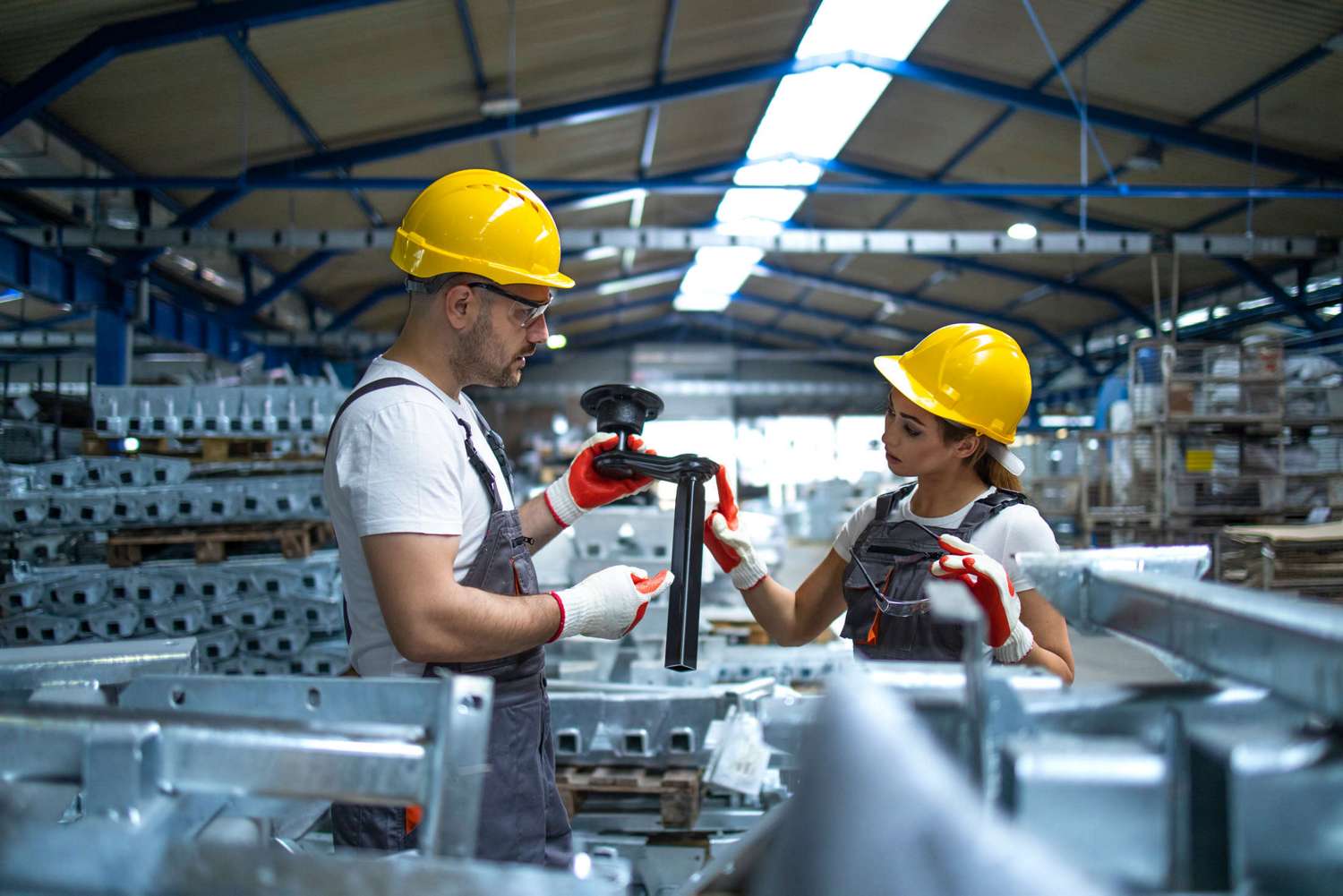
3 Ways IIoT Will Impact Your Operations
Table of Contents
Collecting data and connecting machines to make them “smart” is an important step in the evolution of Industry 4.0. However, getting value requires more than just collecting a lot of data. Real innovation and value will come by using tools that engage with that data, allowing facilities to operate more effectively and profitably. These tools include sensor overlay networks, predictive maintenance systems, and production tracking tools. Here are three key ways that IIoT tools will impact manufacturing operations by harnessing data.
