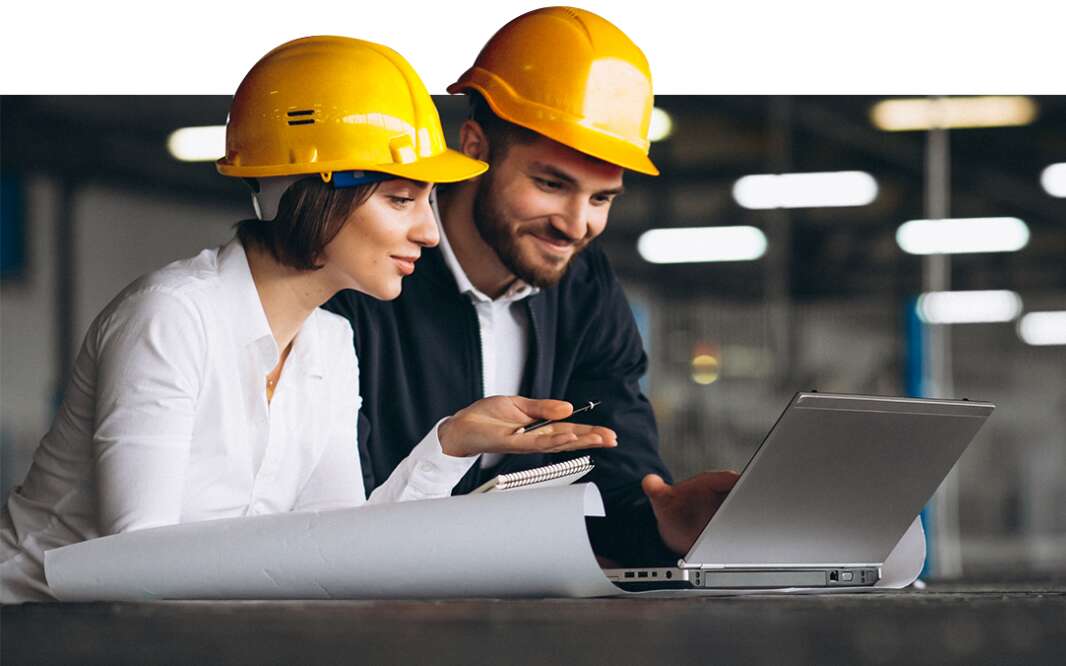
Automotive
Automation Maximizes Production Quality and Throughput
Harsh manufacturing environments, challenging targets, and operator safety require rugged and reliable solutions that reduce downtime due to inadvertent stoppages. As more sophisticated components find their way into vehicles, Banner helps automotive manufacturers effectively modernize and optimize their production.
With robust sensors, operator guidance, and lights that give machines a voice, Banner is helping companies solve challenges related to quality inspection, assembly, finishing, and inventory tracking across the global supply chain.
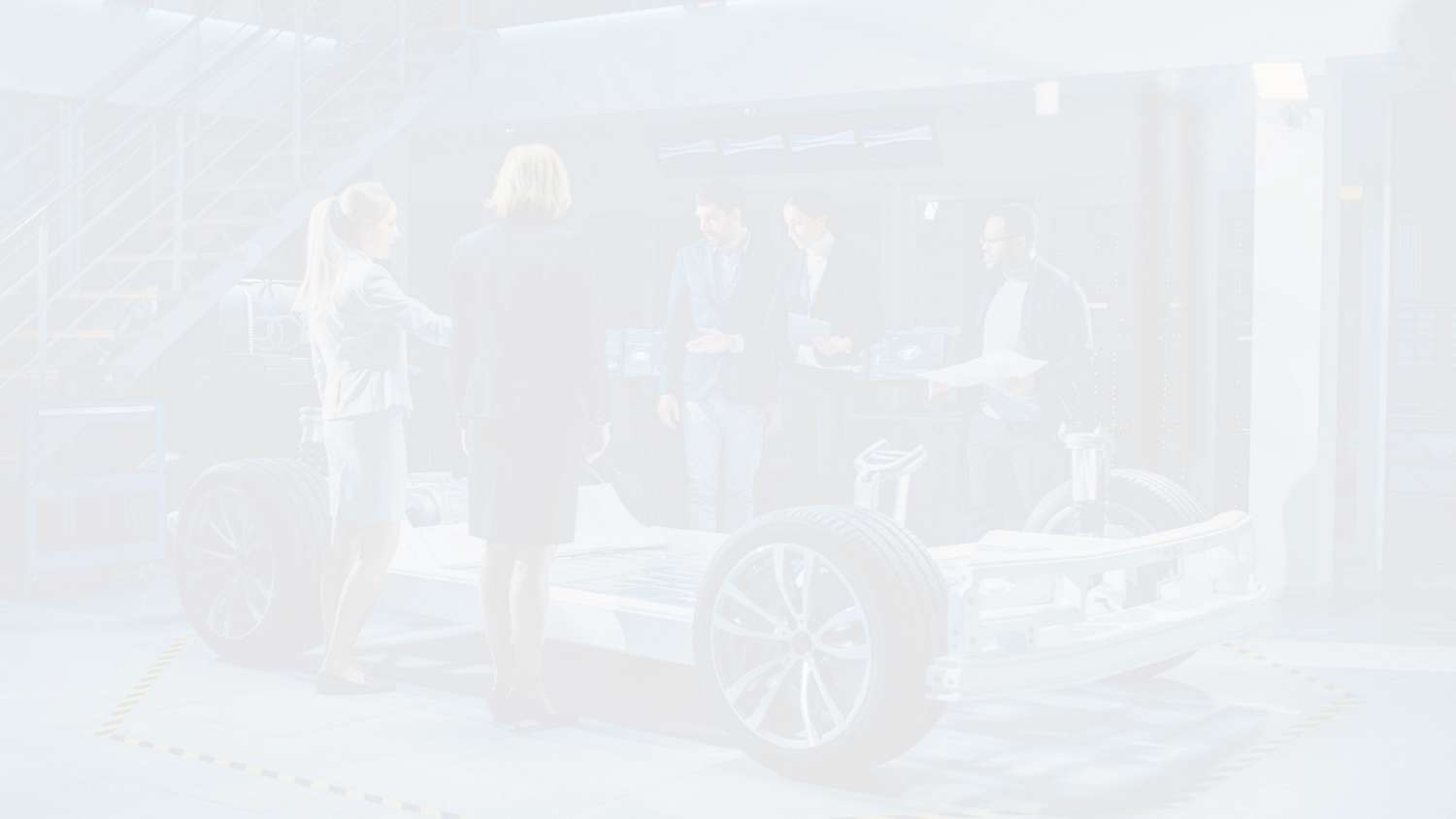
Start with Banner
Every day, automotive and tier manufacturers around the world rely on Banner to solve simple to complex automation challenges in the automotive marketplace. Automotive companies both large and small are adapting to new markets and new technologies, and Banner is helping them be increasingly flexible and deliver more products at greater efficiency.
Banner’s comprehensive catalog of more than 10,000 products includes sensors, smart IIoT and industrial wireless technologies, LED lights and indicators, pick-to-light systems, measurement devices, machine safety equipment, as well as barcode sensors and machine vision products that drive efficiencies, improve productivity and system accuracy, and reduce errors and cost.
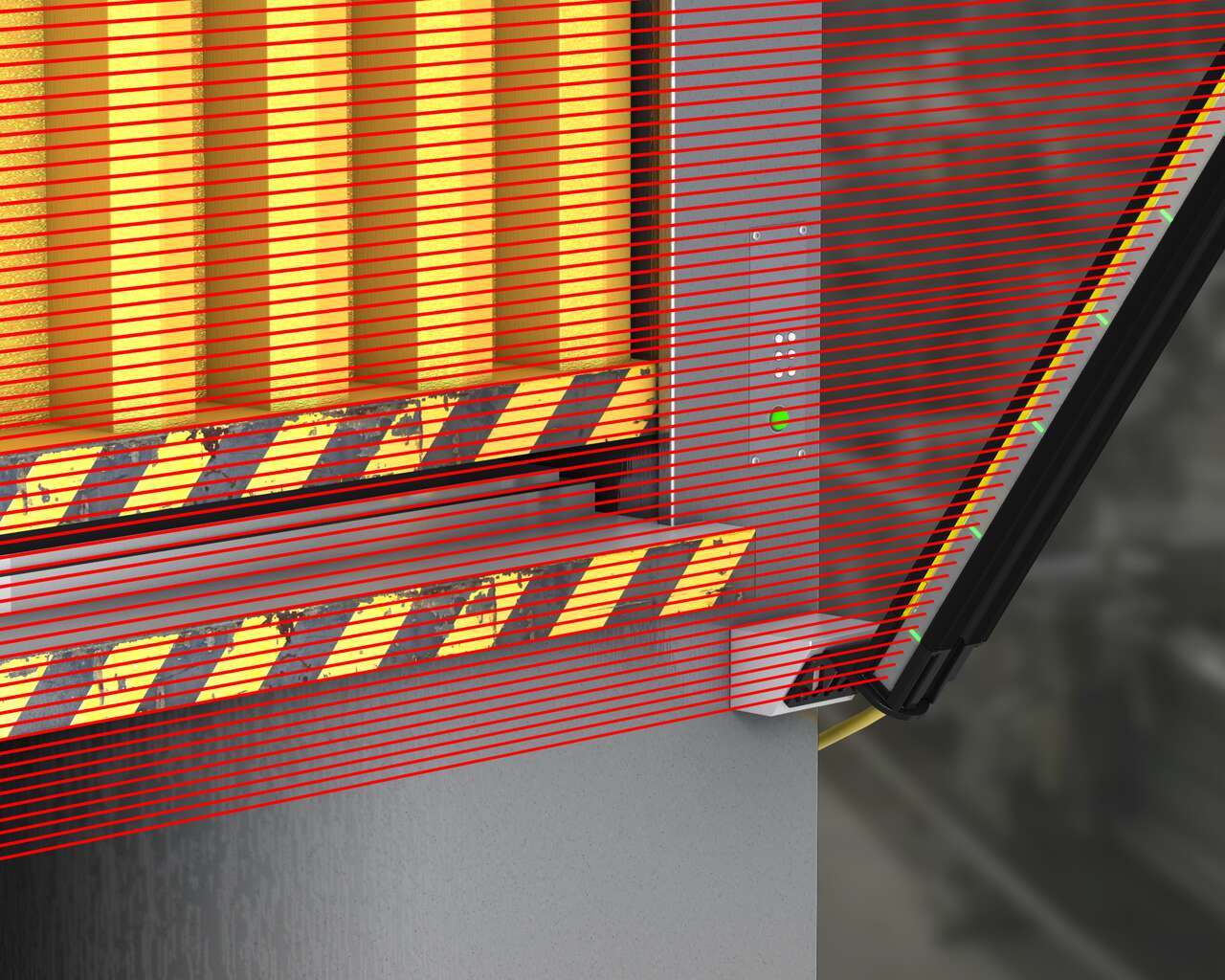
Banner Engineering’s EZ-SCREEN LS is extremely robust with heavy duty extruded aluminum IP65/67 rated housing, metal endcaps and a recessed window to protect it from collisions related to stock removal and incidental impact.
Learn More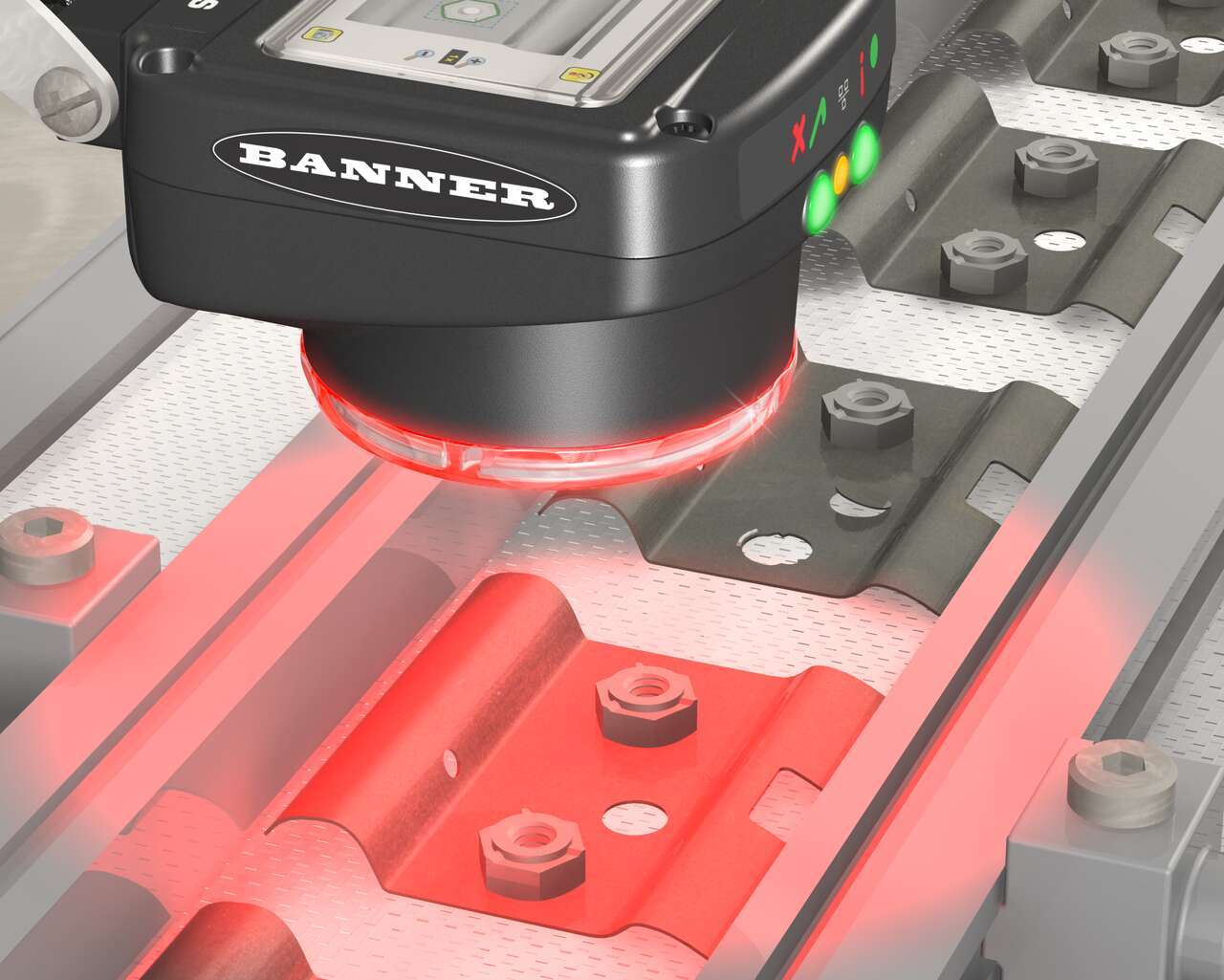
To verify the expected number of holes exists on a small metal part, the iVu Plus TG Image Sensor with Multipoint Inspections can be configured for multiple regions of interest (ROIs) to ensure holes exist and were punched in the correct place. When set up for area inspection, the iVu will scan multiple points on the stamped part to verify the presence or absence of a feature or features of interest.
