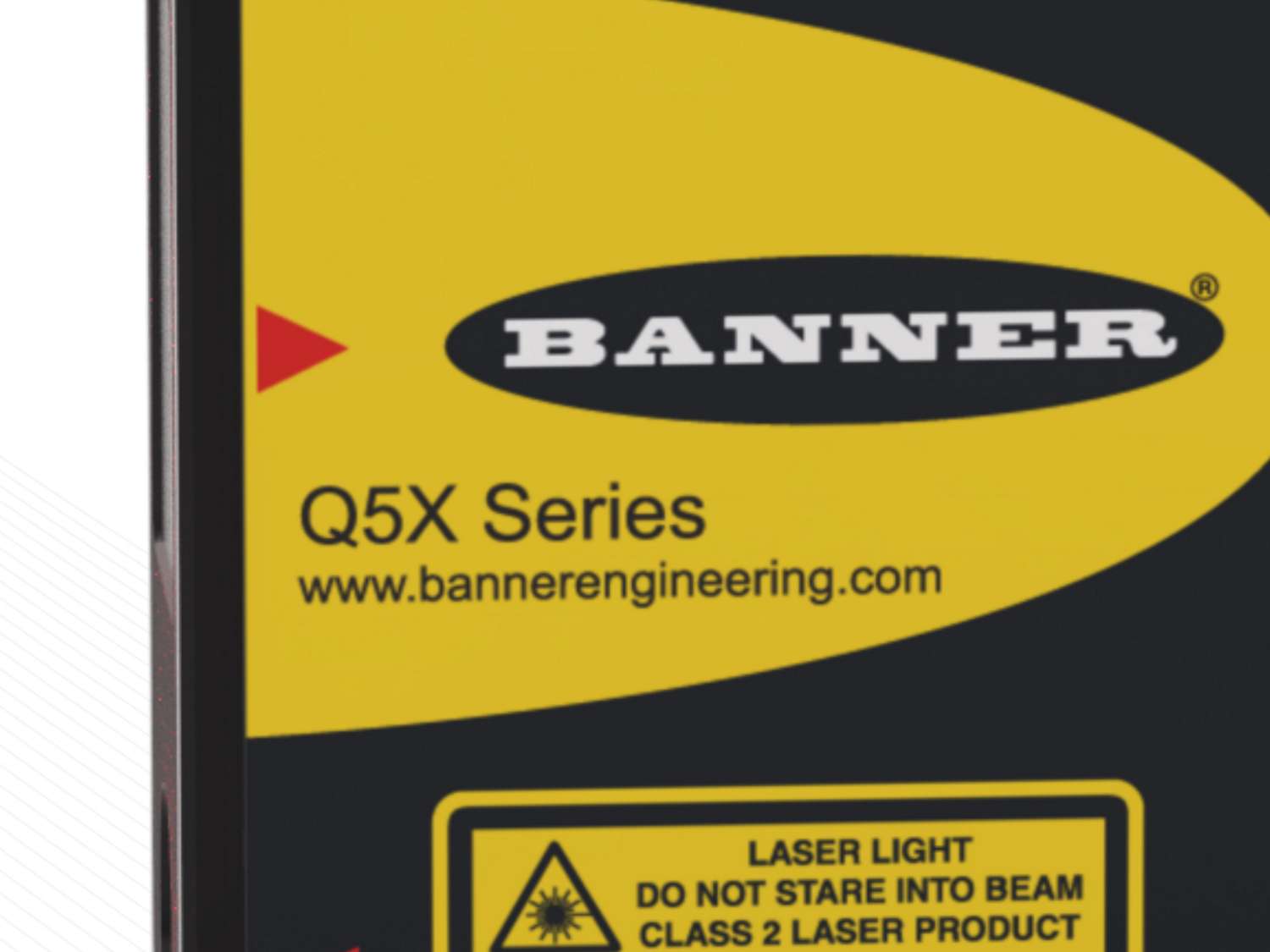
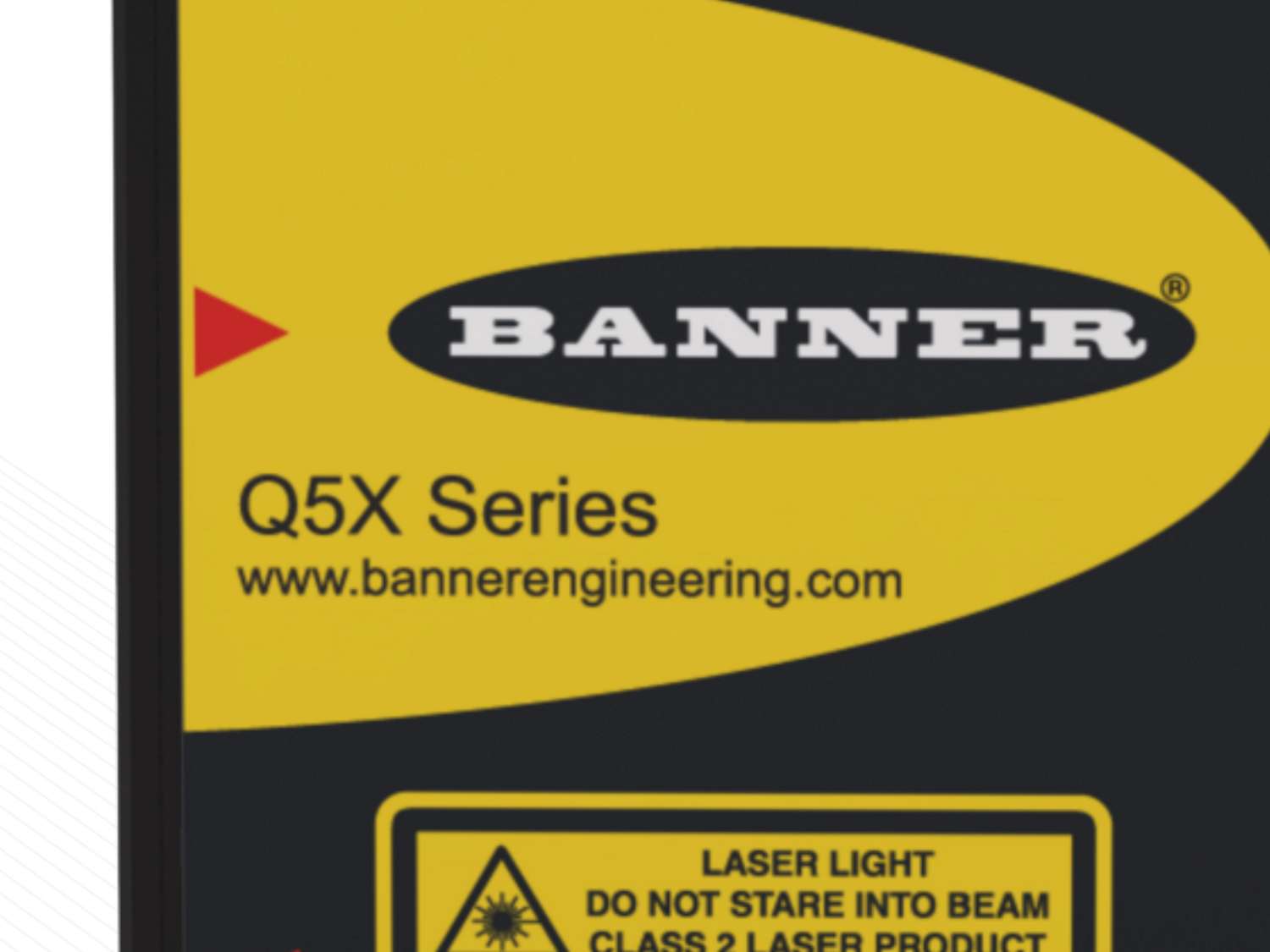
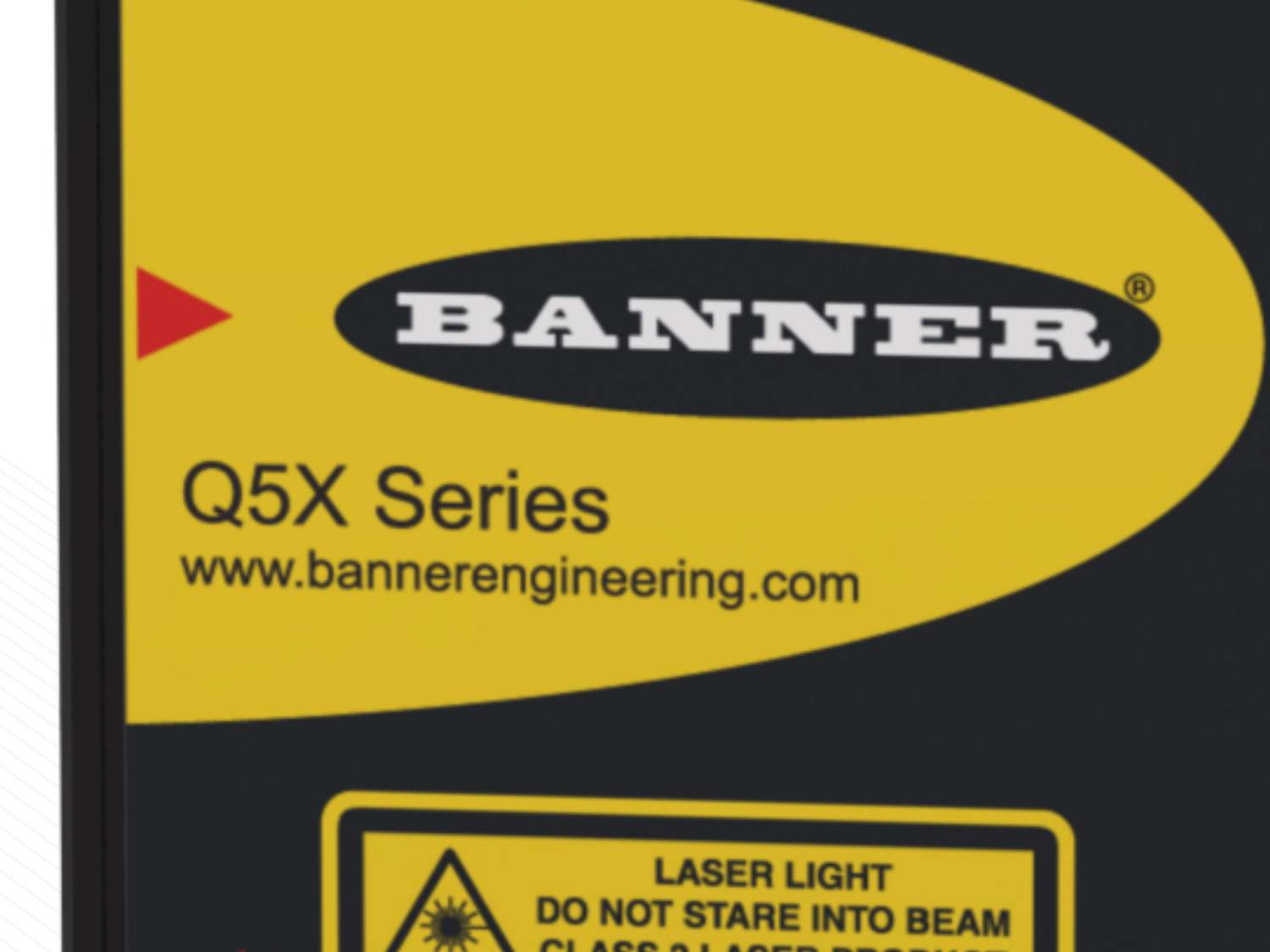

