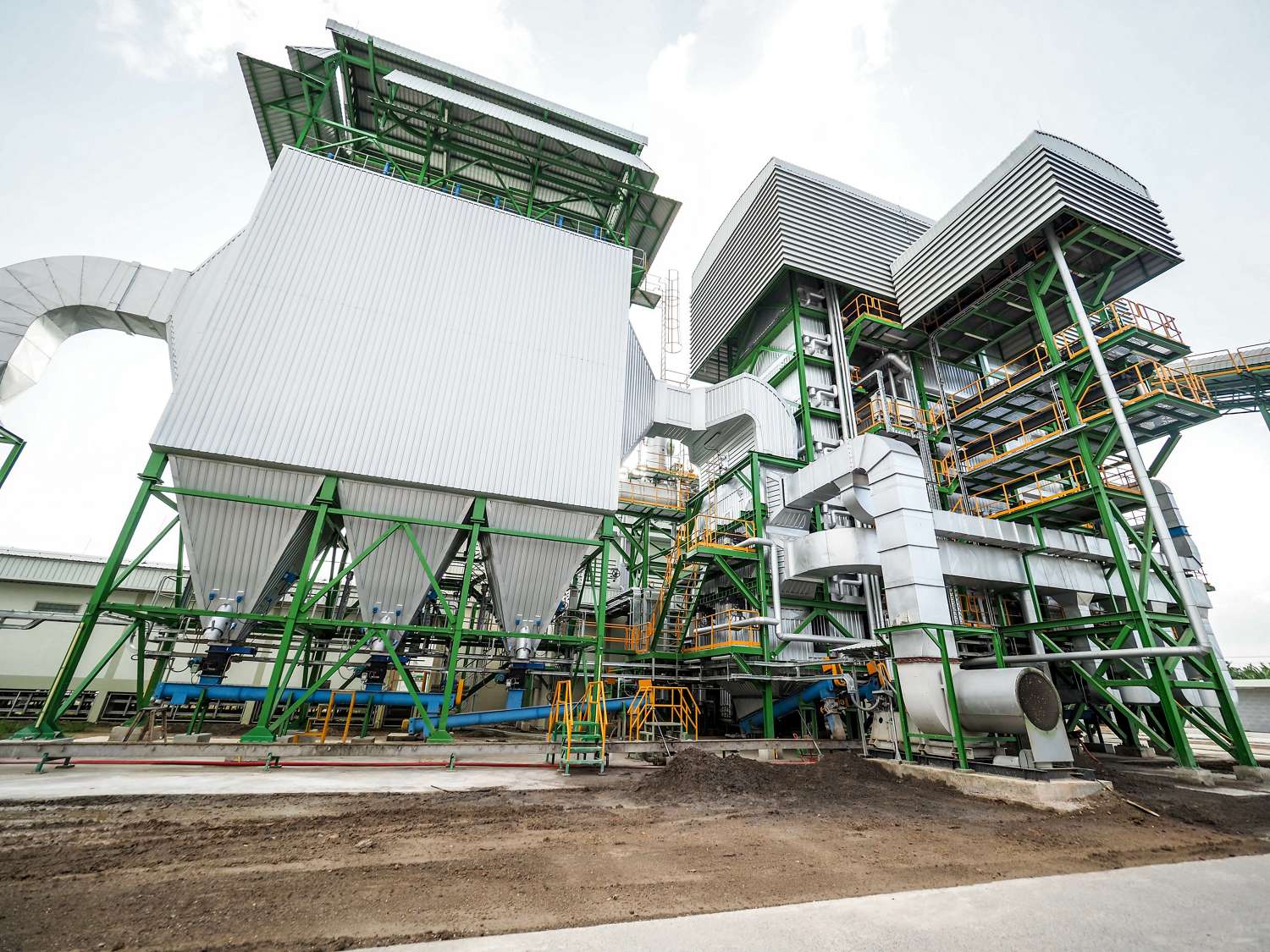
5 Best Practices for Creating an IIoT Dashboard
Industrial Internet of Things (IIoT) technology can provide an overwhelming amount of information about your facility. A cloud platform can collect data from existing equipment, as well as newly installed sensors, to monitor the condition of tanks, motors, extruders, conveyers, and more.
Dashboards are a key tool for making data easy to digest. Instead of looking through lengthy tables of raw data or repeatedly making the same database query, a user can quickly see the most important information. A dashboard is a key way to link IIoT data with context that makes it helpful for operators and leaders to accomplish their goals.
For example, one manufacturer of automotive components deployed an IIoT solutions across multiple facilities and used a templated dashboard for predictive maintenance of motors and pumps. By giving all maintenance people and plant managers a common view of their pump and motor status, they were able to cut down on maintenance calls and even more importantly, save tens of thousands of dollars in costly unplanned downtime.
A dashboard is the first step for making sense of data, diagnosing problems, and capturing value from IIoT solutions. Read on to learn about the five main areas to maximize the effectiveness of your IIoT dashboard.