Learn More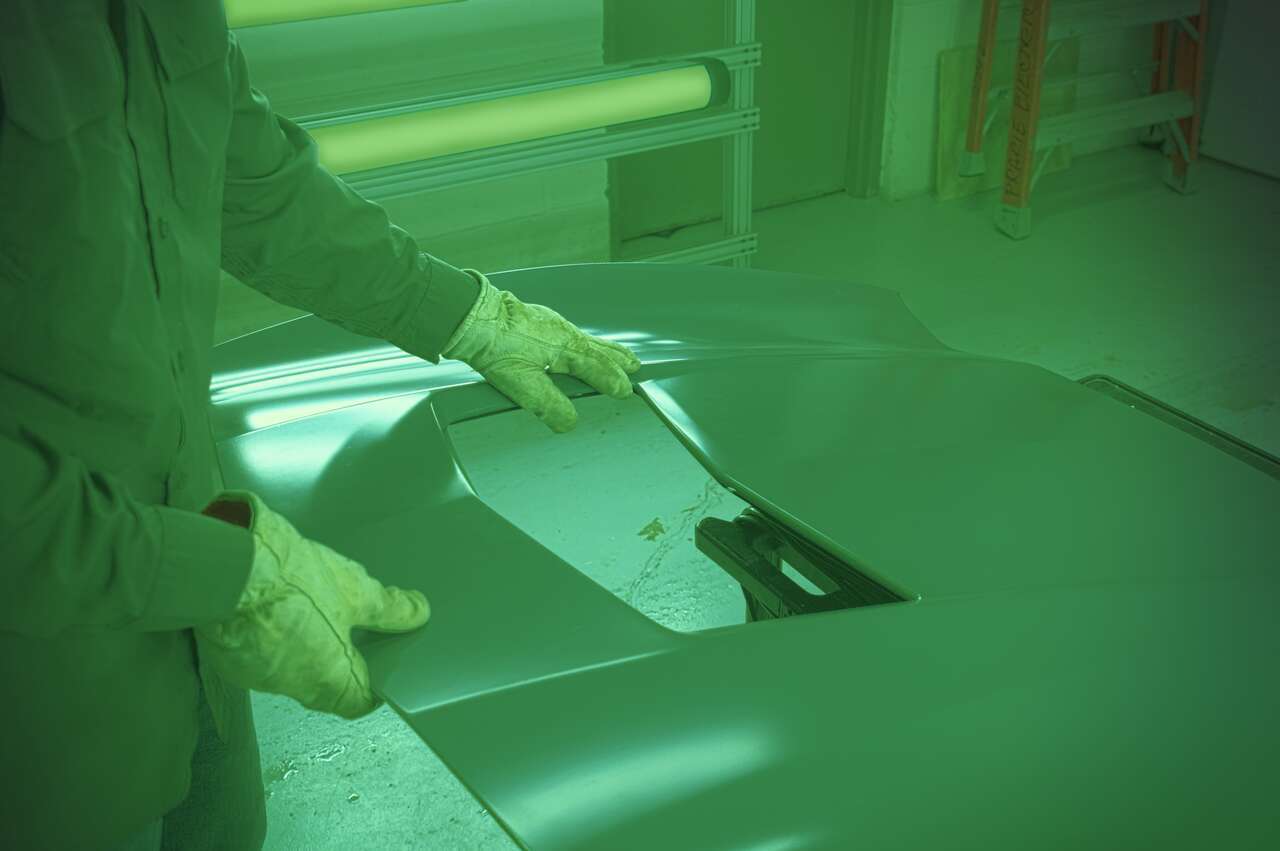
Learn how green LED task lights enhance visibility of surface imperfections on manufacturing materials.
Learn More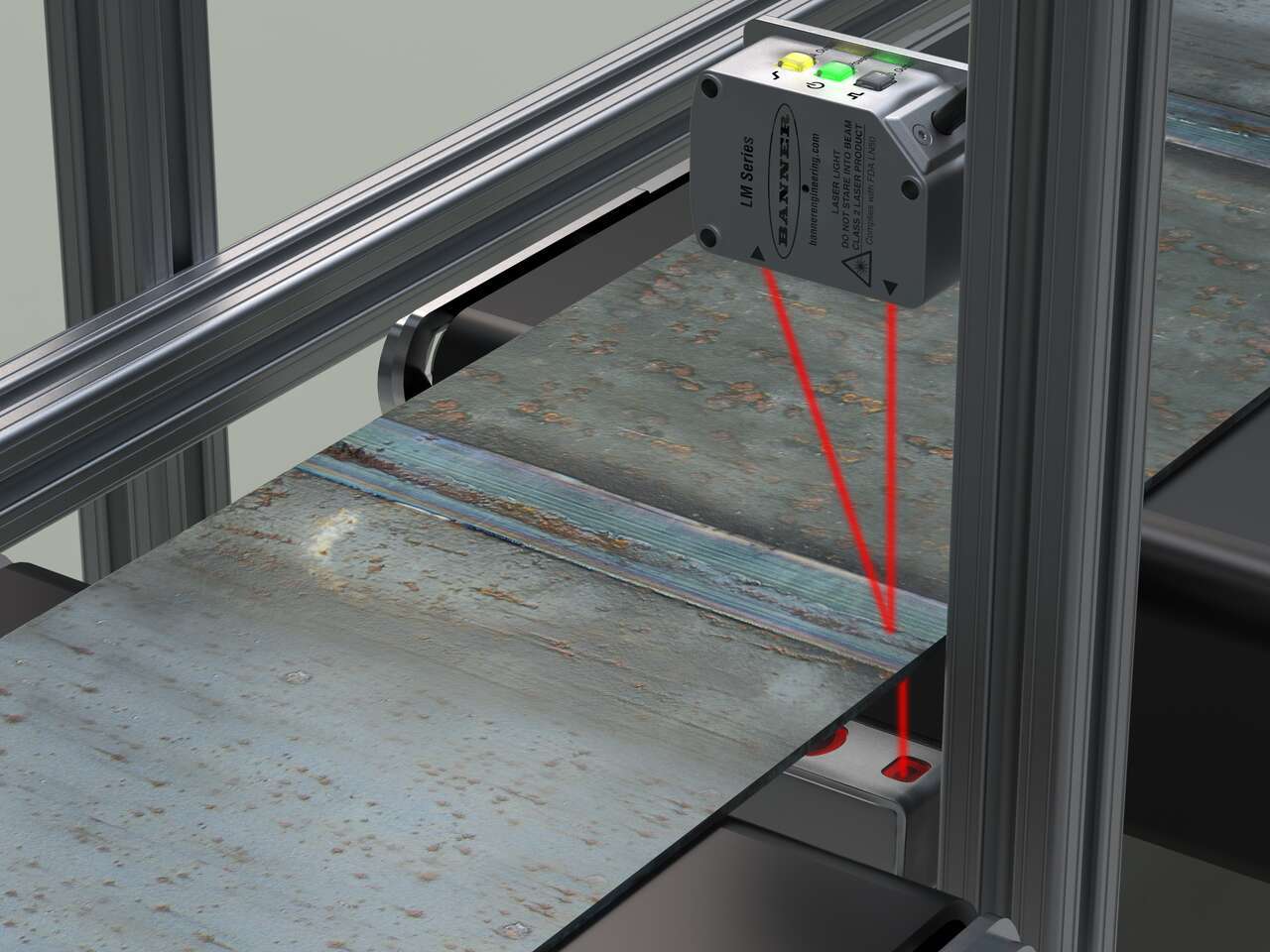
Precise and consistent sensing while material moves down a conveyor measuring thickness at micron levels.
Learn More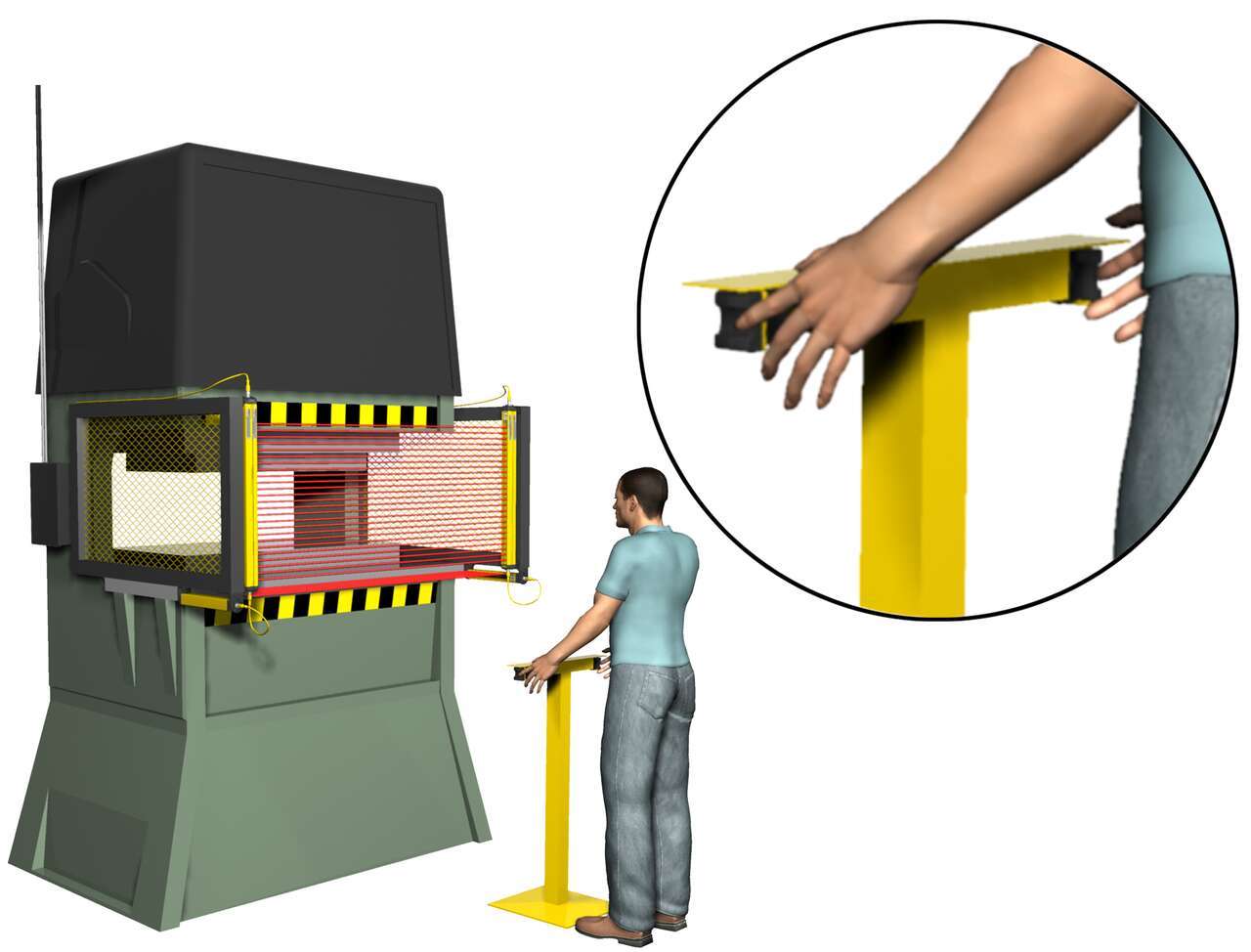
A two-hand control safeguarding system will prevent the operator from approaching the machine while a hazard is present. The machine cycle will begin only when the operator touches both Self-Checking Touch Buttons (STBs) within half a second of each other and will continue operation only as long as both hand controls are actuated, thereby assuring that the operator will remain at the control station while the machine is in use.