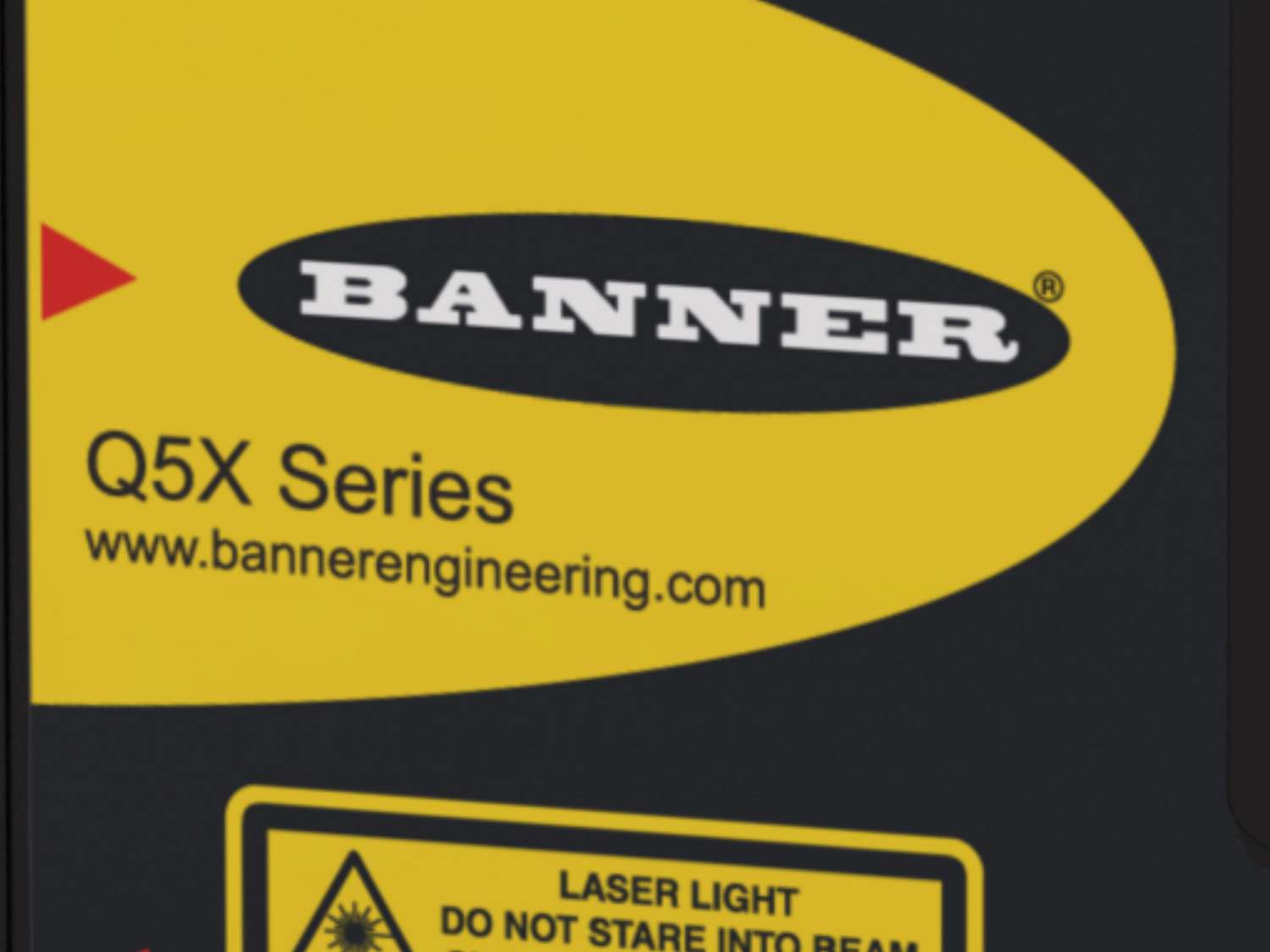
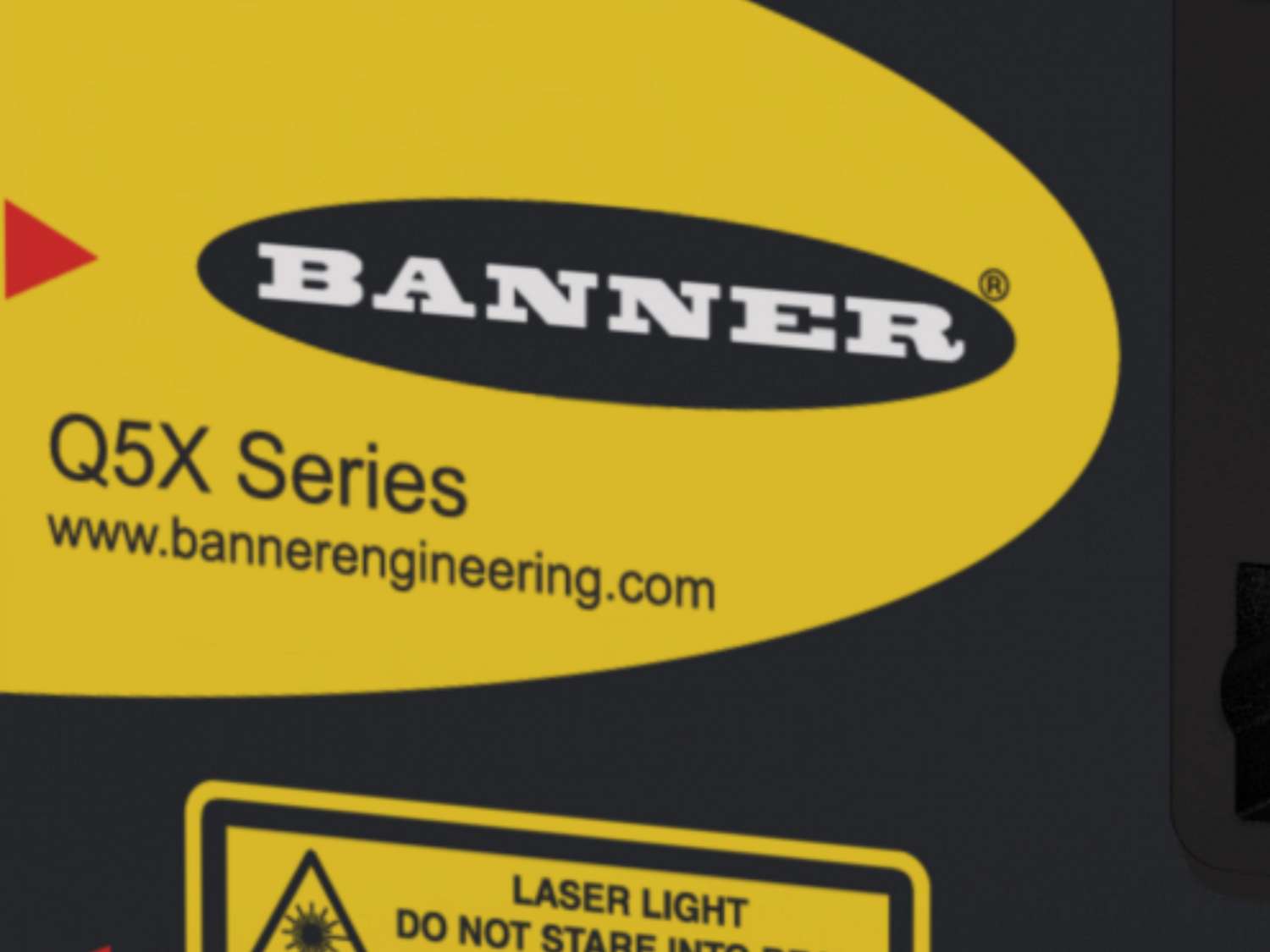
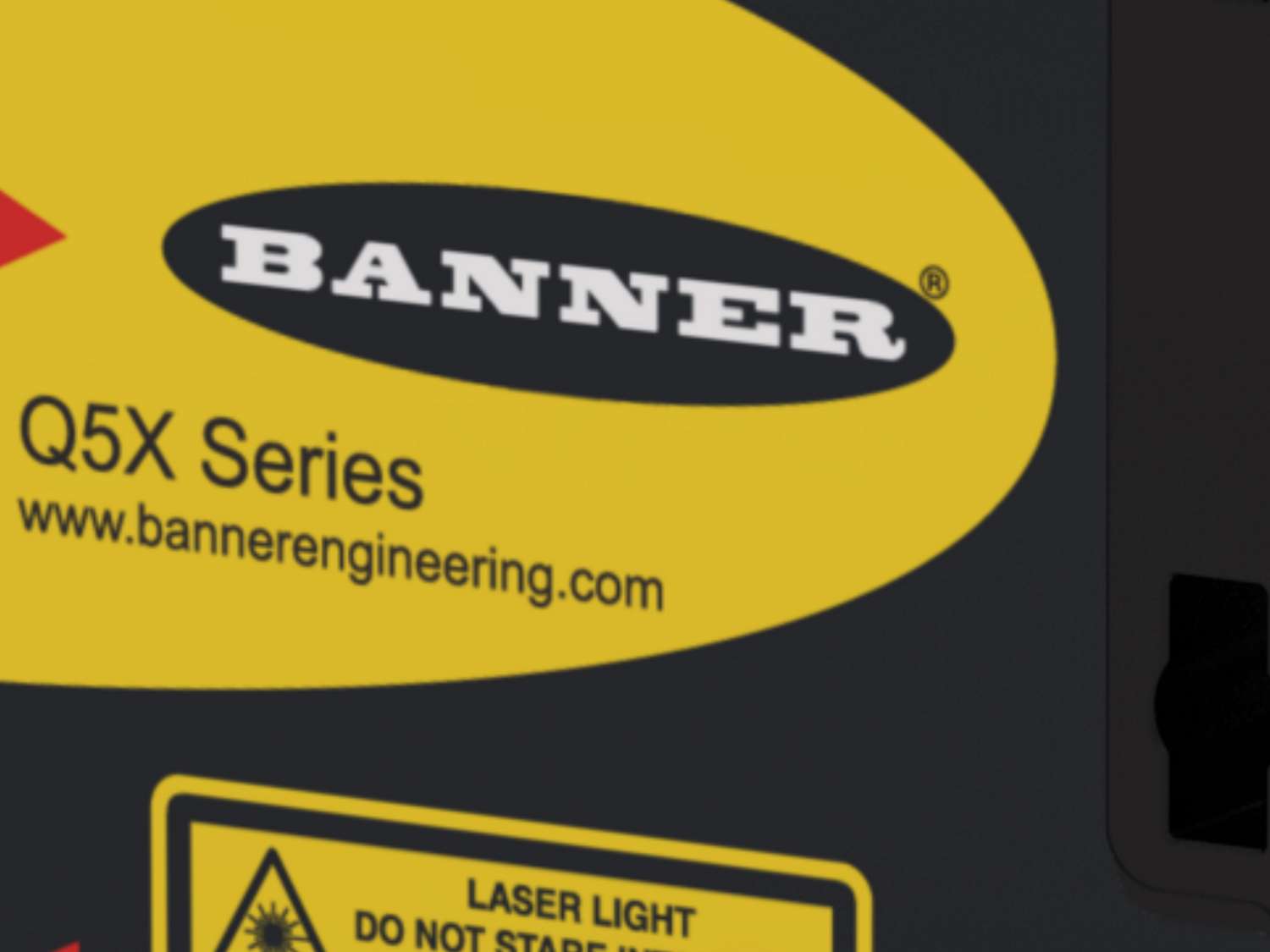
