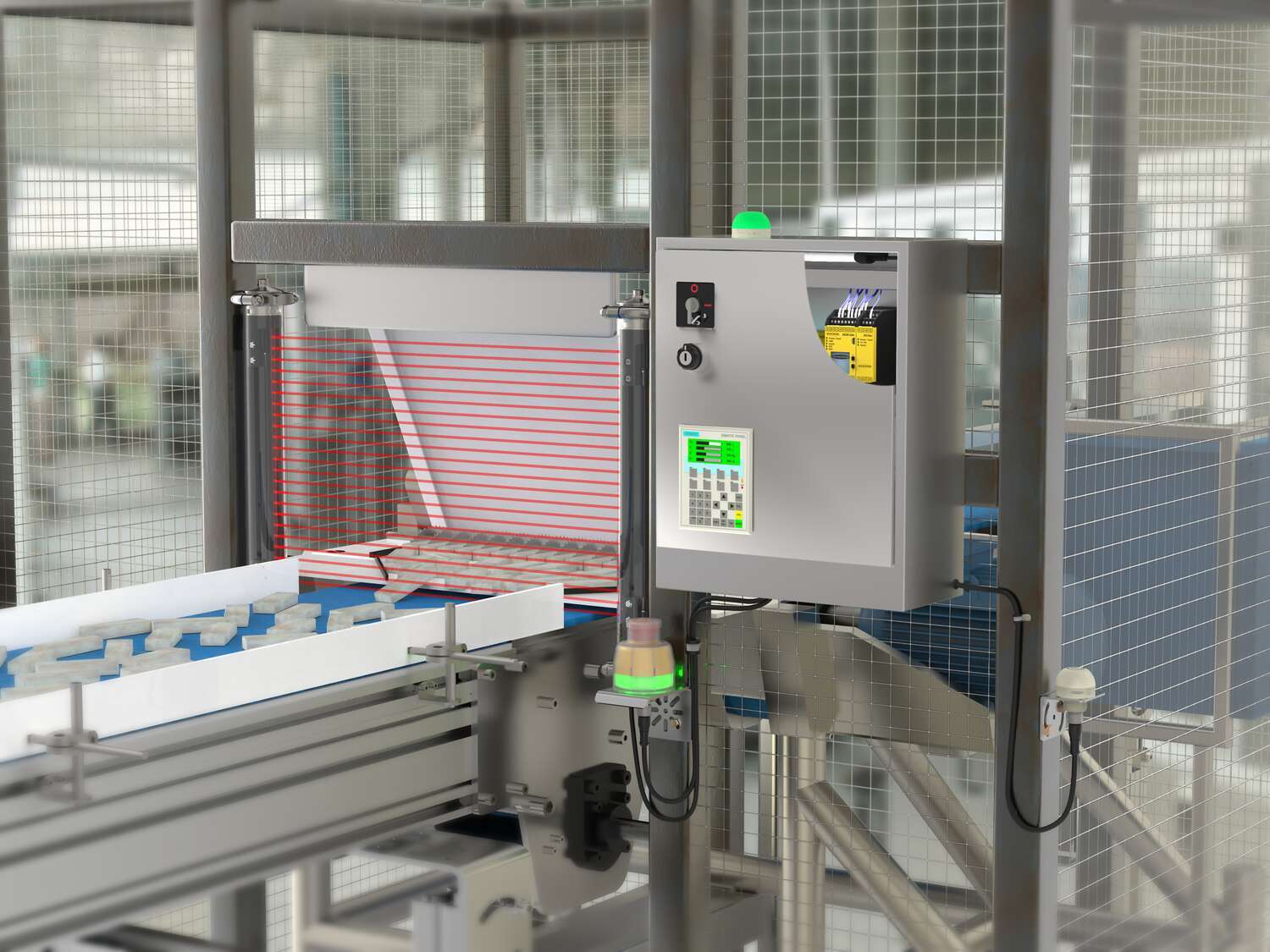
Machine Guarding
What is Intuitive Safety?
We want our customers to know that safety doesn't have to be difficult because we make it easier. When we design safety solutions, we ensure they are easy-to-use—from installation to day-to-day system management. From aligning a light curtain with visible alignment indicators to setting up a complete safety system via our drag-and-drop safety controller GUI, customers can get up and running quickly without steep learning curves. After installation, users can more easily manage their safety system with integrated local indication and remote monitoring capabilities.