Learn More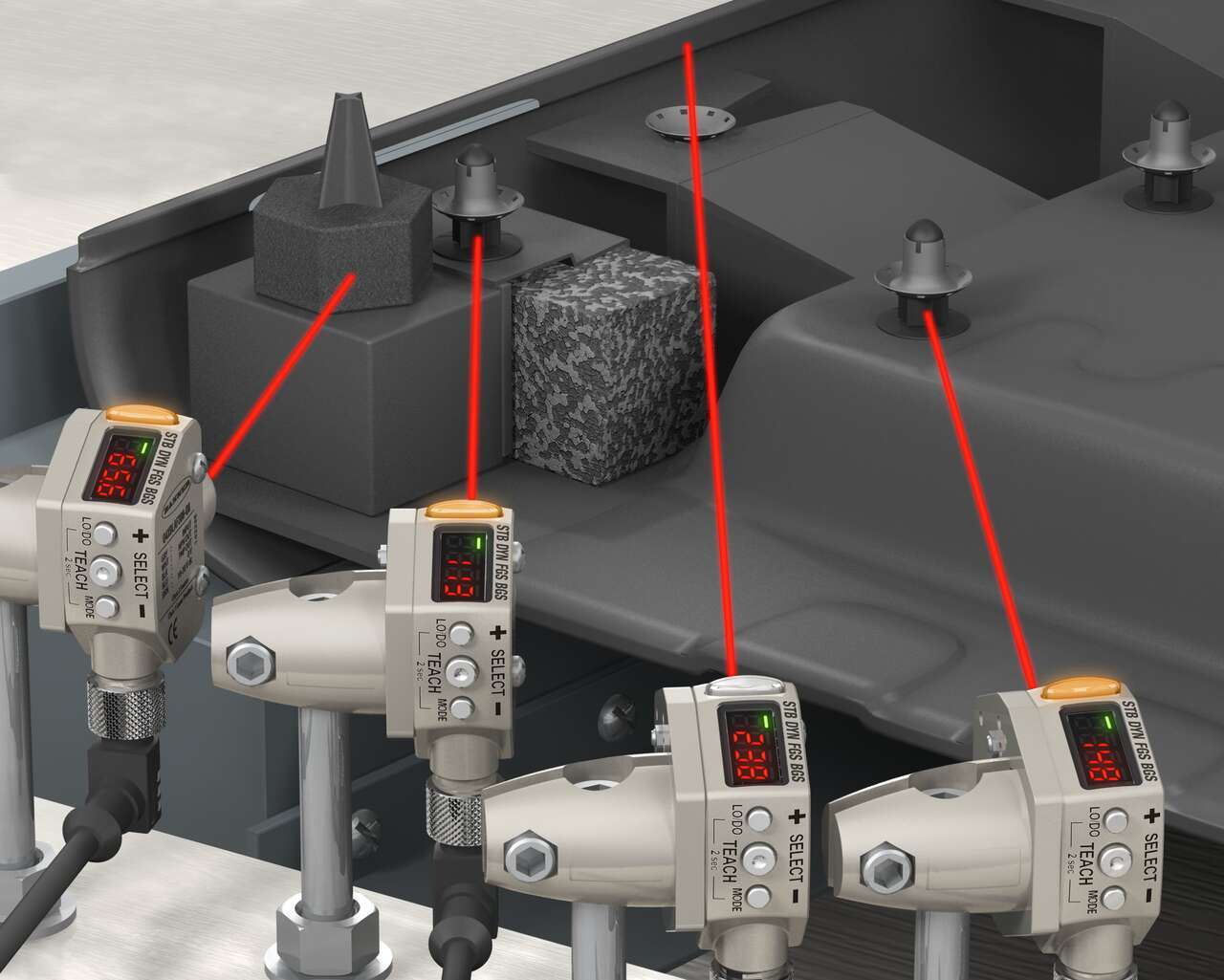
Since door panels are often dark colors such as black or gray, and the foam used to eliminate rattles and provide stiffness is generally black, it can be difficult for standard sensors to differentiate between foam presence and absence due to poor contrast.
Learn More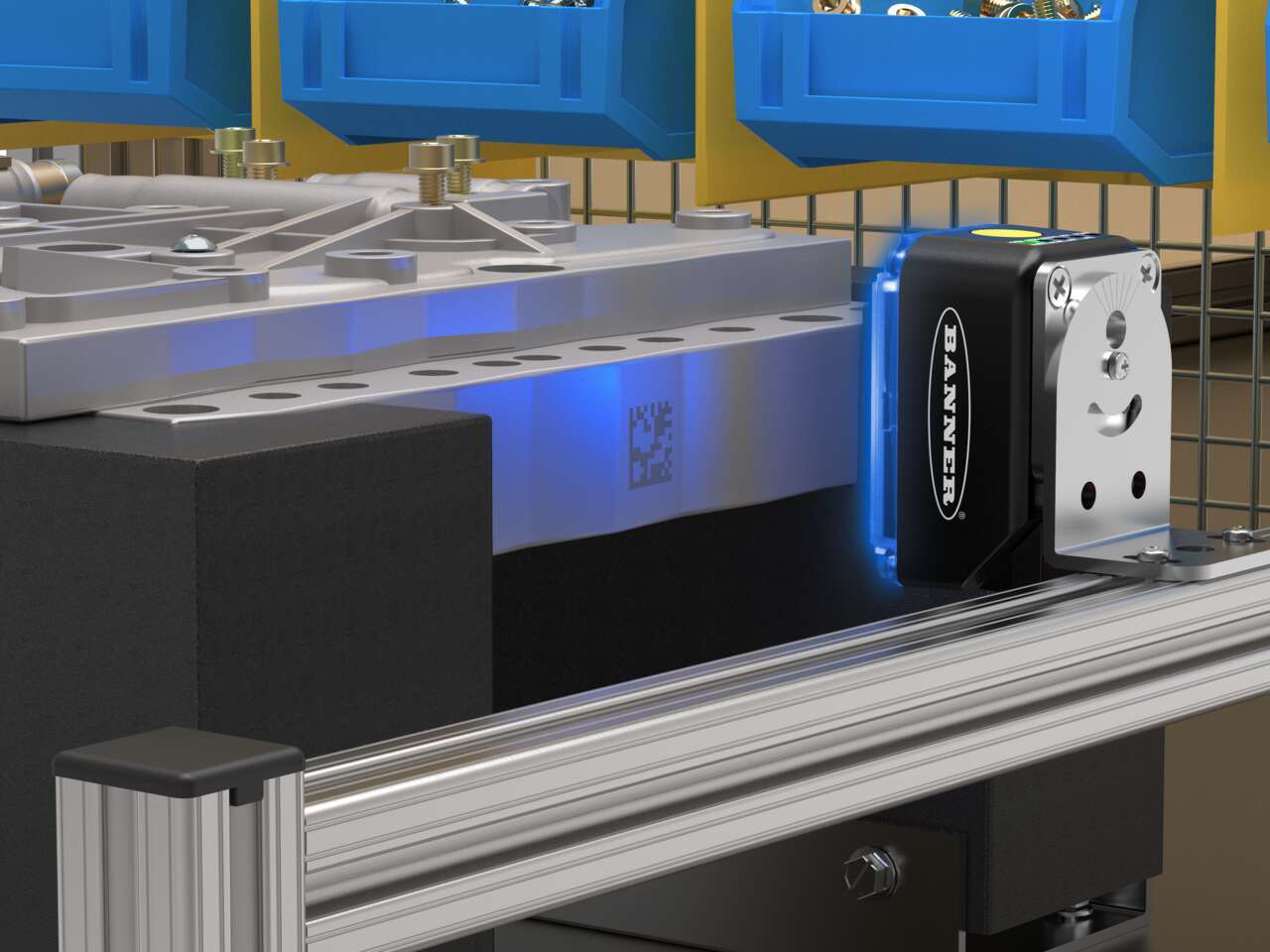
Direct part mark (DPM) codes can be small, complex, and difficult to distinguish from the material they are etched into.
Learn More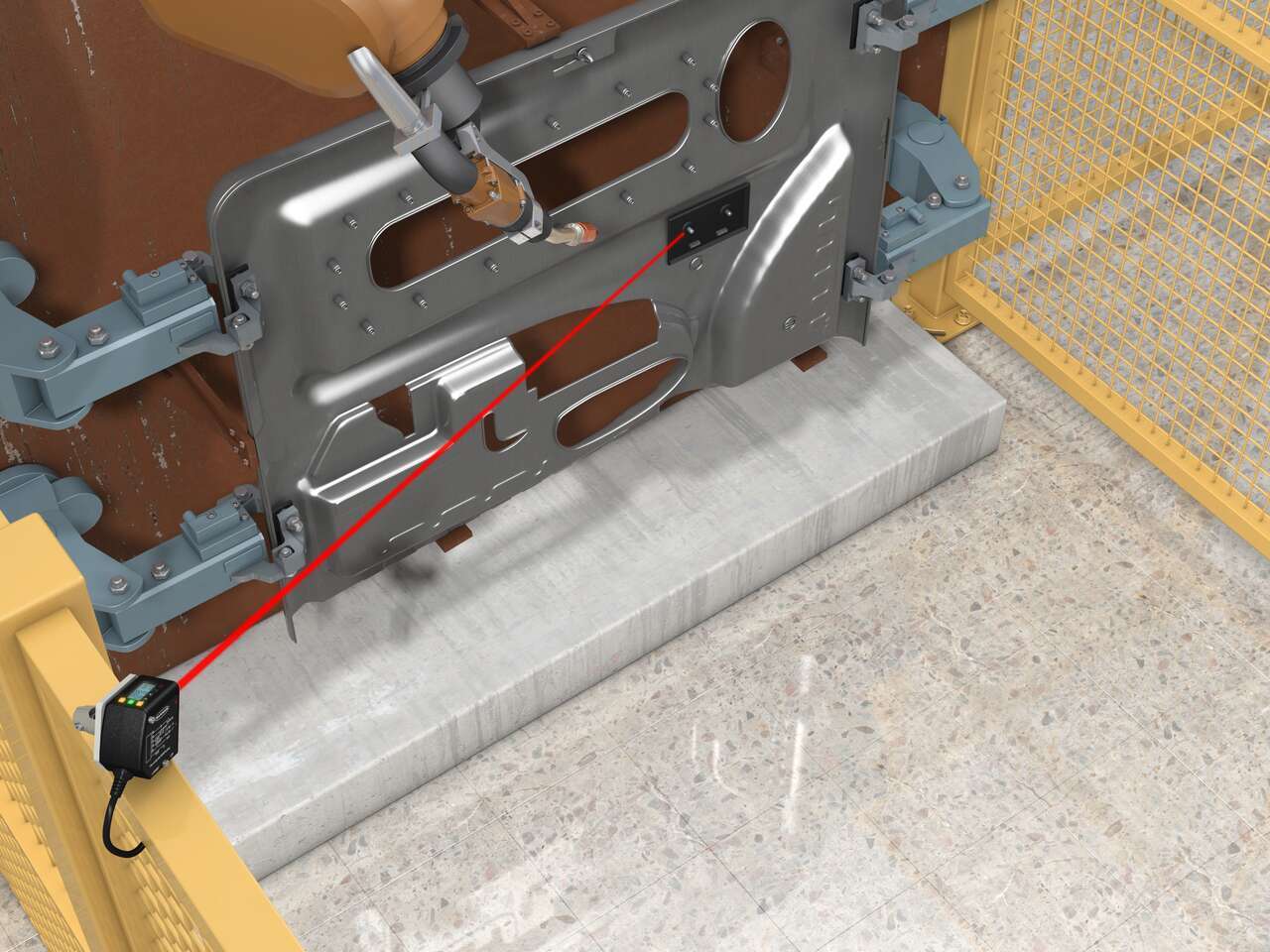
High excess gain enables the sensor to detect items from an angle and it has very high accuracy, so even slight variations in target position will be detected.