- Making Equipment Data Visible To All Who Need It
- Pinpointing Reliability Issues and Eliminating Downtime with Predictive Maintenance
- Tracking Throughput Metrics to Optimize Productivity and Increase Profitability
Making Equipment Data Visible To All Who Need It
Harnessing data is important, but simply seeing a lot of data in one database table isn’t helpful and can be overwhelming and counterproductive. A cloud platform should give users ways to visualize and analyze according to their specific use cases and job requirements. One size doesn’t fit all: A maintenance supervisor may want to see condition monitoring data from a variety of sensor types and group their data by asset type. In contrast, an assistant plant manager may want a more holistic view that includes production tracking and can correlate that with sales and scheduling data.
In the quest for innovative ways to improve efficiency and empower teams with data to help do their work, companies face a common roadblock: Production data is often confined to an individual machine. Although many companies are adopting connected or “Smart” manufacturing processes, these systems may not communicate with each other or with existing hardware and software, let alone a common cloud platform. The data an organization needs to improve operations is still often largely segmented and inaccessible.
IIoT overlay networks, like Snap Signal from Banner Engineering, solve this problem by capturing data signals from virtually any source and converting them to a common industry standard protocol. These overlay networks then aggregate the data and distribute it to users for a unified view of operations. This gives an organization the ability to see its manufacturing data in one place without removing and replacing their existing machines and controls infrastructure. The overlay network is a simple, affordable way to deliver customized data into the hands of those who need it.
To dive deeper on this topic, check out our 5-step guide to modernizing your factory.
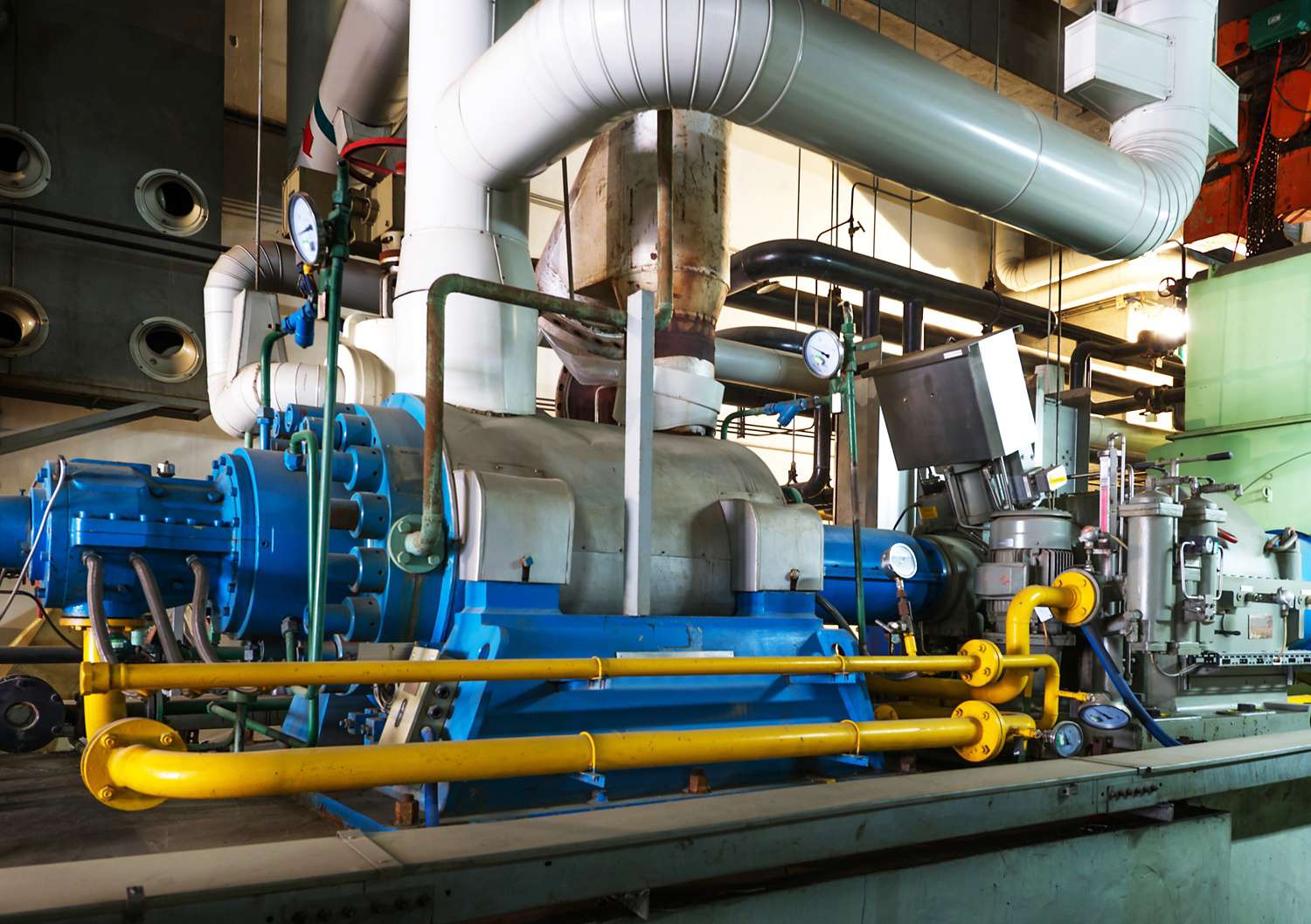
Looking for a Printed Copy of This Page?