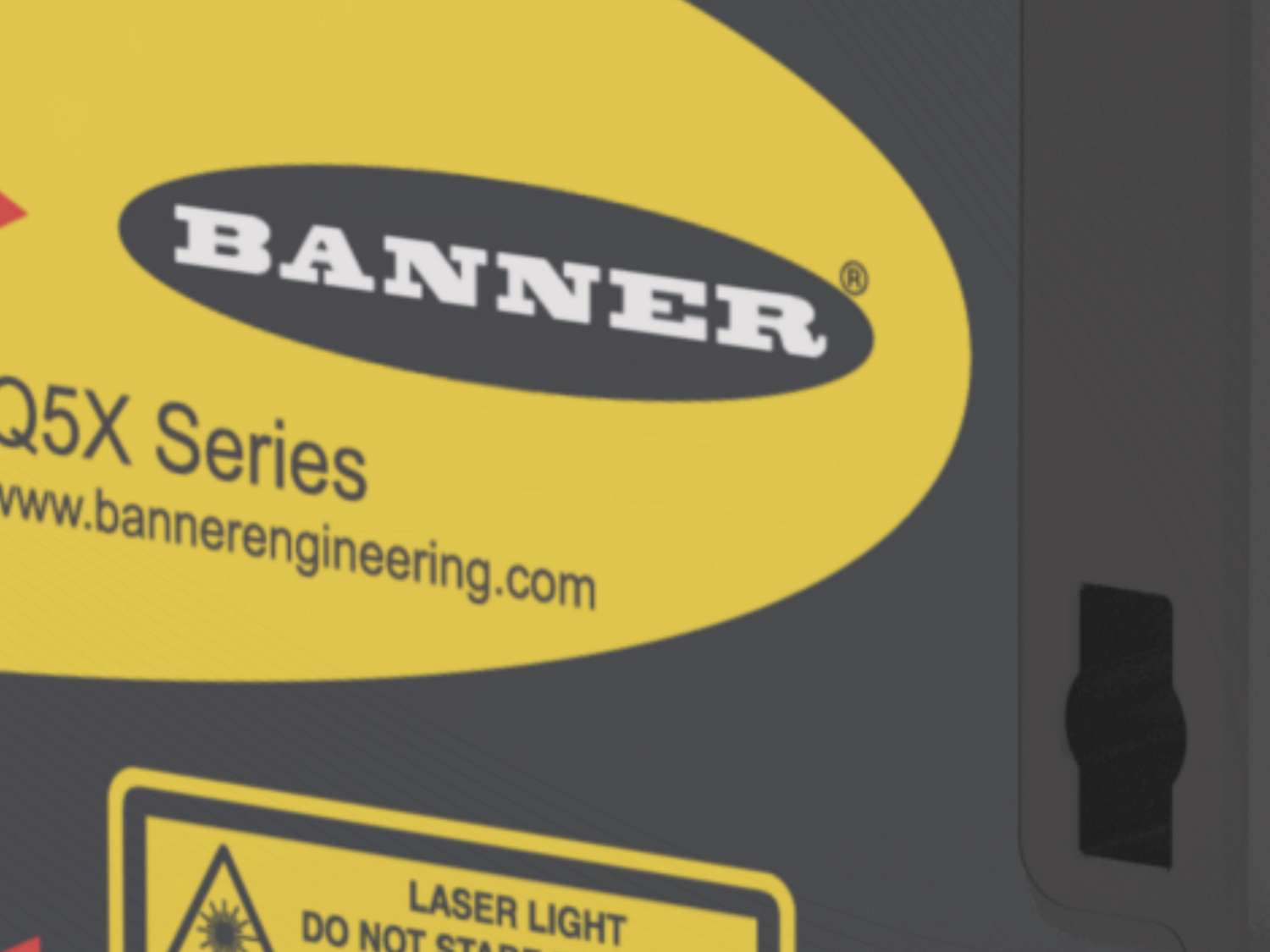
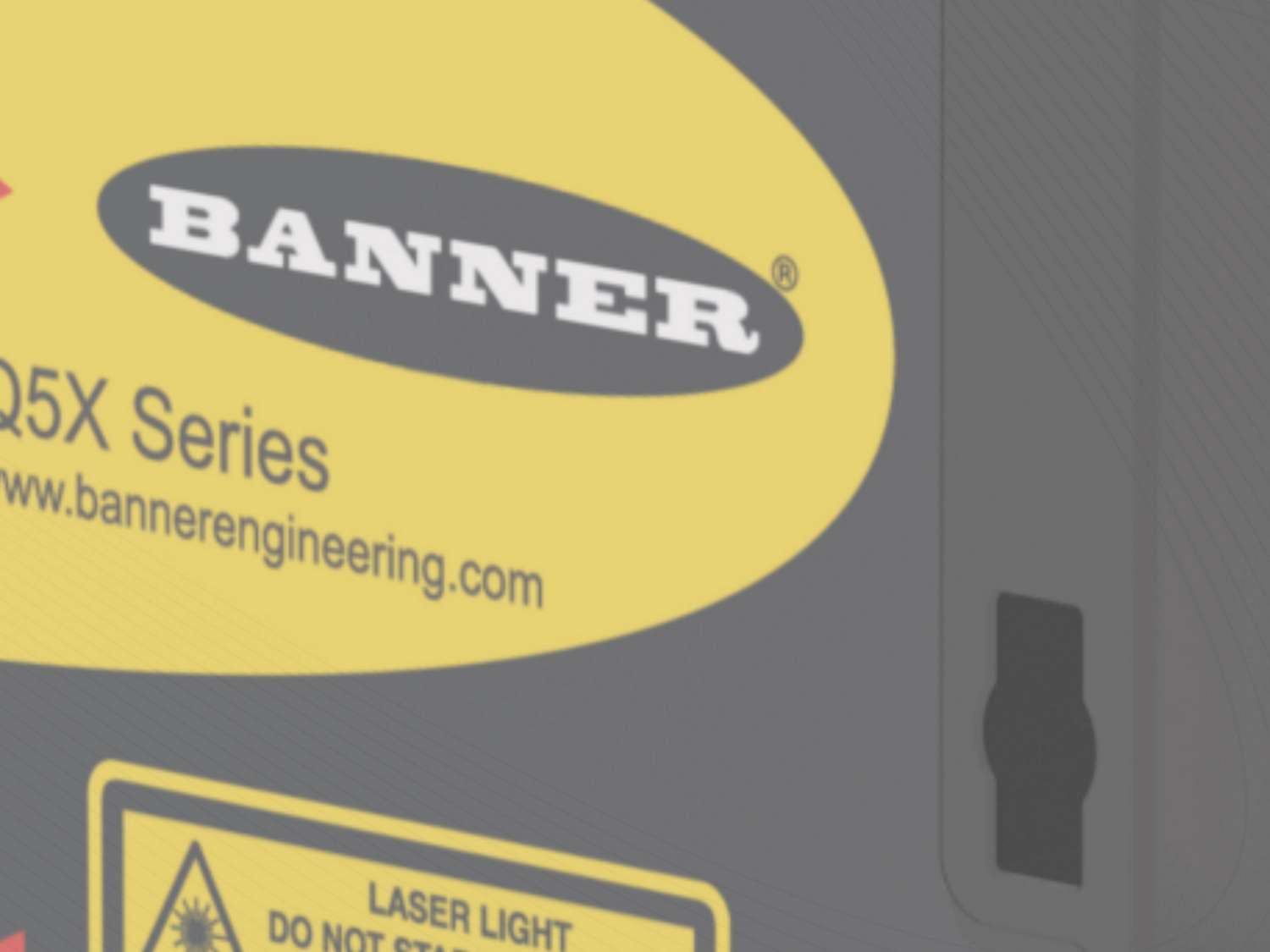
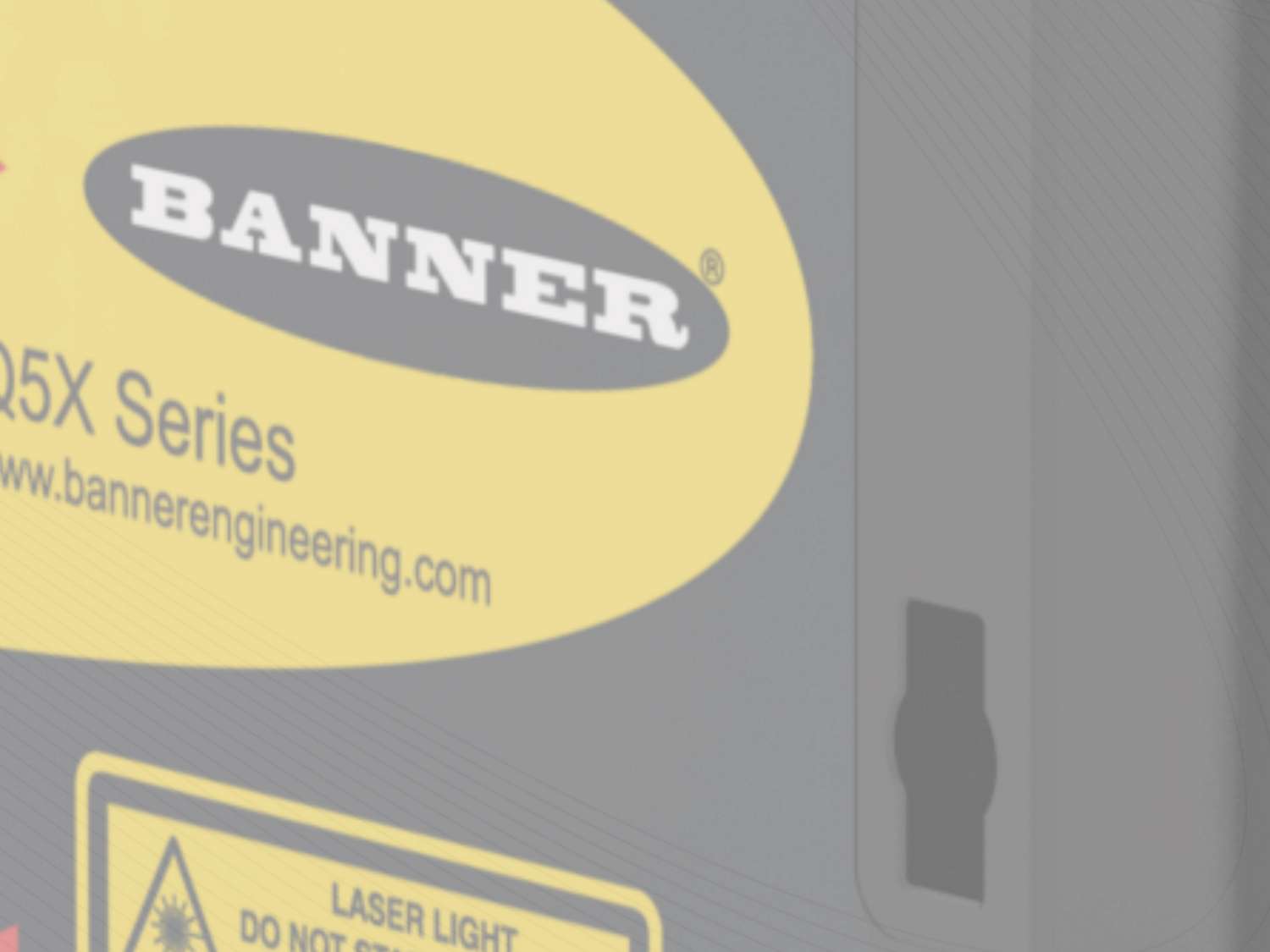