Learn More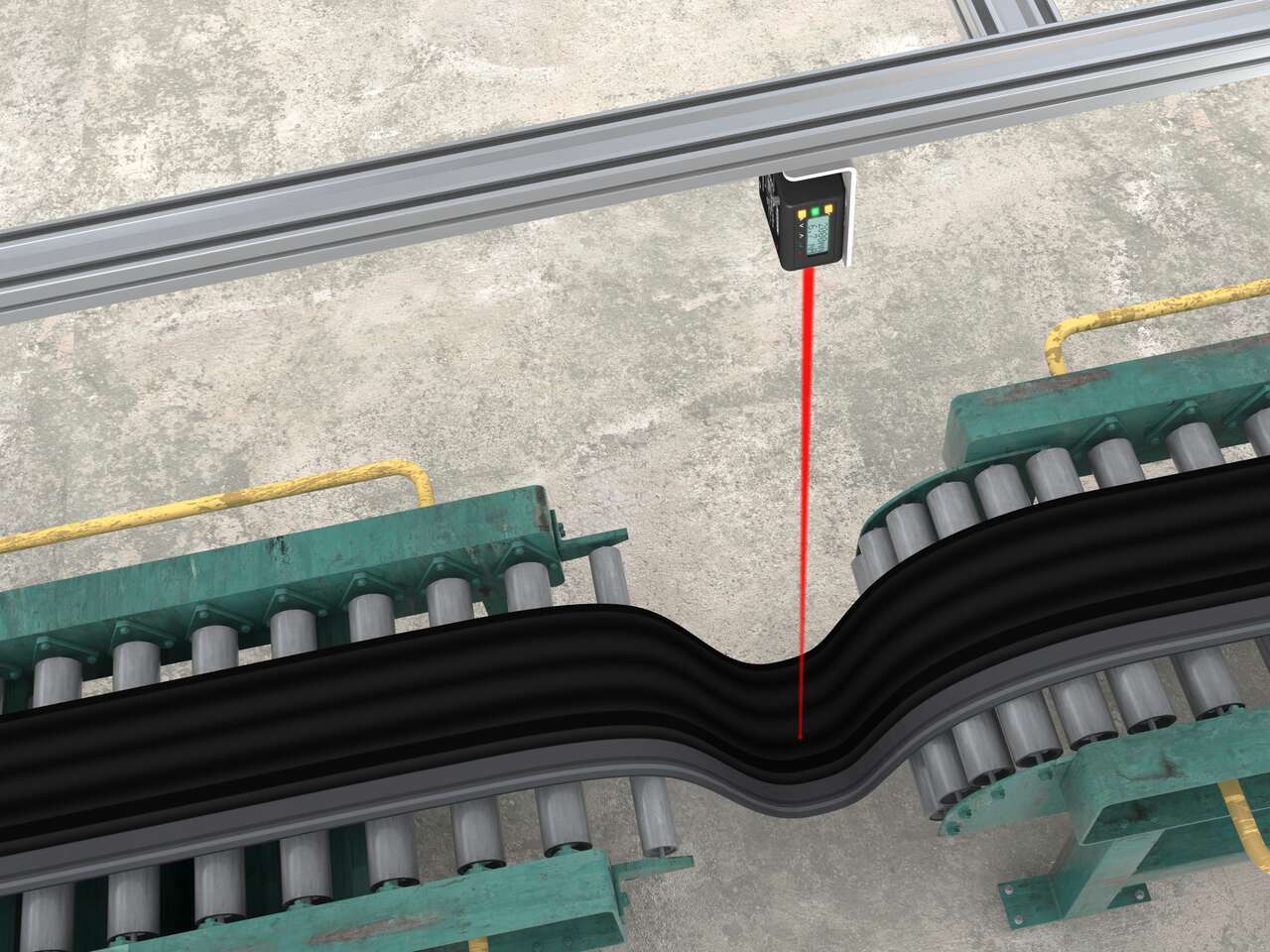
Loops must be closely monitored and machine speed adjusted to maintain proper tension on the material.
Learn More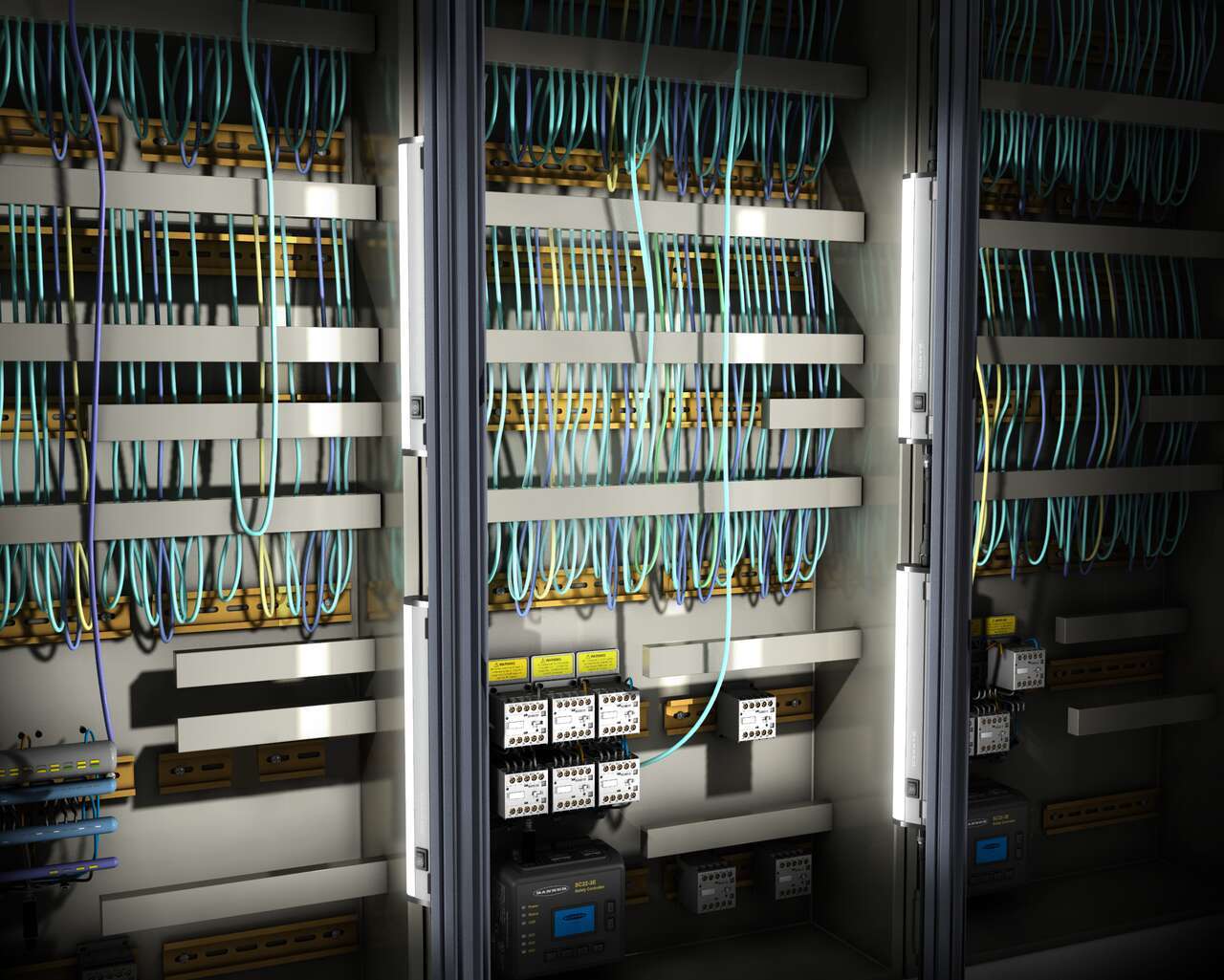
Operators access machine systems through the control cabinet and need Intense illumination of the cabinet facilitates for maintenance and management.
Learn More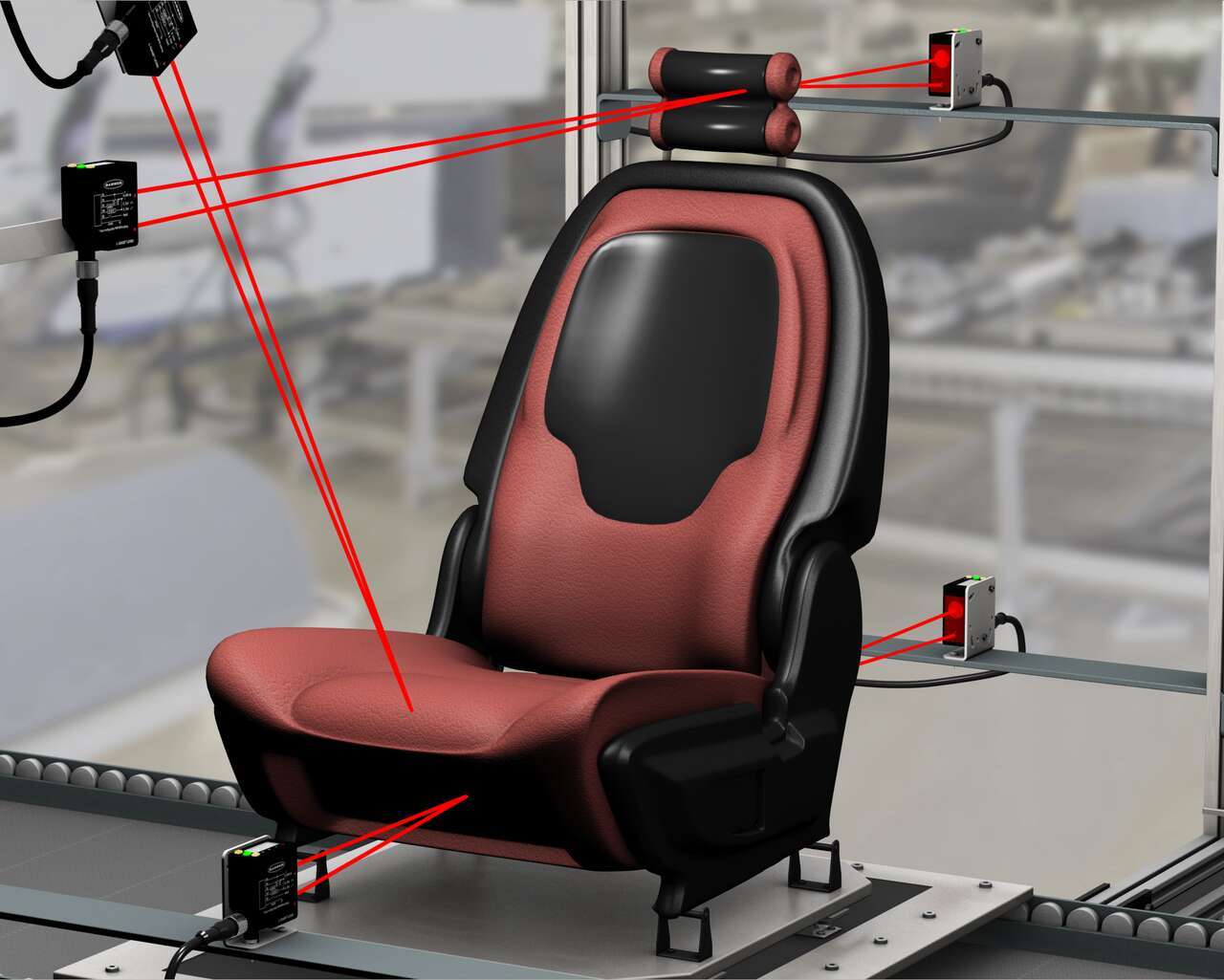
During assembly, inspections are conducted to measure seat height adjustment, forward and rearward movement, and upright and recline motion.
Learn More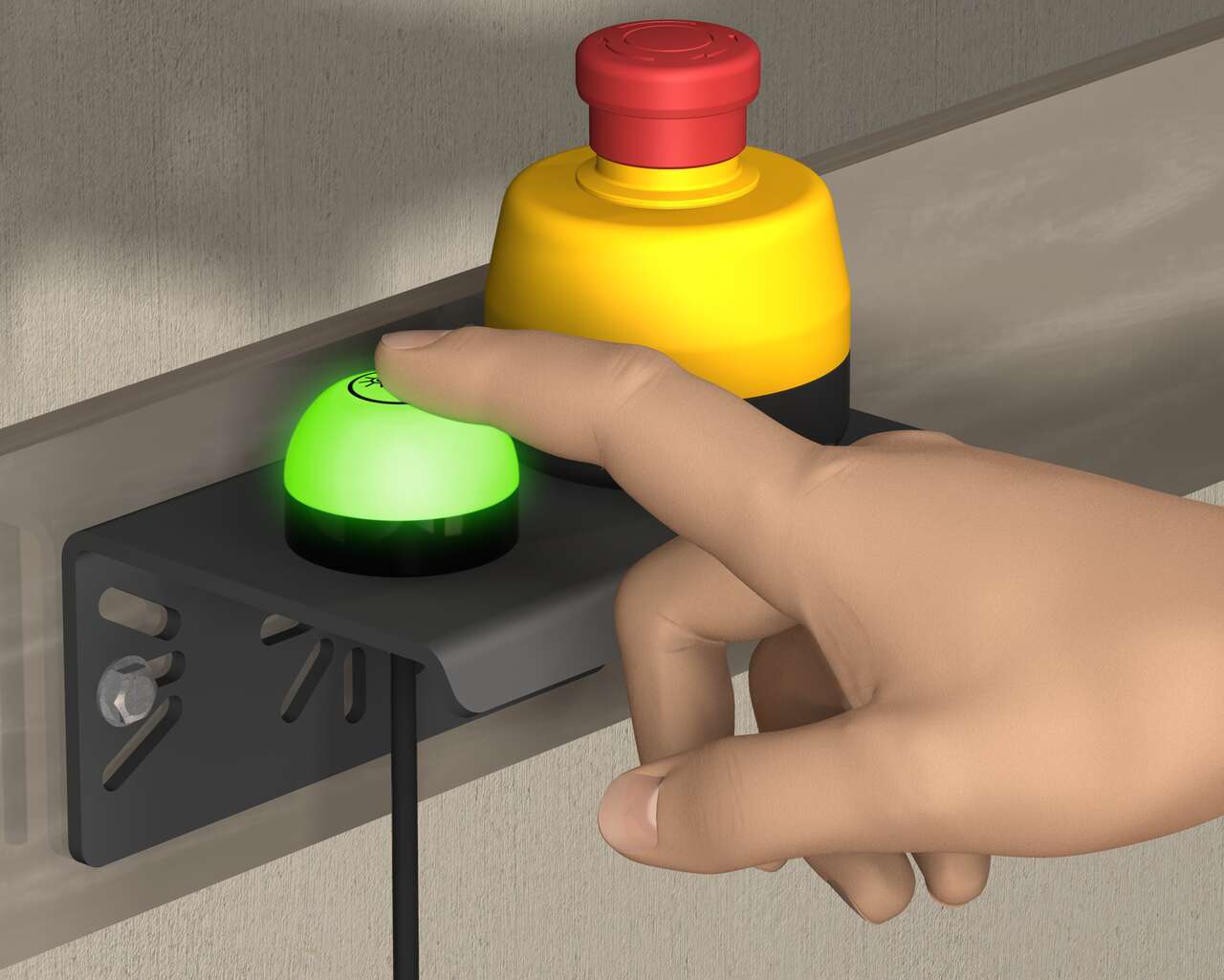
With the all-in-one enclosure, the emergency stop pushbutton combined with the K50 Touch lighted indicator communicates simple status indication in emergency conditions.