Download the 3 Ways IIoT Will Impact Your Operations PDF to learn about the three key ways that IIoT tools will impact manufacturing operations by harnessing data.
Pinpointing Reliability Issues and Eliminating Downtime with Predictive Maintenance
Visualization of sensor data gives you the ability to target maintenance procedures based on data rather than assumptions. In many legacy production systems, maintenance was “reactive” and occurred only when a problem had already caused downtime and scrap. A machine was installed, run until it stopped working, and then repaired. This cycle was repeated until the machine was eventually scrapped and replaced.
Today most maintenance is “preventive,” but requires technicians to have a preset maintenance schedule or “route,” whether machines need maintenance or not. This heavily manual process is successful in preventing many failures, but there are still downsides. Maintenance technicians spend unnecessary time and often incur travel expenses, performing unneeded maintenance too early. In some cases, this type of maintenance scheduling can even create problems, such as if the technician accidentally assembles something incorrectly, introducing a fault that wasn’t there before.
“Predictive” maintenance is the next evolution in reliability. With this method, IIoT data lets reliability groups make data-driven decisions about what assets to service and when to schedule maintenance.
IIoT systems from Banner Engineering (such as the Vibe-IQ vibration analysis software and hardware) have algorithms running at “the edge” of the factory’s network (i.e. near the source of the data). These algorithms automate the process of identifying machine performance trends.
An asset’s gradual condition decline is identified long before it becomes a problem, and maintenance can be scheduled to bring equipment up to spec. In addition to identifying performance trends, condition monitoring systems can also send alerts to maintenance team phones and desktops if a problem is growing worse over time, or if an instantaneous fault occurs.
Predictive maintenance offers one of the quickest returns on investment for IIoT applications. It allows facilities to prioritize technician time on the things that will make the most impact on the business. It’s extremely simple to add a condition monitoring system to an existing process. And among the various applications for IIoT, predictive maintenance is among the fastest to give facilities a return on their investment by eliminating costly downtime. The elimination of even one occurrence of downtime typically more than covers the cost of sensors and monitoring equipment.
Tracking Throughput Metrics to Optimize Productivity and Increase Profitability
Production managers must schedule people and raw materials, meet production targets, and ensure they’re not holding too much inventory.
IIoT technologies give visibility to the plant floor, letting managers make decisions about productivity and scheduling that are based – not on assumptions -- but nearly real-time data.
Data historians of the past helped organizations track production over time, spotting trends and patterns in production history. By making production data available in an IIoT platform, facilities speed the feedback loop to front-line operators who can make decisions with better context. Instead of looking backward to past weeks or months, IIoT lets you see what you produced in the last hour, every hour.
Production tracking tools, such as Banner’s PPM Kit (Production Performance Monitoring Kit) track production to identify sources of reduced output in production lines. Sensors at each stage of the production process count parts that move by and alert users to extended slow or stopped conditions. By measuring individual line speeds and part counts and comparing them with ideal user-set conditions, these tools give operators insight into their performance and data they can use to identify and remove bottlenecks in production.
IIoT systems let users see data from multiple facilities, so they can identify patterns and make correlations that they couldn’t make, if looking only at a single point. By using the combination of features a robust IIoT platform provides, facilities can improve production with better visibility and accountability across all areas of the business.
IIoT platforms also make data available to analyze and correlate with other business systems like sales data, financial information, and other manufacturing processes. This lets companies begin the journey towards “big data” and makes advanced analytics possible. A good IIoT platform will offer tools for getting immediate value from the data on the first day, while also making that data accessible to other analytics tools to build more complex datasets as your digital transformation evolves and matures.
There are innumerable ways IIoT can impact manufacturing organizations, but the many outcomes roll up to a few key benefits like efficiency, information availability, and profitability. To take advantage of IIoT’s promise, collecting data and connecting machines to make them “smart” is only the first step. Using specific IIoT applications will unlock real value and drive innovation. Key IIoT tools include overlay networks (that get all machines speaking the same language), predictive maintenance systems, (that pinpoint reliability issues early to avoid downtime, and OEE tools (to optimize productivity and increase profitability).