- Identify Your Users
- Simplicity Is Key
- Minimize Text in Your Dashboard
- Use Icons to Represent Machinery
- Use a Template
Identify Your Users
Understanding who most often uses your dashboards enables you to customize them to focus on relevant data. Here are some common users of IIoT dashboards along with their interests:
Maintenance Technicians:
The primary interests of maintenance technicians include monitoring equipment for irregular operation or faults. The data is used in real-time to address pending failures during scheduled downtime. This audience will be more interested in the deep technical details and the asset-level data. Looking at the plant will be helpful here because they can easily identify and navigate to any problem in the facility.
Process Improvement Engineers:
This audience will be interested in productivity and quality data. If there are multiple production lines or machines producing the same thing, then this audience will want to see these compared with one another, so they may begin to understand why some lines out-perform the others. Companies using statistical process control for improving quality will benefit from a platform that aggregates all this data in one location instead of having it localized to the process or machine.
Maintenance Managers:
While the maintenance technicians use their dashboards to address immediate concerns, the maintenance managers will want to have a broader and longer-term perspective. For example, being able to see the trends in downtime across the facility would help maintenance managers determine when spare parts should be ordered, or if equipment needs to be replaced. For this audience, categorizing the equipment based on the importance to the operation will help maintenance managers identify where the most time is being spent and where long-term improvements can be made.
Plant Managers:
A plant manager is responsible for all the operations on the floor and ultimately needs access to the data employees use. They need the ability to identify bottlenecks and overall productivity improvements. However, the plant manager will still likely want a highlevel view of the facility and any active alarms, such as outstanding maintenance requests, out-of-spec production delays, and other irregular events. Managers should then be able to access other personas’ more detailed dashboards if they need additional information.
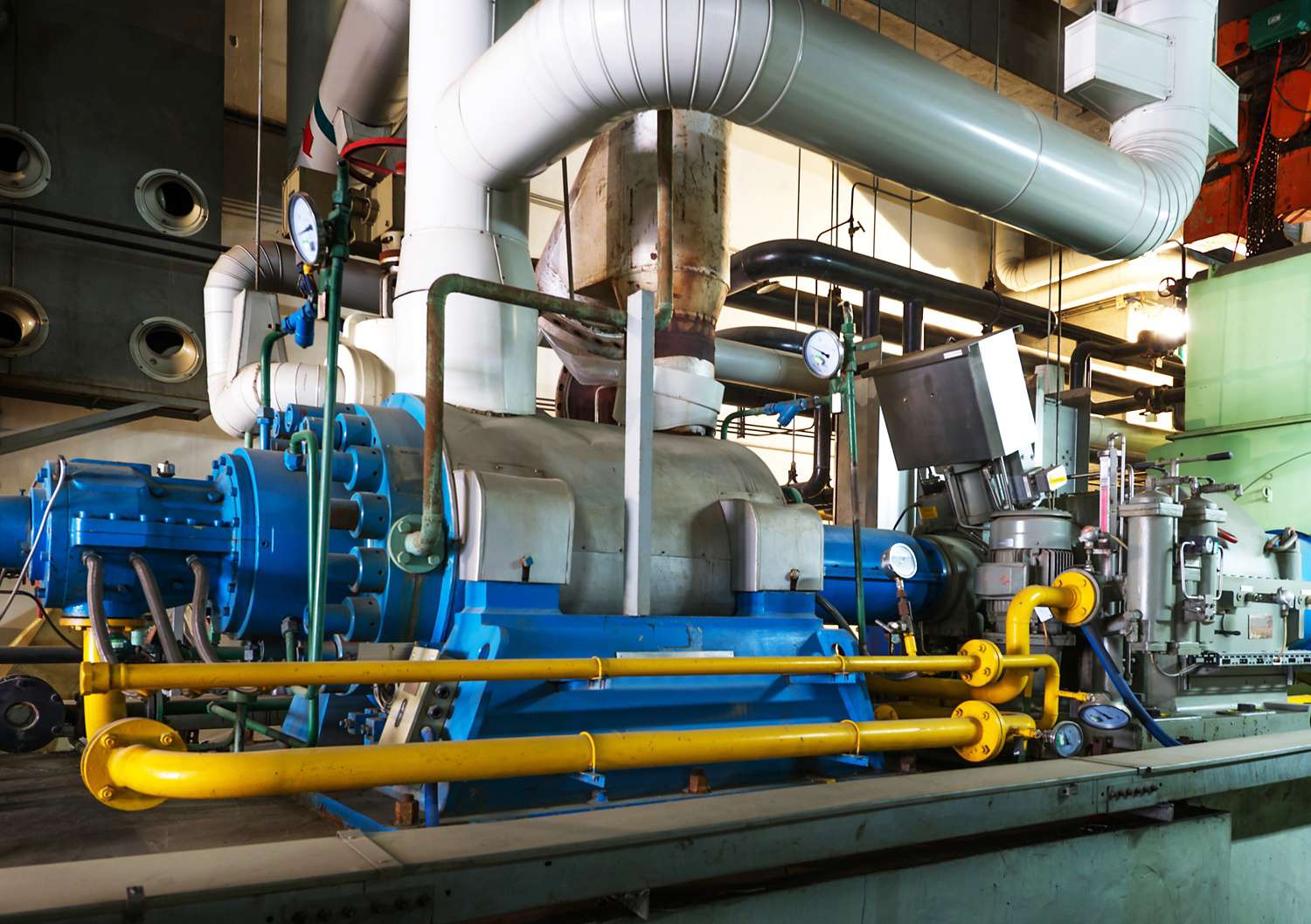
Looking for a Printed Copy of This Page?