Learn More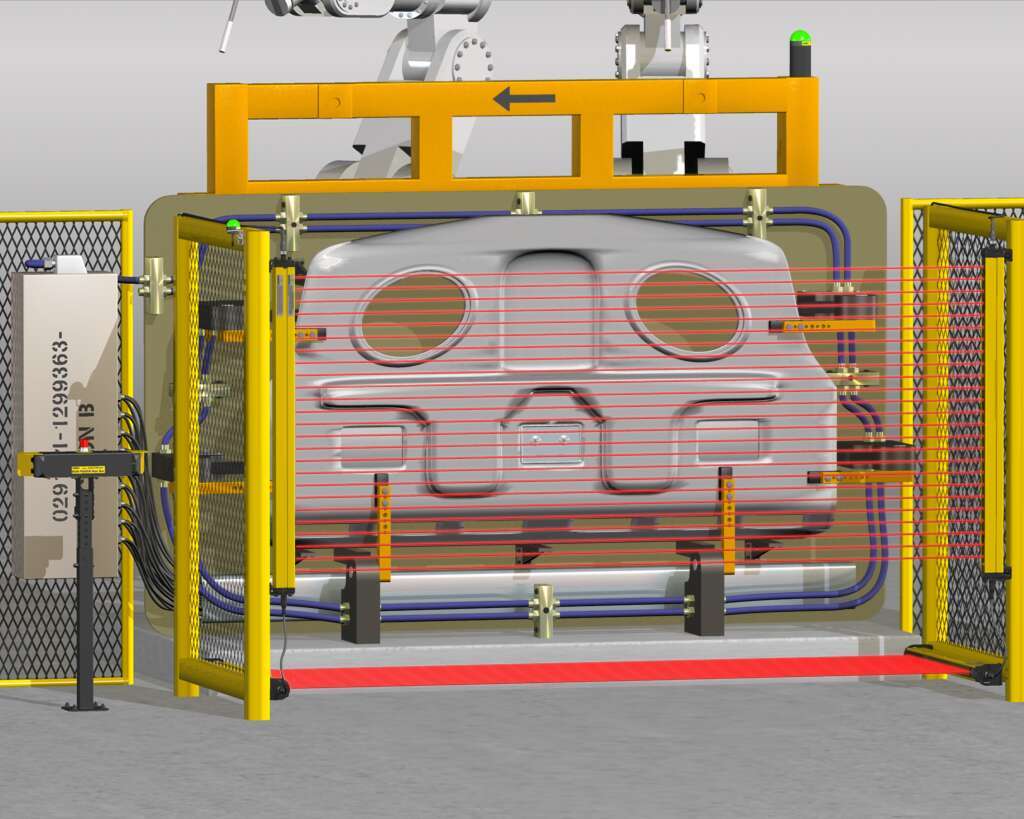
Banner’s EZ-SCREEN® series safety light curtain system is a well established solution for the harsh requirements of welding equipment. With the ability to cascade (series connect) multiple segments together, configurations such as this horizontal/ vertical pair are easily implemented with standard hardware (no master/slave models).
Learn More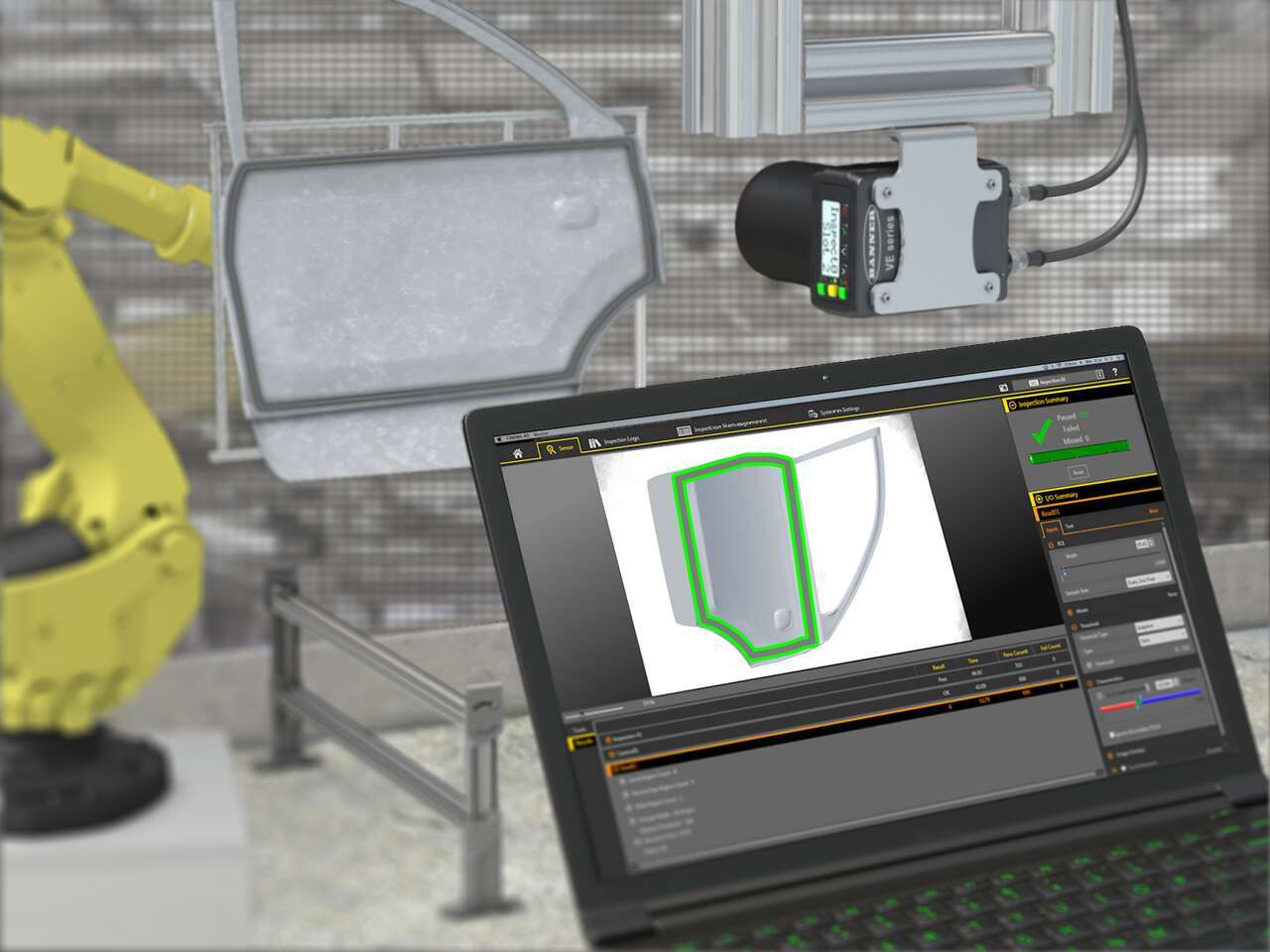
A VE Series Smart Camera, configured to use the bead tool, inspects each door panel for the presence and consistency of adhesive. The camera has a wide field of view and a 2 MP imager capable of detecting even slight inconsistencies in the amount of adhesive applied.
Learn More.psd/jcr:content/renditions/cq5dam.web.1280.1280.jpeg)
Integral hinge will stop conveyor once the gate is opened and the grid is muted when gate is opened.
Learn More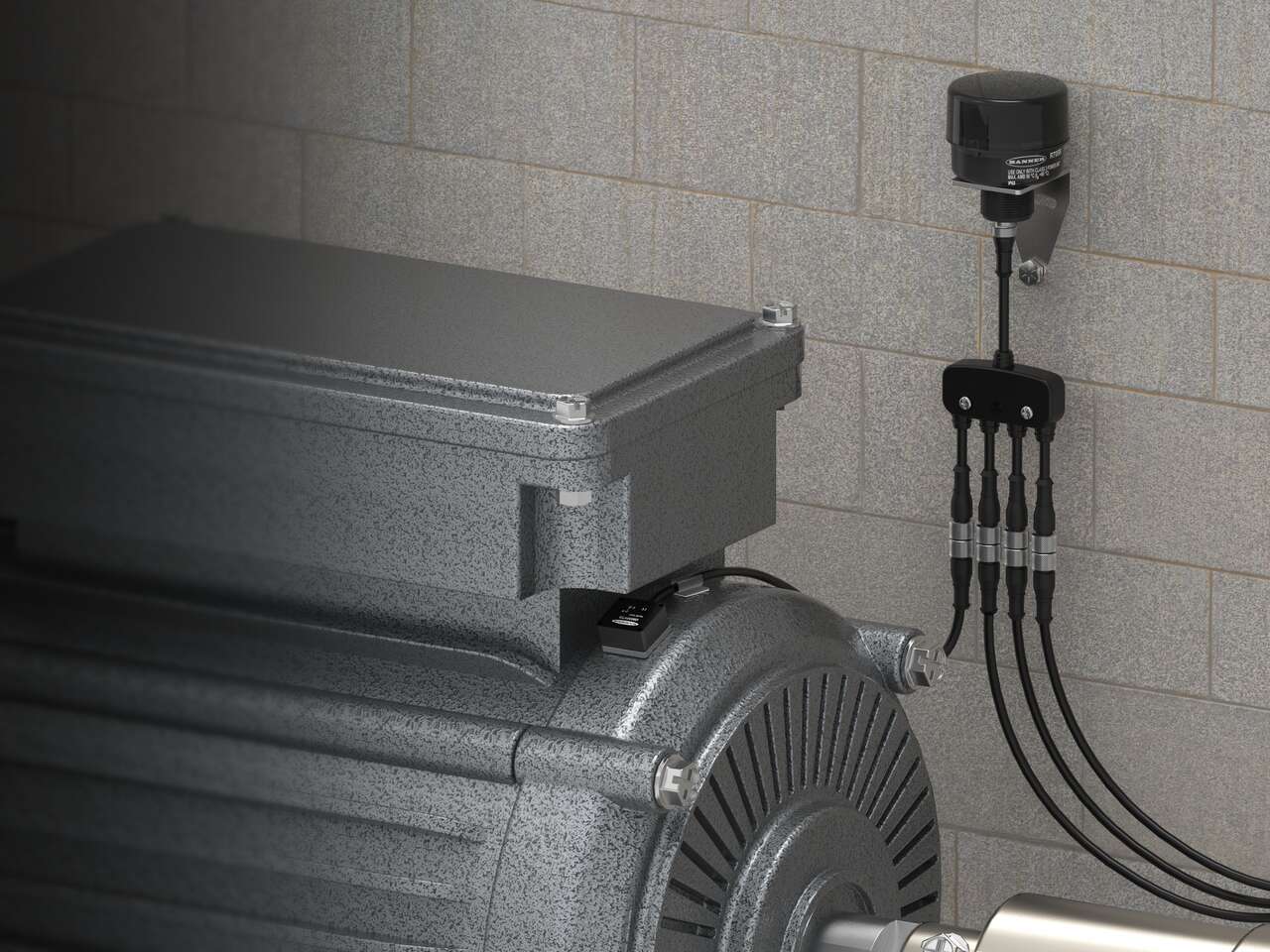
Predictive maintenance enables users to more accurately anticipate when machine maintenance will be needed based on real-time data from the machines themselves.
