Sheet Metal Thickness Measurement
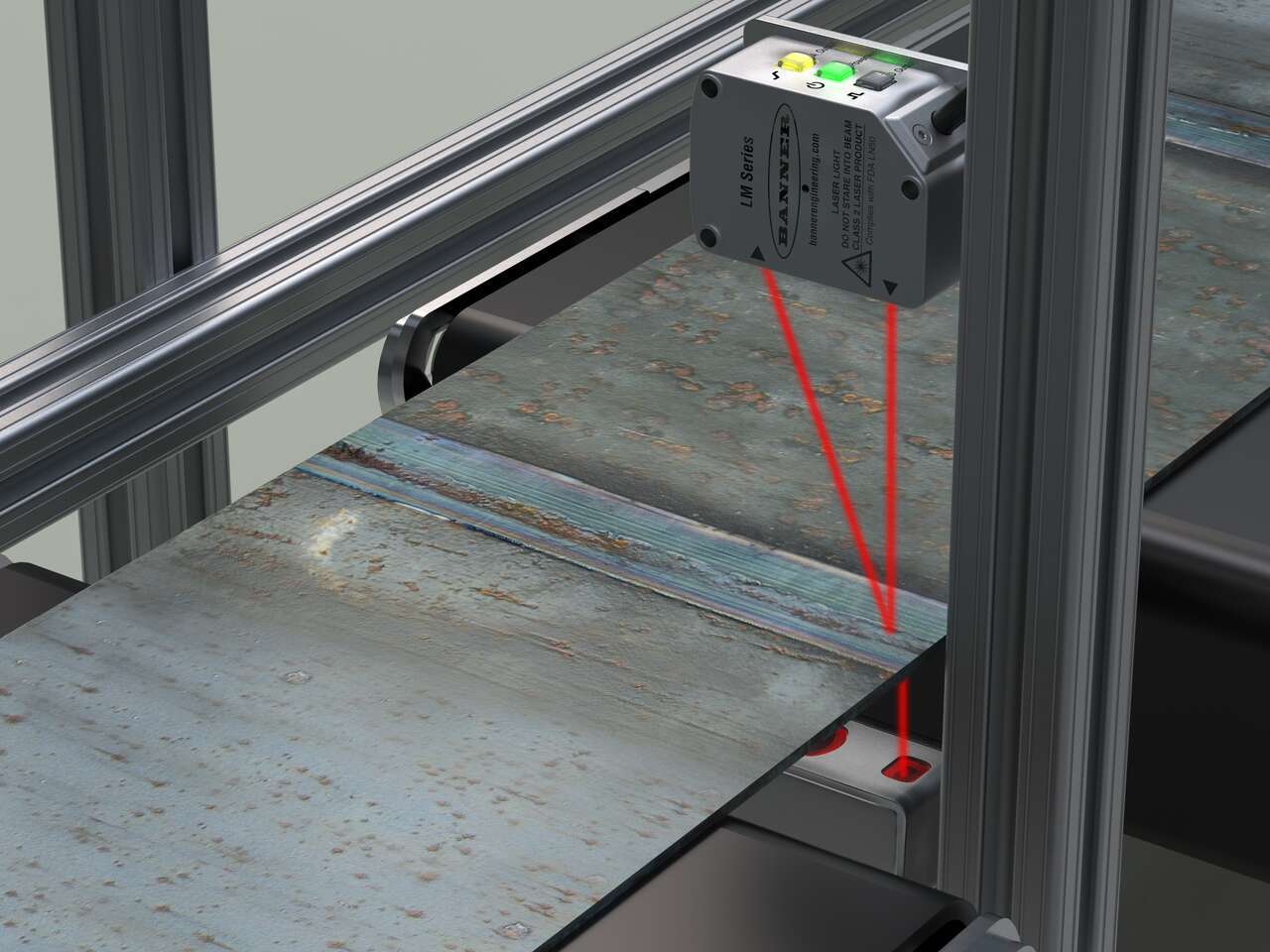
Application: Measuring thickness on a metal sheet
Challenges: Precise and consistent sensing while material moves down a conveyor
Solution: LM Series Laser Measurement Sensor
Benefits: Measures thickness at micron levels
In the automotive industry, sheet metal stamping is the process of cutting and shaping metal alloys into automotive frame brackets and other forms using a press tool. Metal stamping dies are used to create high precision metal parts that are equal in shape and size.
Automotive metal stamping requires a specific thickness to ensure the parts are equal, and to ensure the die is not damaged during this process. As metal sheets move down the conveyor, laser displacement sensors measure the sheets on a very precise scale to ensure they are the correct thickness. In this sheet metal stamping application, it is important that the frame brackets and other metal components are identical and that the die is not damaged to prevent down time and costly repairs.
Description
The LH laser displacement sensor is a perfect solution because it is highly accurate and measures thickness at micron levels. The L-GAGE LH Series can also consistently look at dark targets on these levels. The LH’s 1024 pixel CMOS linear imager is capable of micrometer-level resolutions ranging from 1-10 microns, which gives it the ability to measure thickness of sheet metal quickly and accurately. Thickness measurements are available with 4-20 mA analog or RS-485 digital communication outputs.
The LH sensor pair self-synchronize to take measurements and calculate thickness within the sensors, without a controller. For this specific thickness measurement application, the "master/slave separation," which is two times the reference plus nominal distance, is the ideal separation between the two sensors.