Dashboards are a key tool for making data easy to digest. Download the 5 Best Practices PDF to learn about the five main ways to maximize the effectiveness of your IIoT dashboard.
Simplicity is Key
It can be tempting to show all the data in one view. Don’t overcomplicate it. Try to keep each dashboard focused on the most relevant data. Think of it like reading news headlines: the most important performance data should be the first thing you see. Secondary information is less of a priority and should be reflected as such in your dashboards. Limiting how much information you put in dashboards keeps them organized, accessible, and simple to maintain. This is particularly important for users who monitor a variety of conditions, such as tank level, temperature, part counts, and more. As a rule, share a specific piece of information once, in the simplest form possible. For example, if you are representing the fill level of a tank so that an operator can be notified to refill it, use a visual indicator widget such as a gauge and avoid adding extra level charts, or graphics.
On the other hand, plant managers or controls engineers would find more value in trend lines, as well as correlating tank level with productivity data, but they may need less specific information about the exact current state of a particular tank. The simplest form of information will differ depending on your stakeholders, so remember to start with your users’ requirements. Another tactic can be to create a dashboard that focuses on the data you need to solve a single problem.
Minimize Text in Your Dashboard
Did you know that research from MIT suggests that the human brain can process an entire image that your eyes see in as little as 13 milliseconds?1 Keep this in mind when you label your dashboards with text and icons.
A dashboard is best utilized for reading key data quickly. It should include high-level information and overall performance data; it is not a full report with detailed analysis of factory performance. It can be tempting to use an abundance of text to describe what is being monitored, but featuring only essential information enables users to quickly monitor the machines and respond to critical incidents. Use text for key labels and descriptors of assets that guide the users’ eyes to the most important information. Show, don’t tell, what the users need to get from the dashboard. This will offer an organized overview of critical information and prevent confusion.
1 Trafton, A. (2014). In the blink of an eye. MIT News. Retrieved from: https://news.mit.edu/2014/in-the-blink-of-an-eye-0116
Use Icons to Represent Machinery
To make your dashboard immediately valuable, use visual cues and patterns that a user is already familiar with. It is easier to remember which asset on the dashboard corresponds to a machine if the graphics are tailored to the specific application. Add your own images to the background of the dashboard to customize it even further. For example, a simple map or blueprint of a facility can be the background of a dashboard, and specific asset icons can be overlaid on top. To clarify where a specific sensor is on a piece of equipment, add a picture of the entire machine and place icons over the spots where they exist in your actual facility. Therefore, it is important to have a dashboard system that allows you to add images and graphics and then overlay them with relevant indicators.
For example, Banner Cloud Data Services includes a built-in library of icons that represent different sensing modes and machine asset types, from motors and tanks to differential pressure and amperage. These icons can be color-coded to indicate connectivity or threshold alarms. This gives the users a true at-a-glance view of an asset and its status.
Use a Template
Creating custom dashboards enables total control of what assets you want to monitor. You have the option of customizing alarms, background colors, graphs, tables, and more. If you would rather use an existing dashboard instead of creating your own, many of Banner's kits for condition monitoring and performance tracking, such as the Expansion Kit or PPM Kit, generate pre-configured dashboards. Banner’s Wireless Production Performance Monitoring (PPM) Kit is a stand-alone, add-on solution that is compatible with new and existing production machinery, without the need for modifications. It comes preconfigured with a DXM1200 Controller and one Q45 all-in-one sensor node or a TL70 node. The SmartSolutions Expansion Kit is an end-to-end monitoring solution designed to simplify and streamline the deployment of IIoT solutions into your plant. Preconfigured dashboards give you a template to adjust and build on. Data can be analyzed to help you follow trends, verify compliance, solve problems, and make informed decisions about your business. Simply unpack the box, install the devices, and start collecting data.
Dashboards Enable At-A-Glance Status Indication for Proactive Maintenance
Dashboards can be tailored to address the key information that is applicable to your business and employees. As an immediate source of information, dashboards can also translate data collected by condition-monitoring systems into sales data, financial statistics, and other analytics. Without a condition-monitoring system, workers must perform routine maintenance checks on their machines and manage unexpected downtime in their factories. Such decreases in productivity are costly. IIoT technologies allows you to make better-informed decisions based on gathered data. Banner’s cloud platform makes this data accessible to everyone, from plant floor operators to corporate executives. Having a unified view of production operations lets you identify inefficiencies, improve performance, and increase profits.