Learn More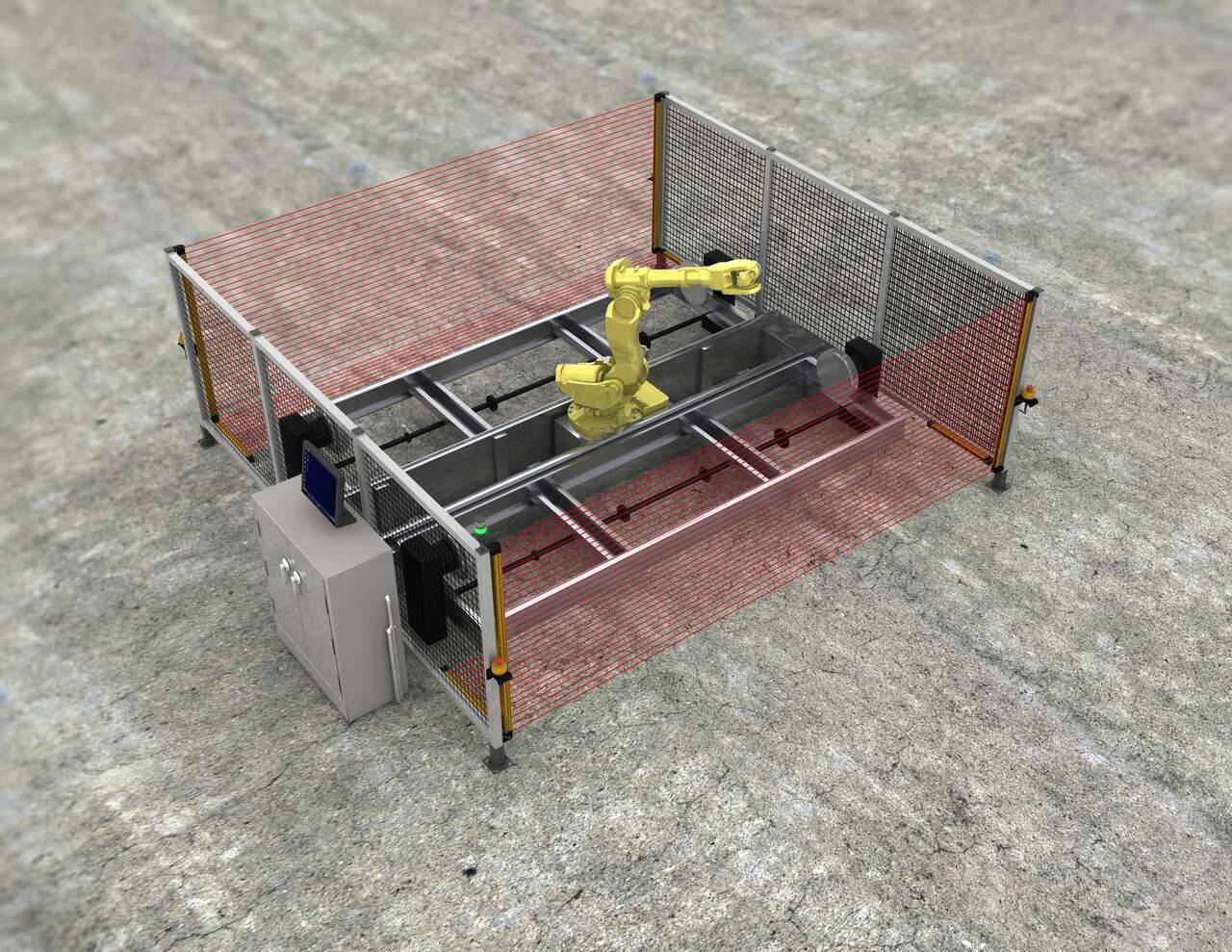
See how Banner’s EZ-SCREEN LS Heavy-Duty Type 4 Safety Light Curtains uses cascading to maximize safety while minimizing cabling and equipment footprints.
Learn More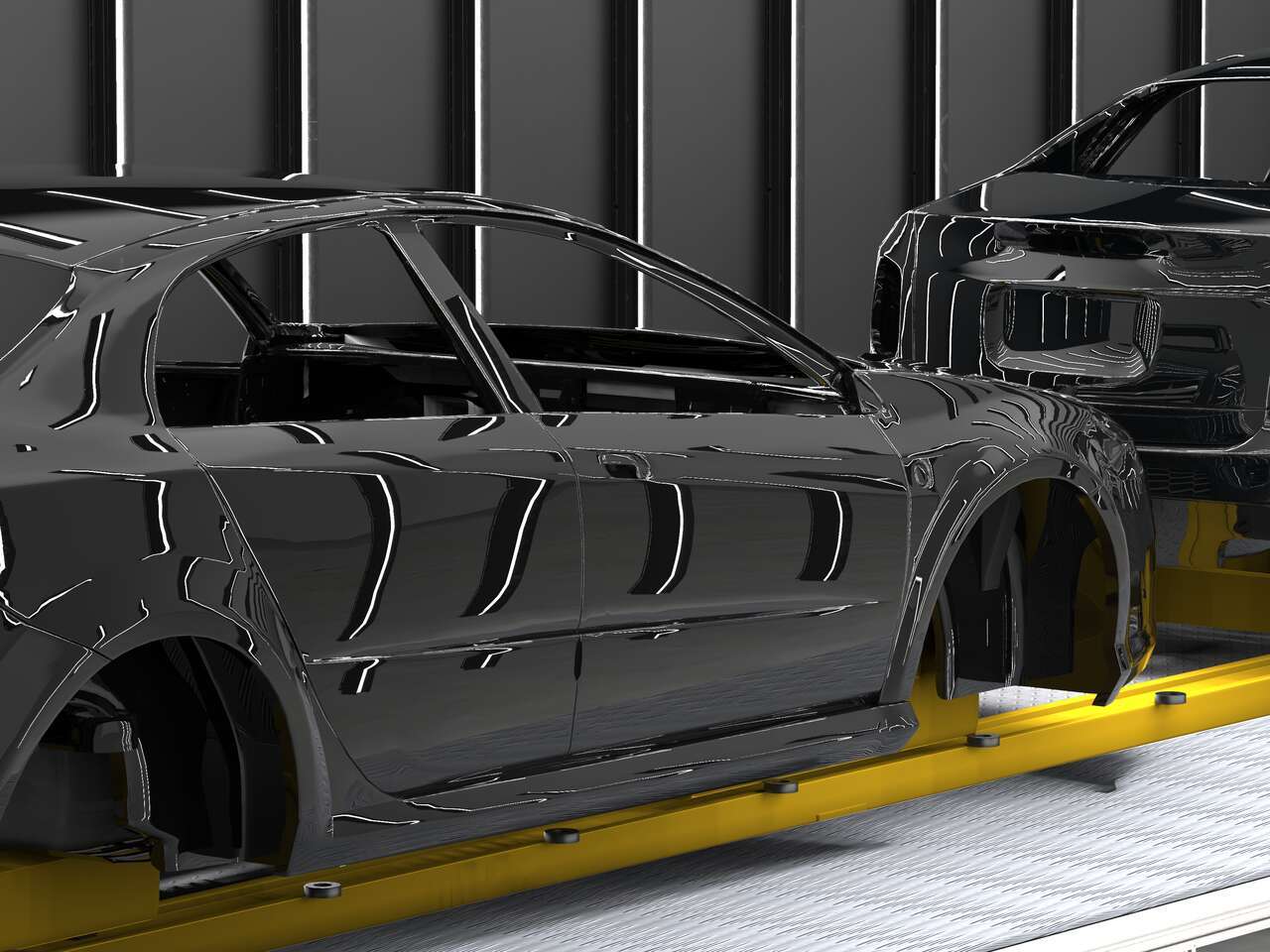
Inspection with high quality illumination, identifies vehicles needing additional work to ensure the highest quality paint finish.
Learn More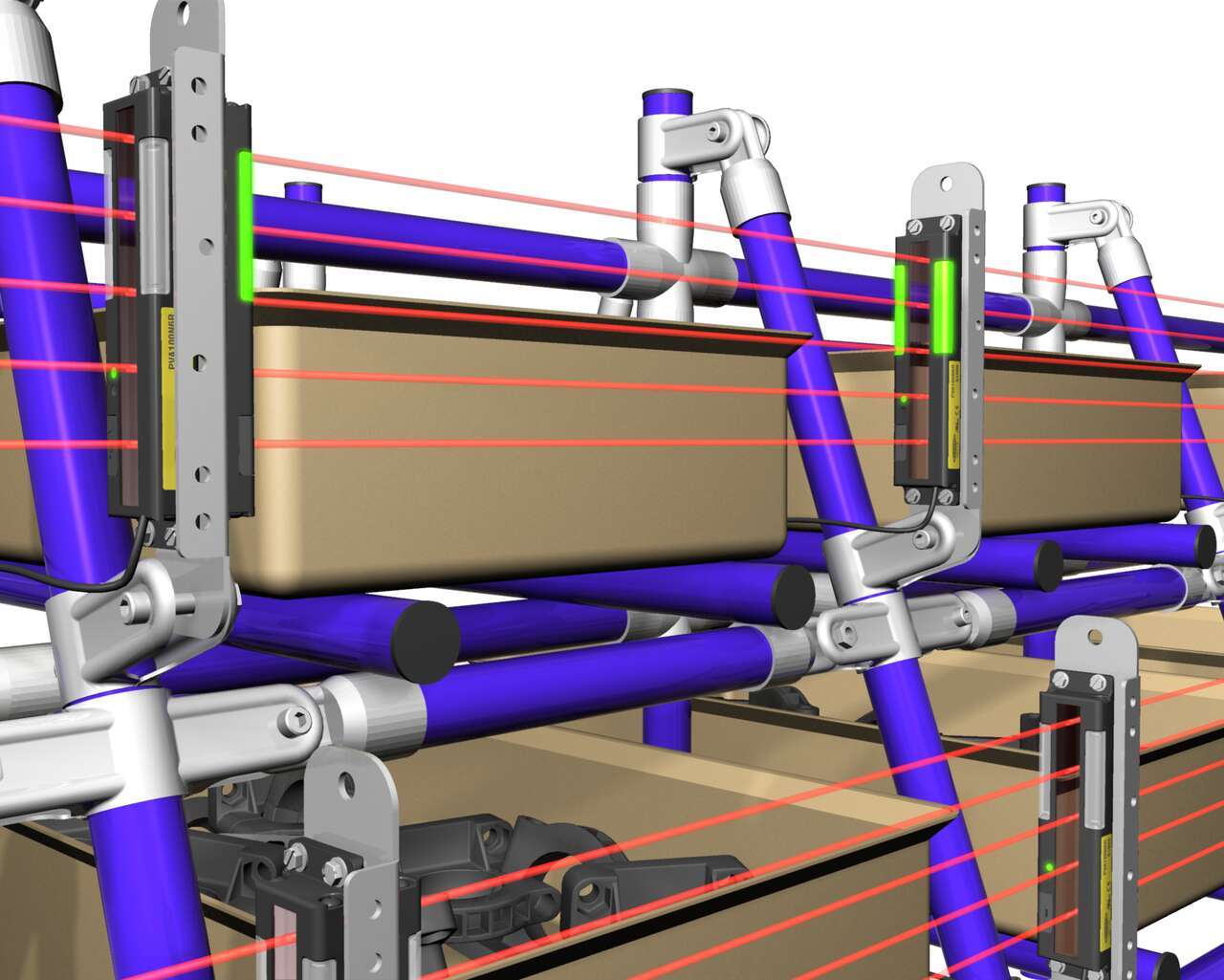
The EZ-LIGHT PVA pick-to-light sensors provide a reliable error-proofing solution for various operation systems. The light indicate to assemblers which items to pick and in which order to pick them.
Learn More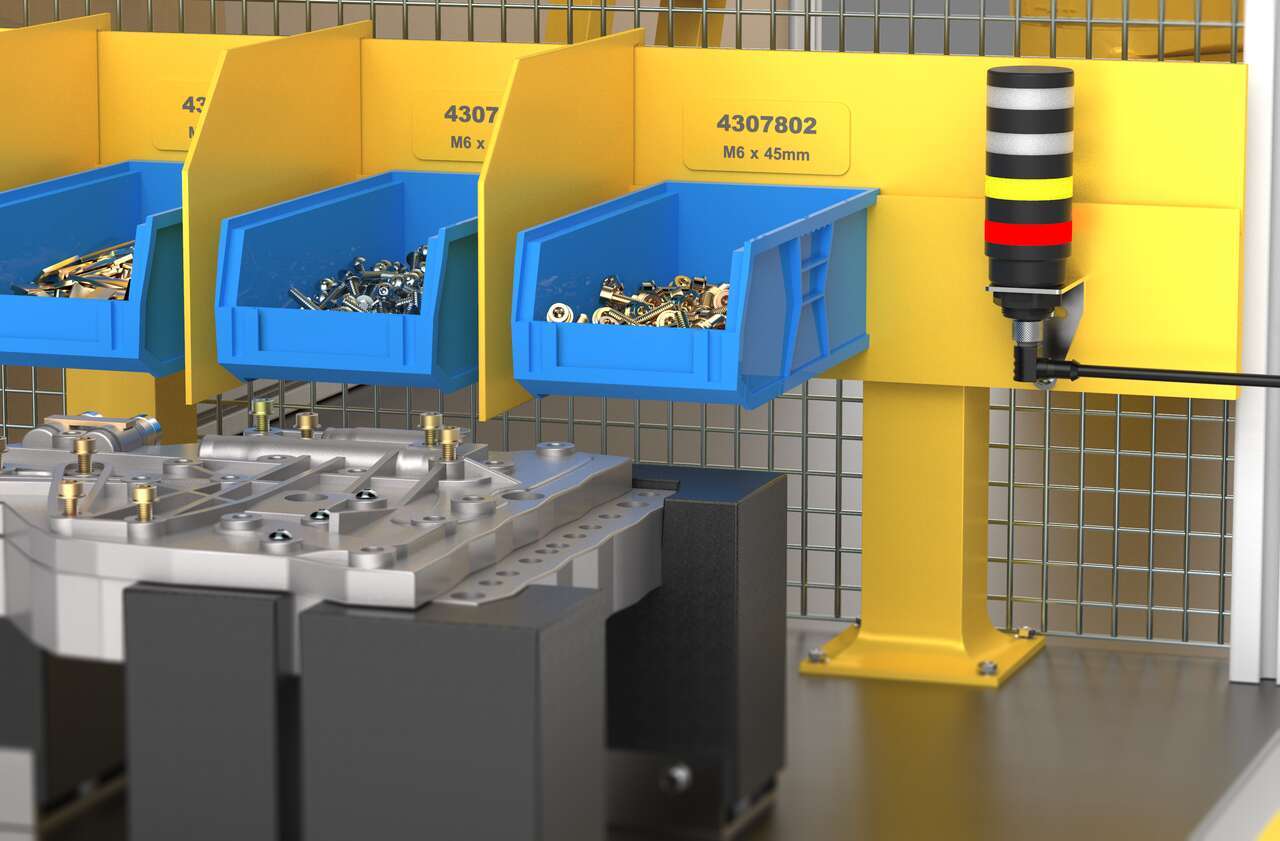
The TL50 Pro tower light helps assemblers meet expected cycle times and support overall takt time requirements.
