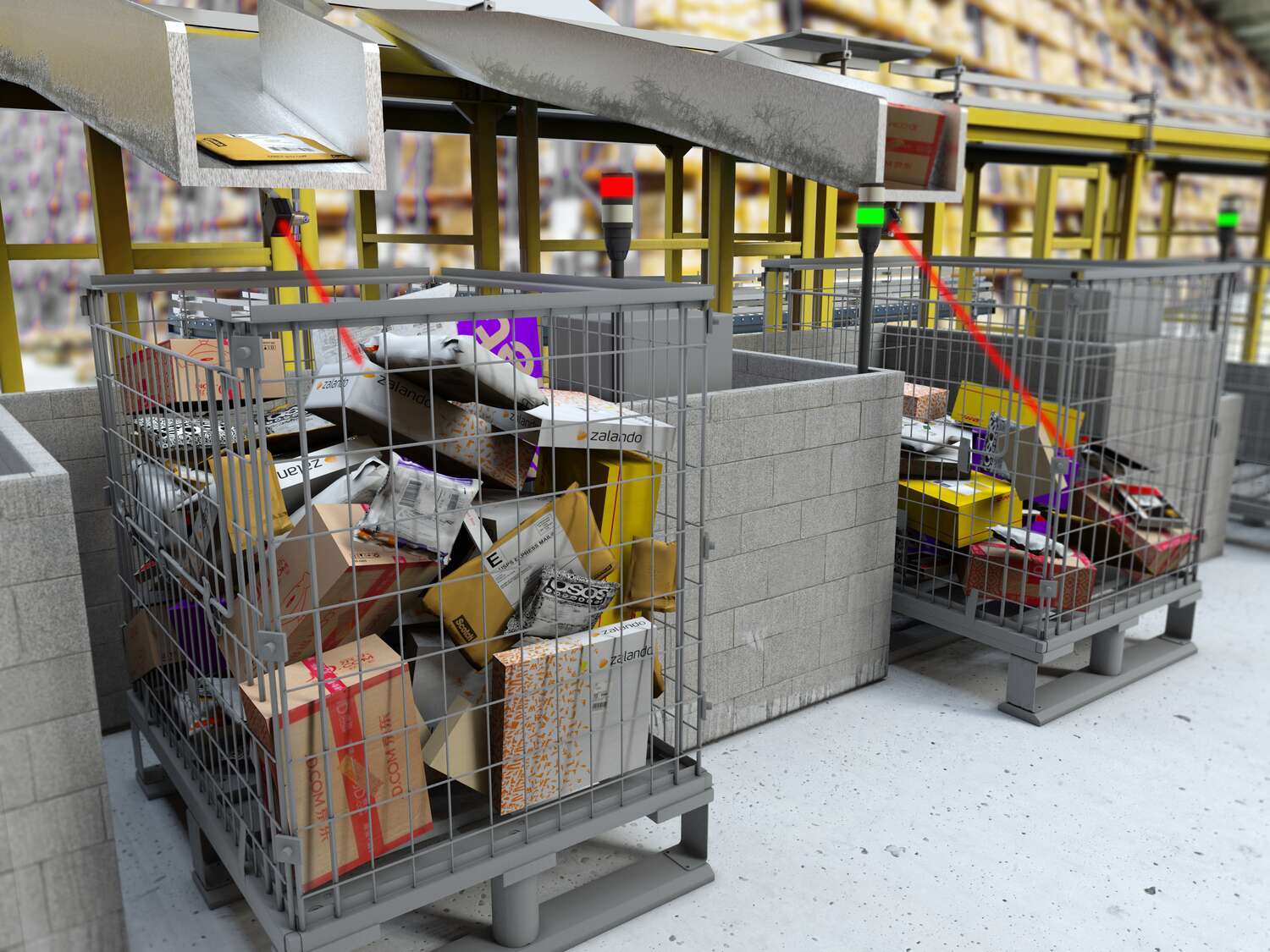
What Is 3D Time of Flight?
Most measurement sensors are designed to look for an object at a particular point within a narrow area. However, there are some applications that require looking for objects across a larger area, such as detecting when a shipping cart is full of various-shaped packages and needs replacing or measuring the heights of items across an entire pallet to ensure even loading or unloading. In situations like these, a more effective solution than a single-point sensor is to measure the entire space with a 3D time of flight (ToF) sensor.
Alex Novak, Global Product Manager for Sensors at Banner Engineering, explains that “3D time of flight is a type of optical measurement. It makes a grid of distance points to create a 3D point cloud of information, which is then used to understand different things about the target. This data can be used to perform calculations, such as the volume of multiple items in a bin. Specific aspects of the viewing area can be reported, like the greatest peak height a sensor can see.”
How 3D Time of Flight Works
The initial operation of a 3D ToF sensor is fairly straightforward: light is emitted from the sensor, bounces off the target, and returns to a multipixel imager.
The next part is a little more complex. As the light returns to the sensor, each individual pixel will report a different distance measurement point because it is receiving its own piece of the emitted light. The distance information for each pixel is determined by measuring the round-trip time from light emission to reception on each pixel. When the distance information for each pixel is combined, the sensor can create a fully three-dimensional picture of what it sees.
How 3D Time of Flight Differs from Other Sensor Technologies
Most other optical sensor technologies measure a lone signal returning from a single, small-diameter point. By only measuring a very small area, these sensors have a difficult time recognizing peaks and valleys among material heights being measured. Novak says a 3D ToF sensor, on the other hand, “combines a light emitting source with a special type of imager and makes many distance measurements at once, allowing for the construction and interpretation of a 3D image with a single light emission event.” In other words, a 3D ToF device gathers data from numerous points simultaneously across a broad area, whereas other sensors capture measurement data from specific small points.
Why 3D Time of Flight Is a Better Choice for Some Applications
When using 3D ToF, a user is given much more information than single point sensors. “This extra data allows a user to make more informed decisions about their application,” says Novak. “It can provide insight that would otherwise be very difficult to gather, such as tracking the volume taken up in an empty space as opposed to just a single height measurement point.”
For example, a 3D ToF sensor can easily and accurately detect the variances across the aforementioned shipping carts and pallets. In the carts, varying peaks, valleys, and gaps are formed by shipping packages of various shapes, sizes, and orientations. A 3D ToF sensor detects the unpredictable and ever-changing contours of the collected packages as they pile up, regardless of sizes, angles, or positions. Similarly, the top of a pallet load can easily be monitored for items reaching a certain stacking height no matter where the items are placed. Operators can be notified when fill levels and peak heights are reached anywhere across an entire area, something a single point sensor might not be able to catch.
When precise height measurements across a broad area are needed, 3D time of flight technology can solve many challenging applications in which other technologies would give an incomplete picture.