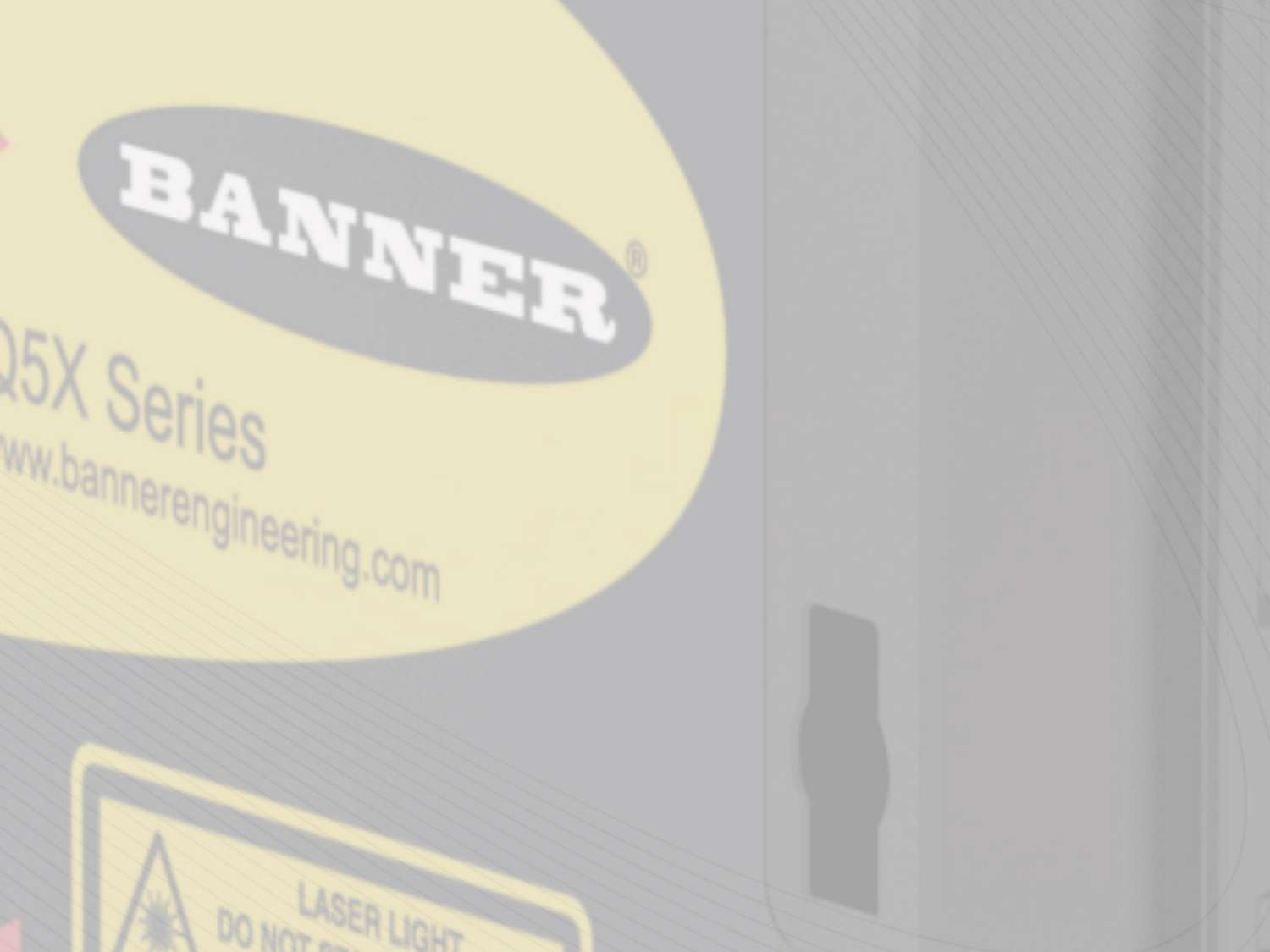
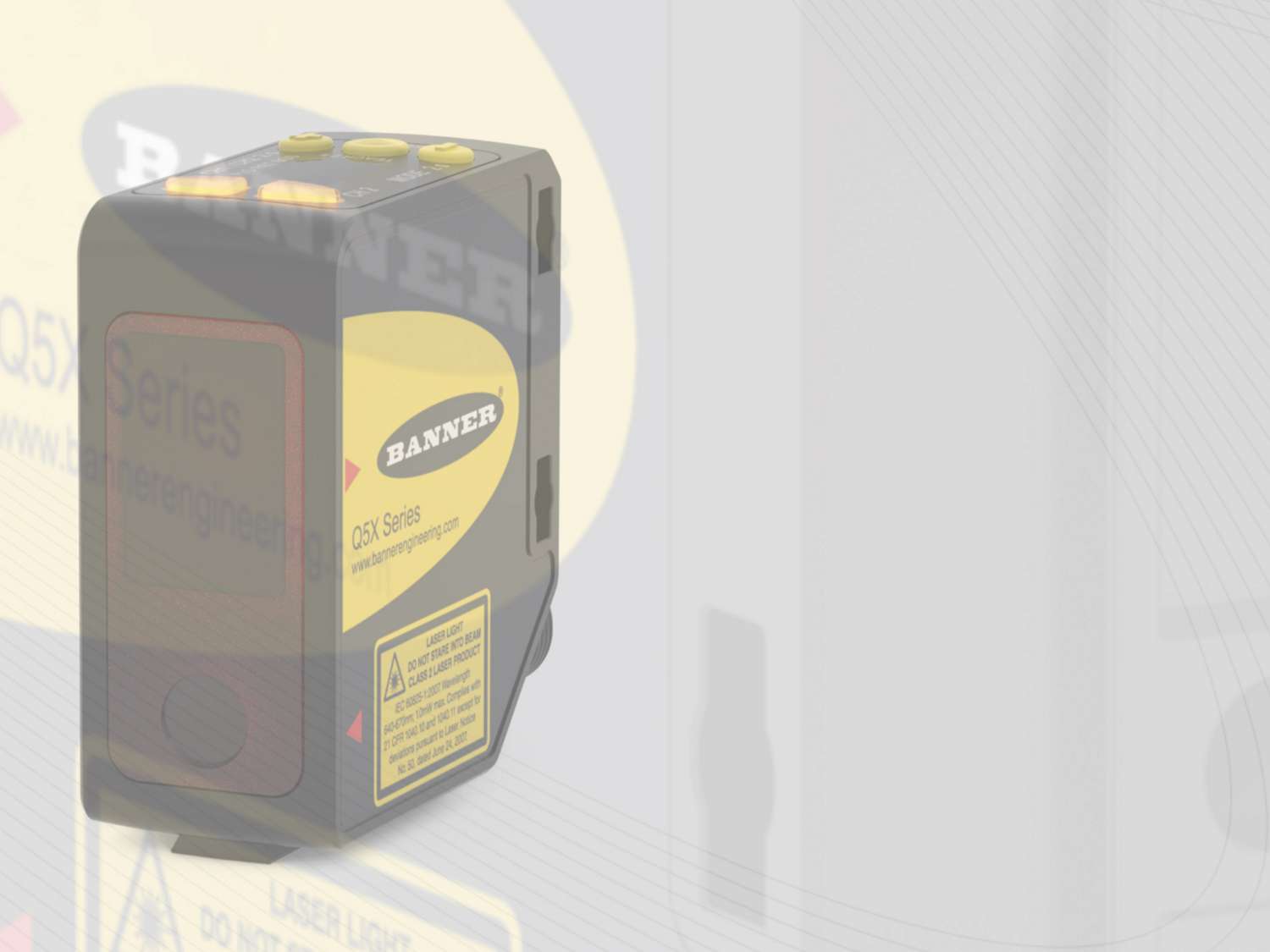