Learn More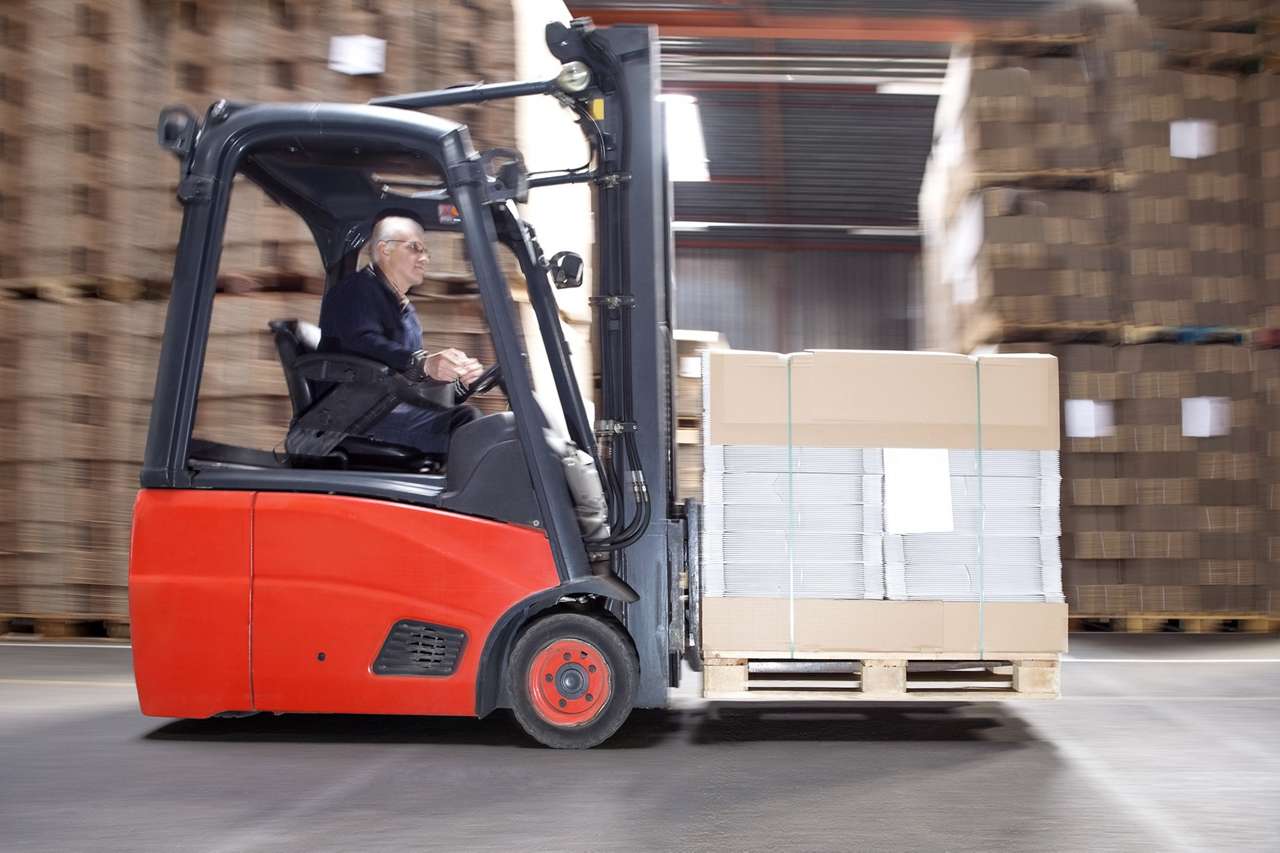
Increase production efficiency by developing a wireless call-for-parts, service, and Andon system that allows for up to 35 work stations to call out to 12 forklifts/Hi-Los using the EZ-Light K70 Touch to wireless Direct Select operator interface.
Learn More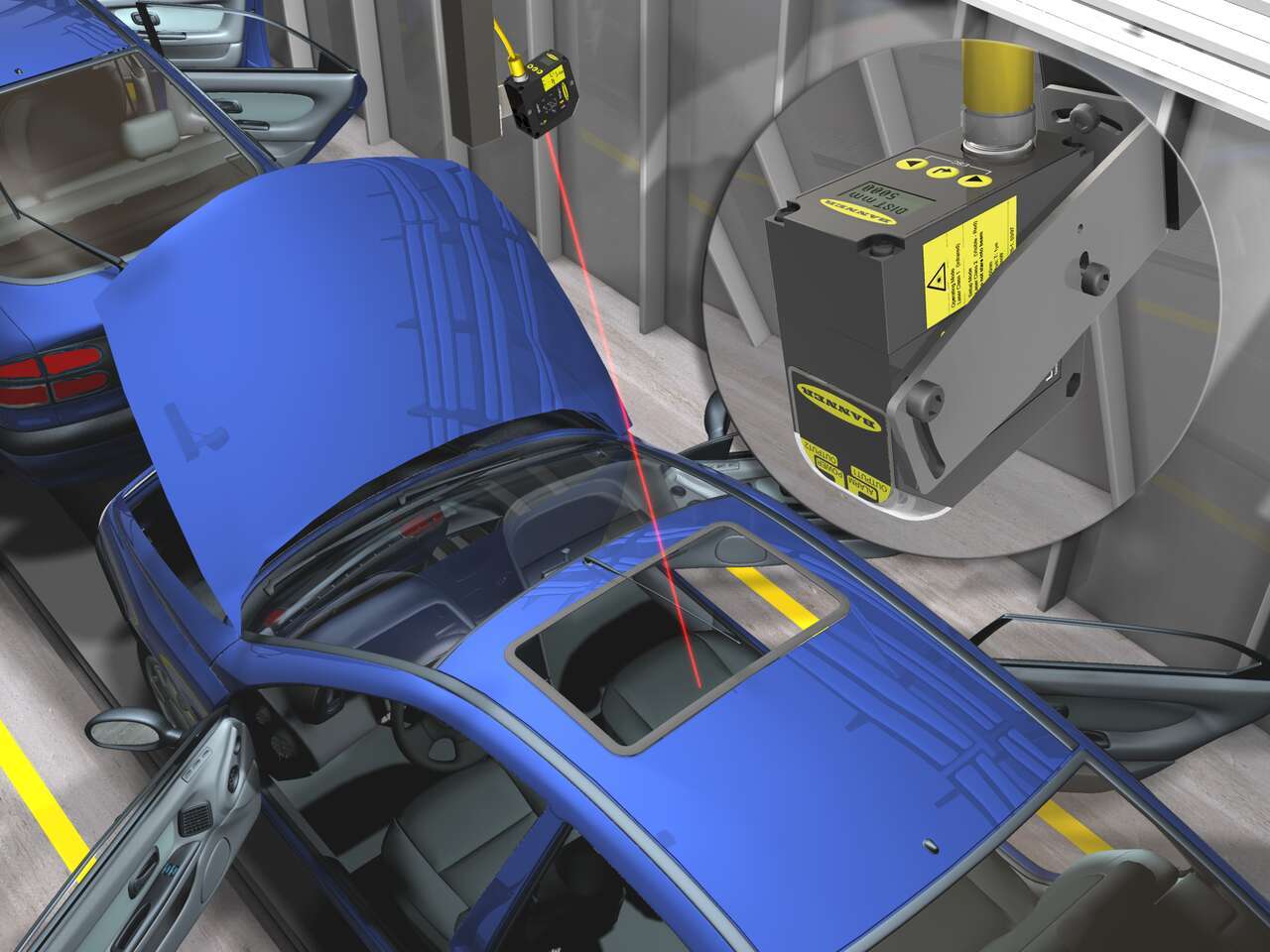
As vehicles move forward on an automotive assembly line, an L-GAGE LT7 time-of-flight laser sensor is directed inside the sun roof to verify that the car seat has been installed and is in the correct position.
Learn More.psd/jcr:content/renditions/cq5dam.web.1280.1280.jpeg)
Sensor solutions to detect the presence of a moonroof on an automobile assembly line where extended range capabilities are required.
Learn More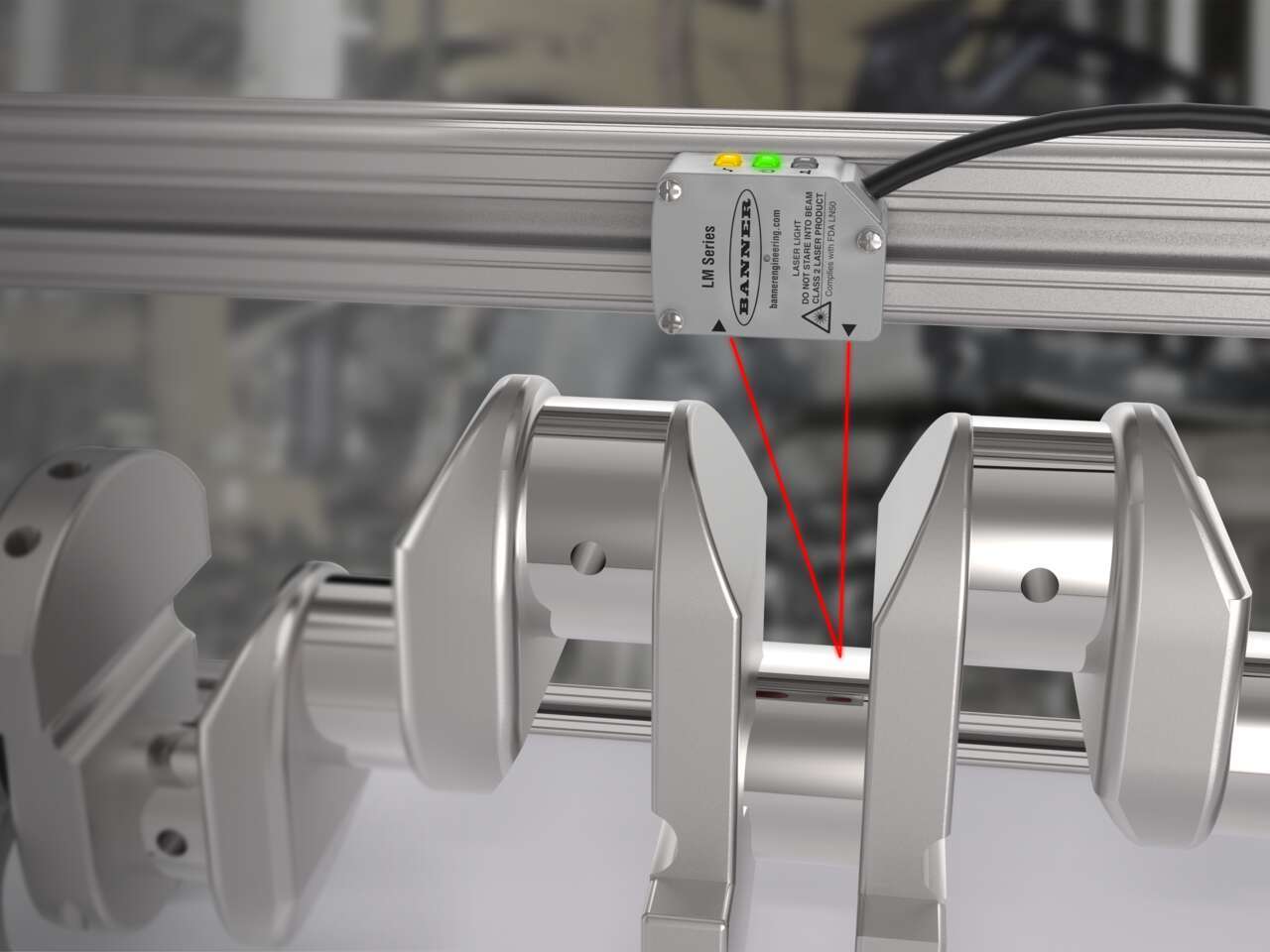
Crankshaft runout measurements must be monitored continuously to ensure that they meet tolerance requirements. Learn how LM Series laser measurement sensors solve this difficult application.