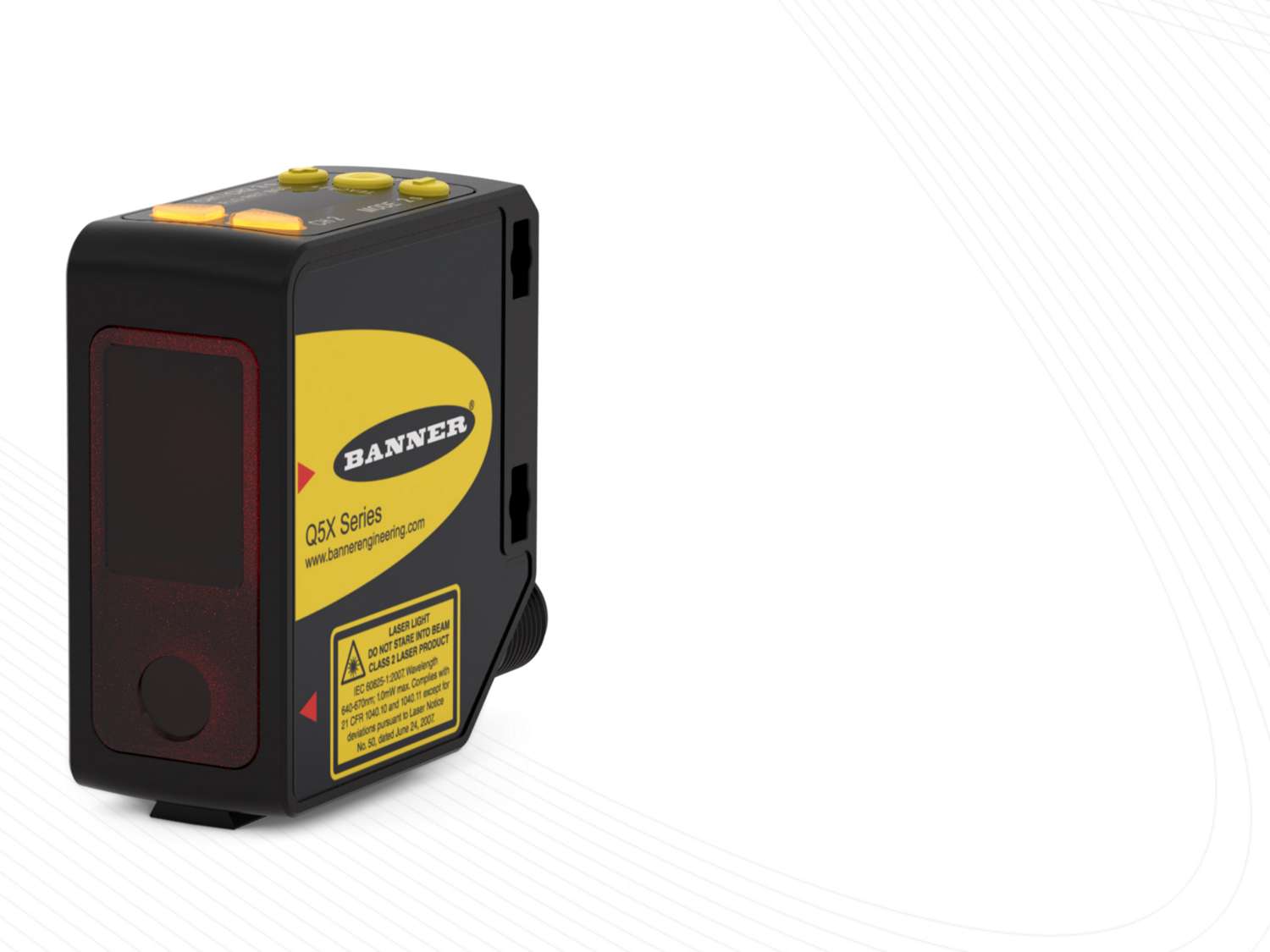
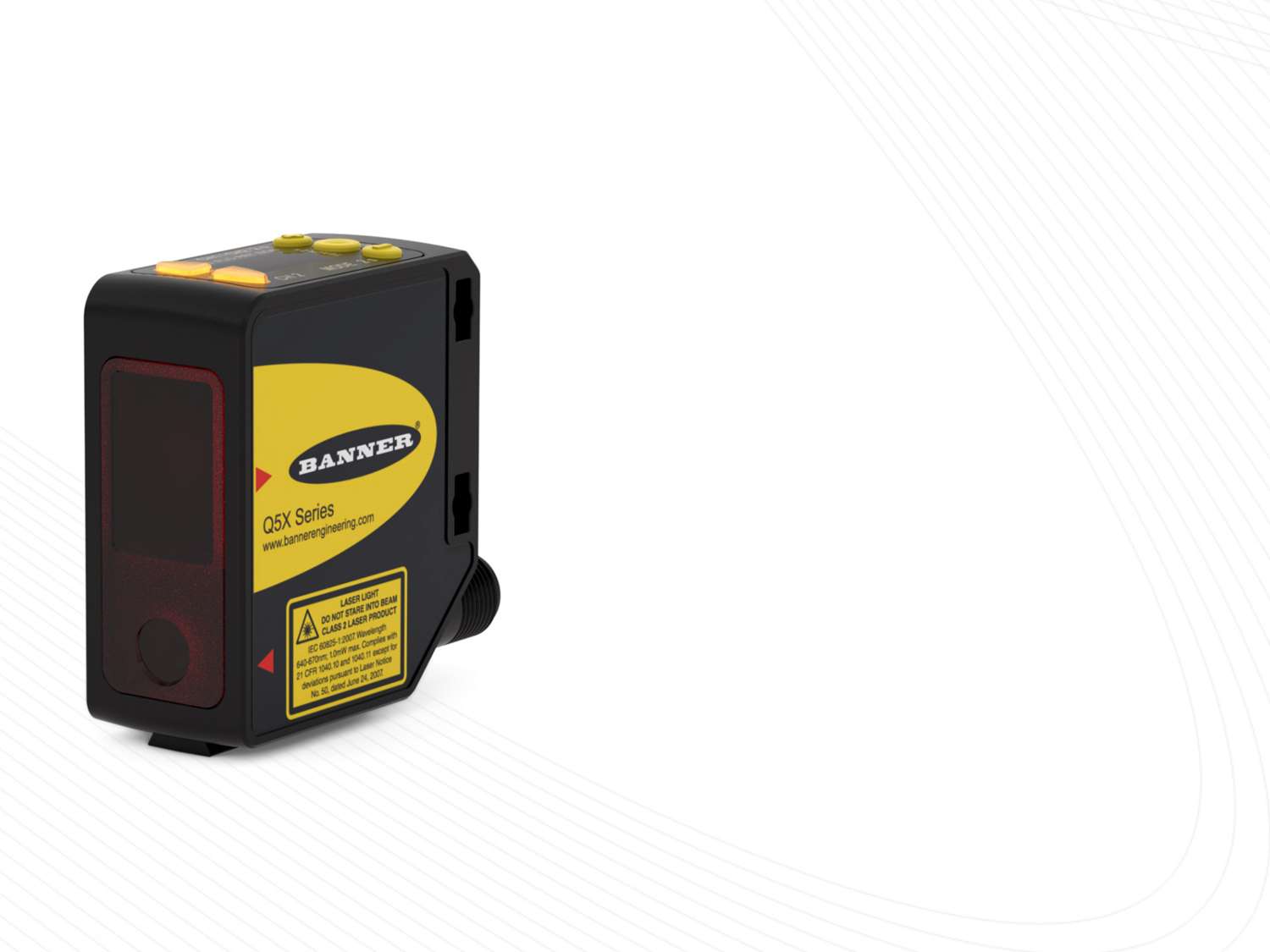
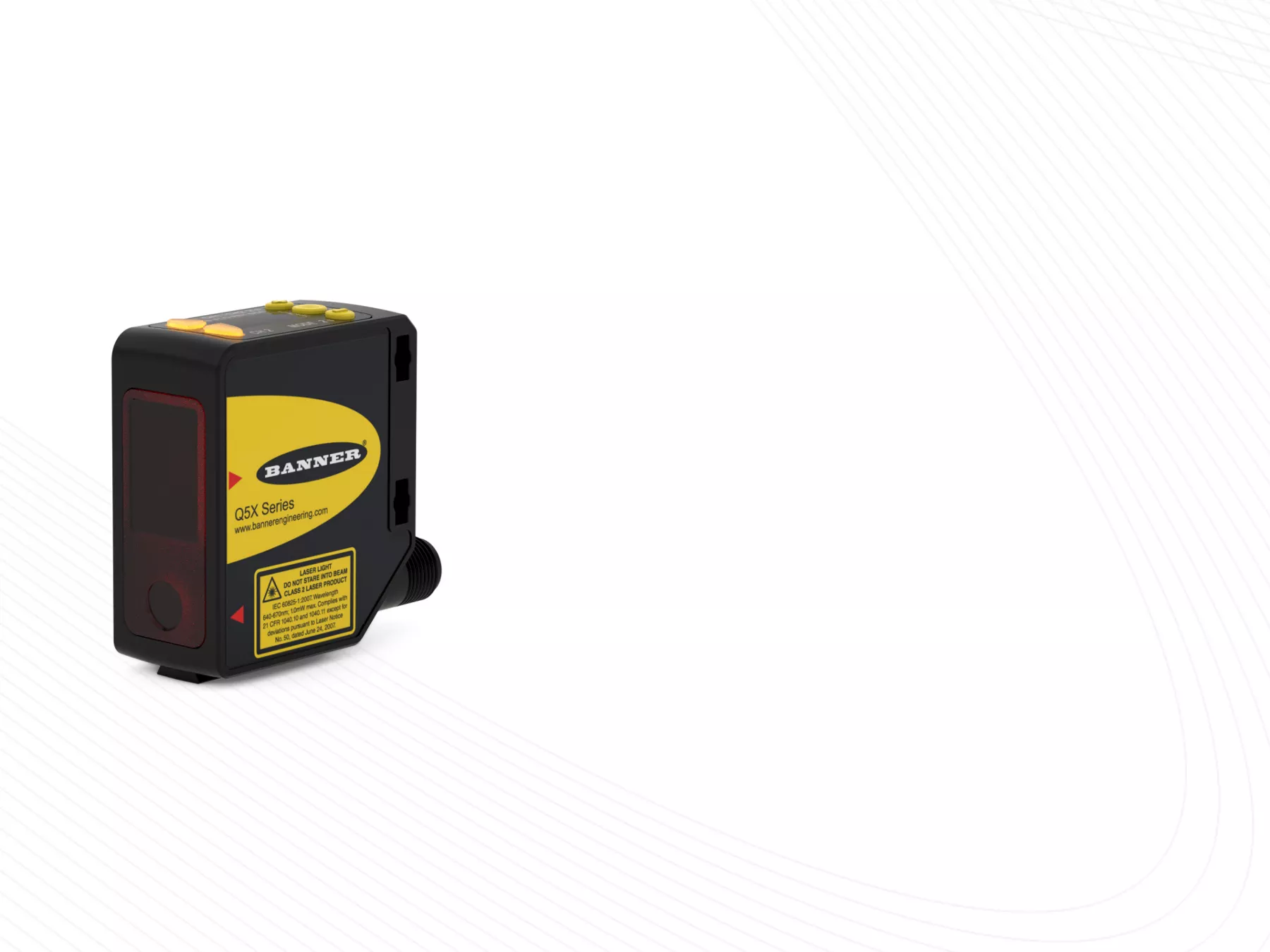
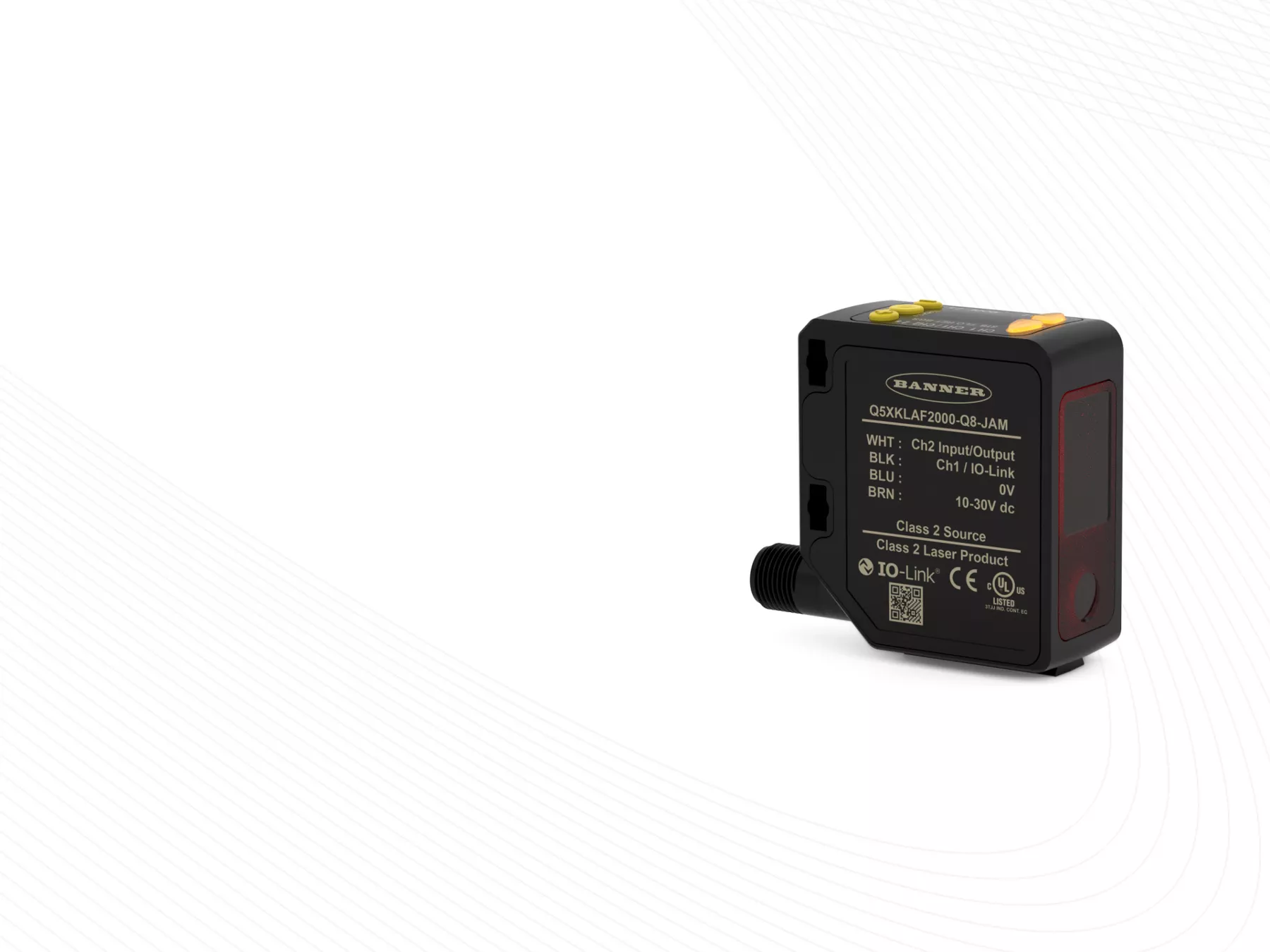
Naturally, factories that can address actual conveyor jams promptly and avoid false jam detections will be more productive—and more profitable—than competitors that struggle with more frequent work stoppages.