Learn More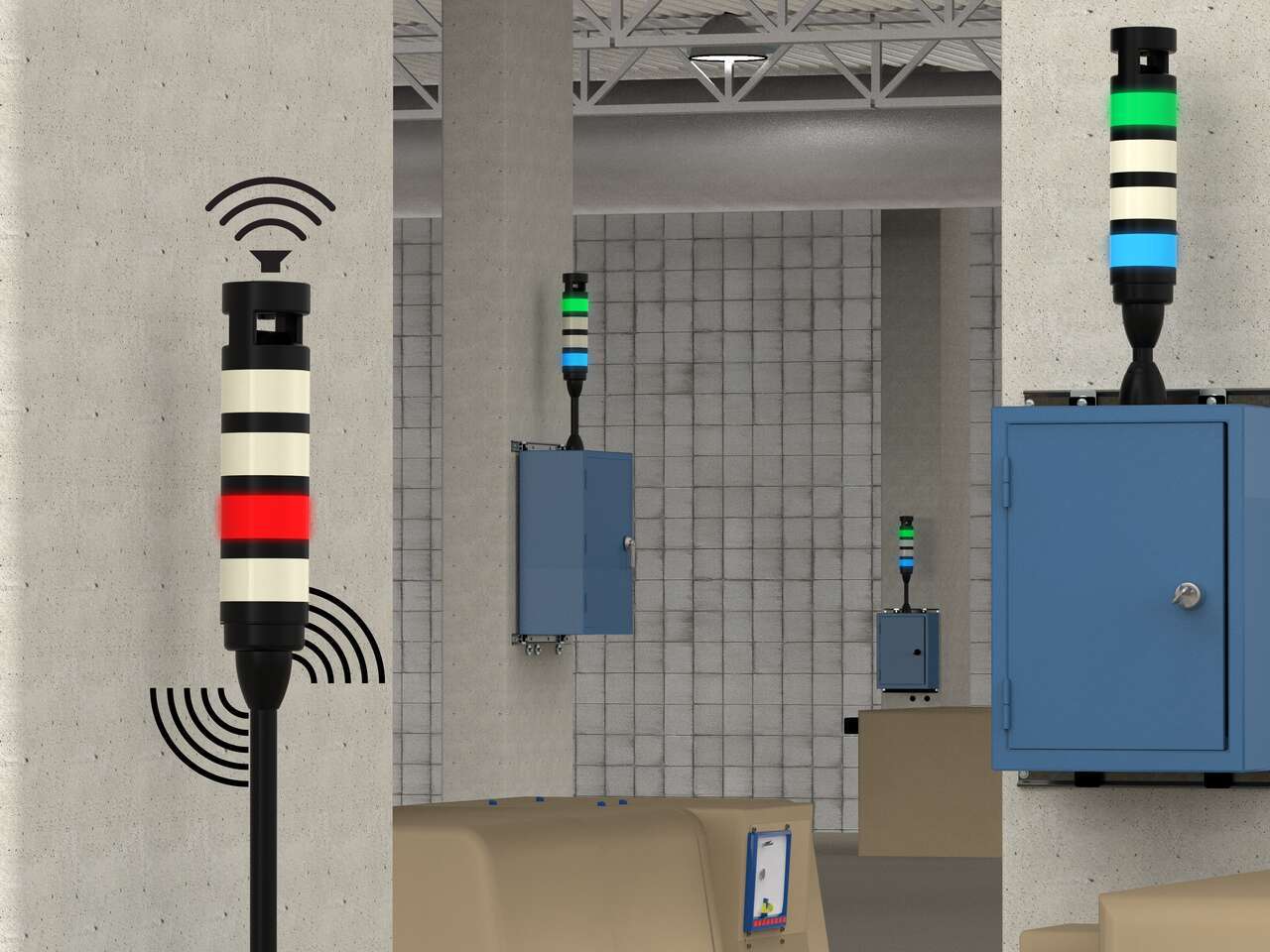
Remote monitoring capabilities provide data for OEE calculations, making it easier for manufacturers to identify and remedy causes of waste within their facilities.
Learn More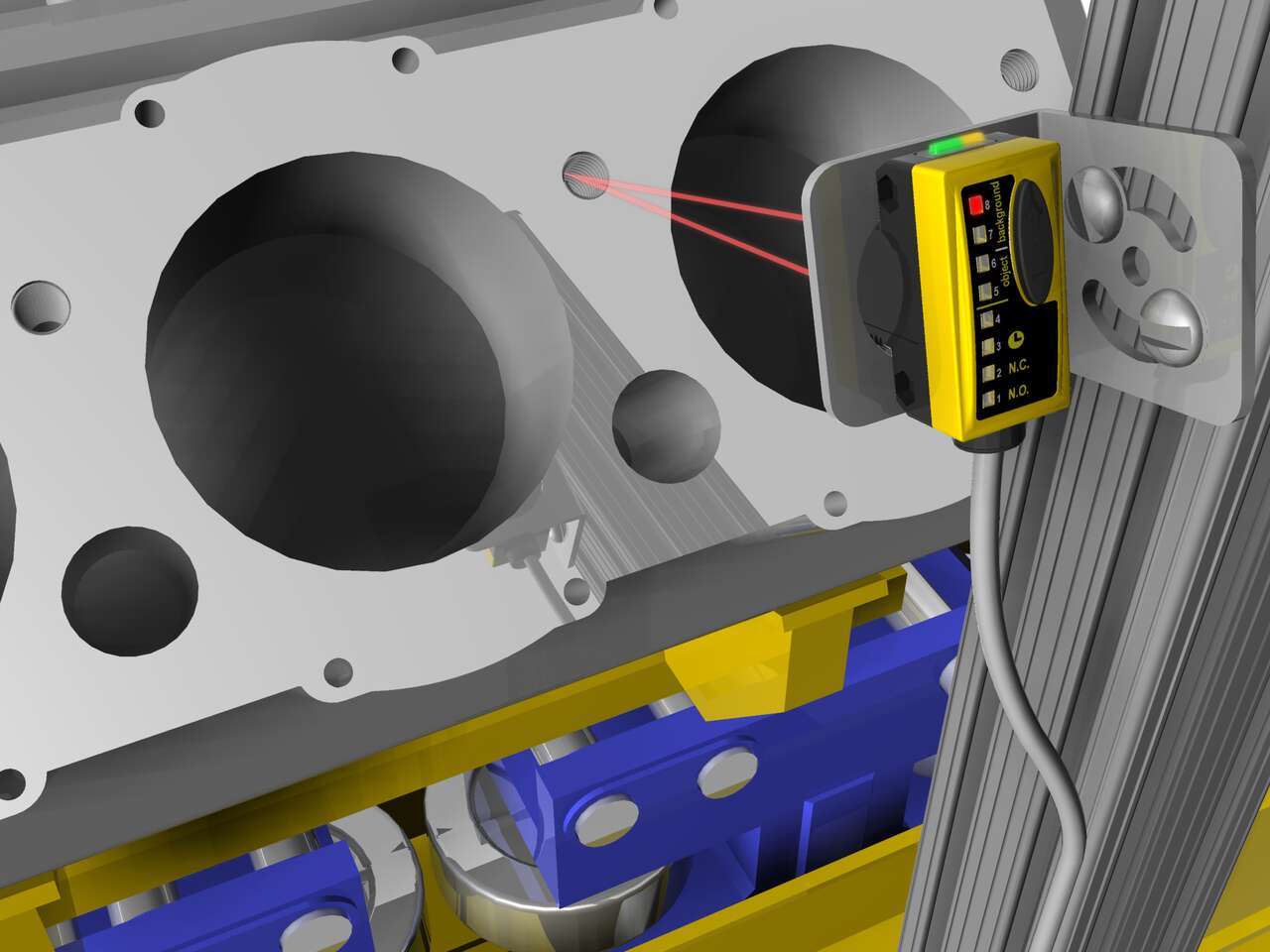
The WORLD-BEAM QS30's narrow laser beam can prevent these mistakes from happening it is necessary to verify, from a distance, that bolt threads have been cut into holes in a manifold.
Learn MoreAutomotive Manufacturing Solutions
Specialized EV Solutions
Learn how Banner solves lithium-ion battery assembly, quality control for electrode thickness, and roll monitoring for jam detection or materials running low.
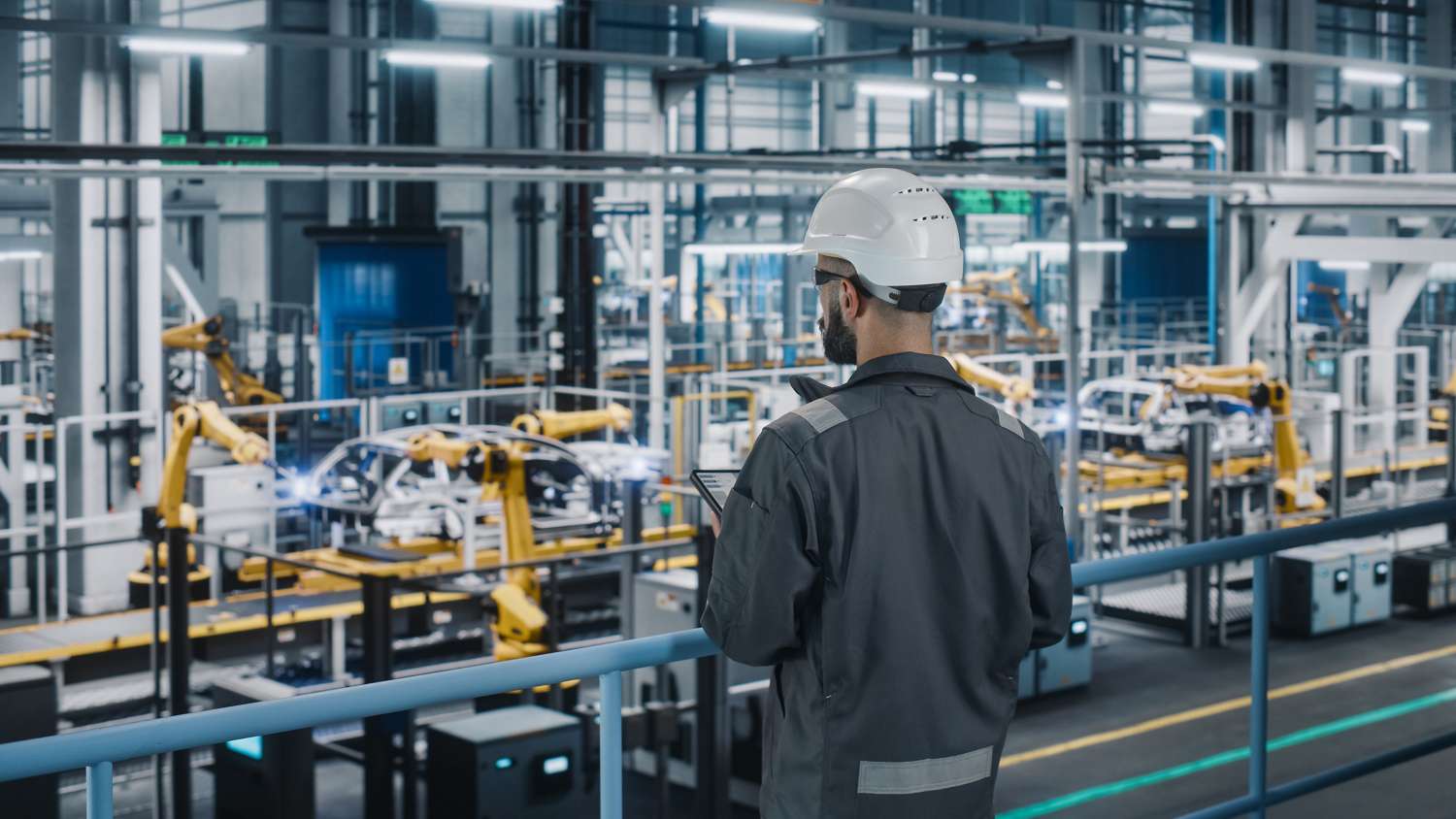
-
Monitor Vibration | Predictive Maintenance Solution
Reduce Unplanned DowntimeWireless Solutions Kits make it easy to monitor remote and mobile assets, collect and act on data, and solve specific applications, such as tank level monitoring, industrial temperature monitoring, and wireless vibration monitoring.
-
Scalable, Easy-to-Use Pick-to-Light | PTL110
Improve Part Picking Speed and AccuracyPTL110 pick-to-light devices are flexible and scalable to a wide variety of applications. With fast response times and flexible installation options, PTL110 systems improve speed, productivity, and quality in picking, kitting and related applications.
-
Easy-to-align safety light curtains | EZ-SCREEN LS
Enhance Worker SafetyBanner’s LS safety light curtains are intuitive, easy-to-use machine guarding devices built to withstand challenging manufacturing and packaging environments.
-
Bright, Energy-Efficient LED Work Light | WLB72
Give Workers the Light They Need to Work EfficientlyThe WLB72 Series High Output LED Industrial Strip Light enhances overall visibility, improves worker productivity, and reduces energy costs in a variety of applications requiring bright, uniform illumination.