If your production facility is prone to frequent interruptions from your current jam-detection sensors, and especially if many of those jams turn out to be false, it might be time to upgrade to Q5X Jam Detection Sensors. These reliable sensors are easy to install, and they can be incorporated into any manufacturing environment using industry-standard M12 connectors and a variety of available mounting brackets.
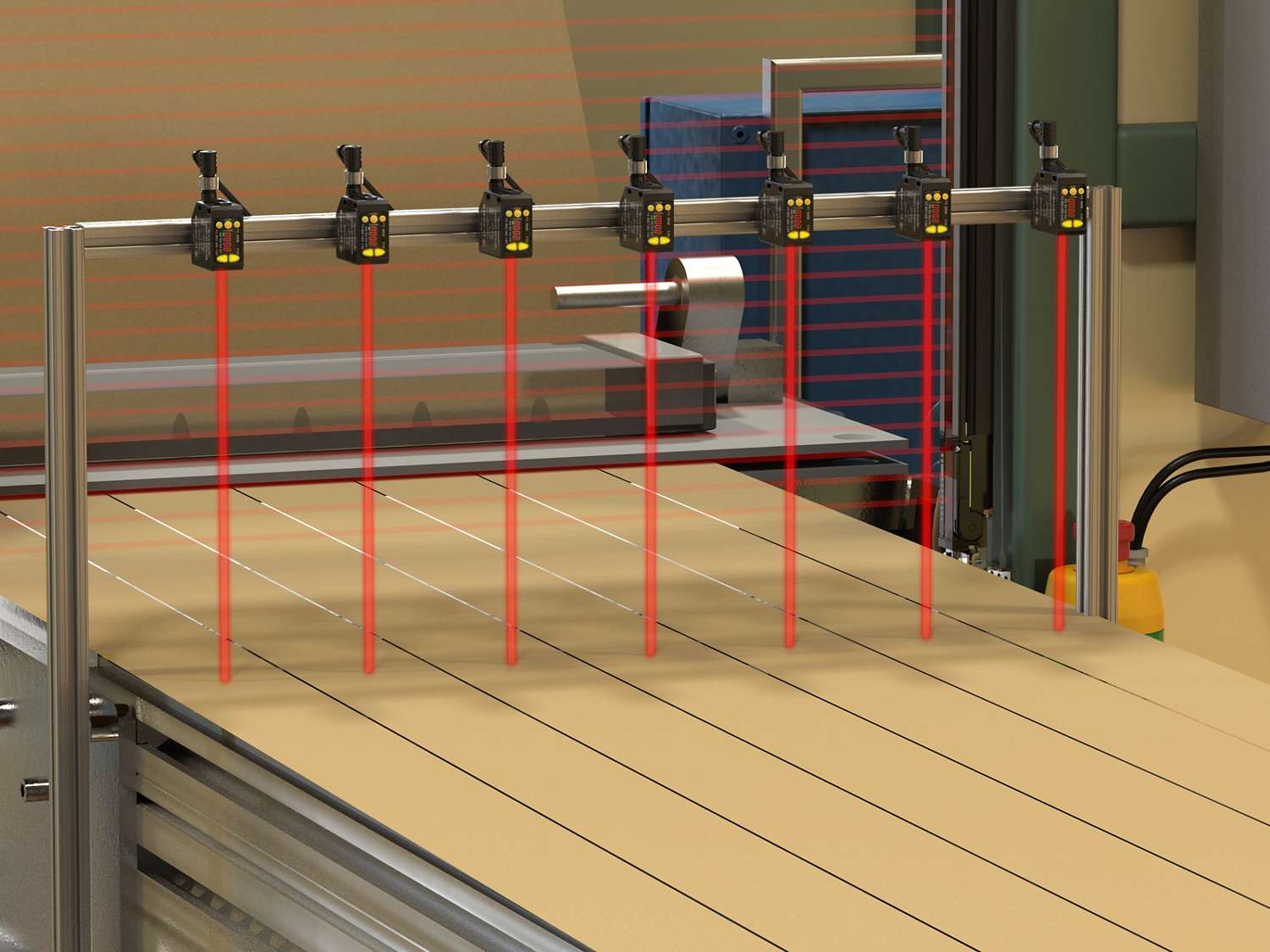
Determine How Much Jams (Real or False) Affect Your Productivity
Consider the following variables:
- How many jams are detected each day?
- What percentage of these jam detections turns out to be false alarms?
- On average, how much downtime do these false jams cause?
- What is the value of your throughput?
- How much does it cost for your technicians to address a false jam? How do false jams affect the productivity of your downstream processes?
Banner experts can provide further guidance to estimating jam-related productivity losses.
What is the typical method for detecting conveyor jams?
Most conveyor systems rely on simple photoelectric sensors (“jam photo eyes”) that look for packages moving by. Because the sensor is only capable of seeing if there is either something there or not, it relies on gaps between packages to detect package flow. An on-delay timer is needed to look for excessive periods of time when the sensor detects an object; this could mean that there is a jam and nothing is flowing. These timers reside in a controller, and it is typical to see on delay times of 20 seconds or more. This is problematic for two reasons, the packages could in-fact be flowing, just without gaps, and secondly, if a real jam does occur, then the response time is lengthened by the setting in the on delay timer.
What types of problems do real conveyor jams cause?
If conveyor jams are not cleared quickly, packages can pile up and cause damage to both the goods traveling on the conveyor, along with damage to the equipment itself. Furthermore, at some point the jam must be cleared, requiring staff to often resort to using “jam poles” to access the area, exposing a potential safety hazard in the process.
What types of problems do false conveyor jams cause?
If a false conveyor jam is detected, it will likely cause the conveyor to stop, which stops the flow of goods to the next destination. This stoppage not only reduces throughput of the facility, but also leaves many workers or other equipment without the input goods they need to do their job, creating waste in the work itself. False conveyor jams also cause unnecessary work by maintenance staff to go “clear” a false jam. Use our calculator to determine how much false jams are costing you.
Does the Q5X Jam Detection Sensor require any special programming?
The Q5X is set up entirely from the on-board display and pushbuttons. There are only minor configuration settings that you will need to make. Check out the video on this page for a tutorial on setting up the sensor.
Do I have to rewire anything to use Banner’s Q5X Jam Detection Sensor?
The Q5X uses an industry-standard M12 connector with common pinouts, this allows the sensor to easily replace a normal photoelectric sensor with no changes in wiring. If wiring changes are needed, including switching from AC to DC power, Banner can supply adapter cables in many cases; just consult with your local Banner expert or reach out to our Application Engineering team in the chat window in the lower right of this screen.
Does the Q5X Jam Detection Sensor require a reflector target on the opposite side of the conveyor?
No, the QX Jam Detection Sensor can be taught in two teach modes. One does need a static reference target but it does not need to be a standard reflector. Any target can be used as long as it will always be present such as the back rail of the conveyor. The other teach mode uses a temporary target for the teach process which can be removed once the sensor is in run mode.