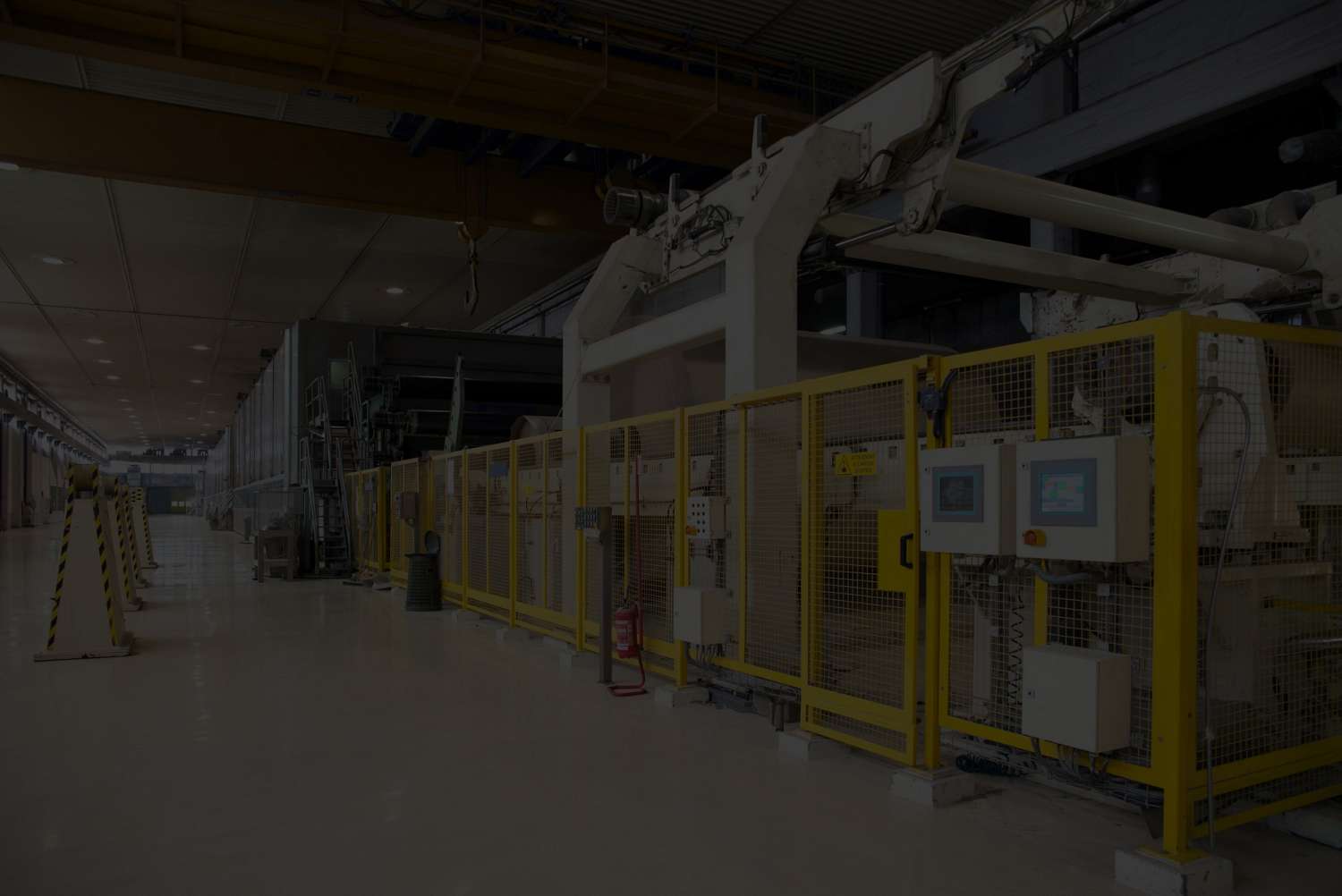
-
Featured Application | EZ-SCREEN LS
Safety Measures for Meat Slicing Machine in Harsh ConditionsSafety light screens on a meat slicer protect operators from sharp blades while in operation. The environment is harsh and frequently exposed to chemical washdowns. The EZ-SCREEN LS with hygienic enclosure keeps personnel safe while preventing water and chemical damage to the light screen.
-
Featured Application | EZ-SCREEN LS
Small Assembly Station Protection with Light CurtainsEZ-SCREEN LS safety light curtains have no DIP switches, feature end-to-end sensing, and can be easily installed with automatic configuration. The use of side mount brackets creates a quick and simple installation with adjustments made from the front side of the EZ-SCREEN LS arrays, saving time during setup. Maximizing machine uptime and reducing repair and replacement expenses helps companies remain competitive.
Learn more about how Banner solves machine safety challenges
A More Intuitive Way to Safeguard Machines
Safeguarding machines helps ensure safe, smooth operation and avoid unplanned downtime—and it's a necessity. But safety devices and systems can be complicated and challenging to commission, operate, and troubleshoot.
Intuitive safety solutions from Banner Engineering make safety simple by combining easy-to-use safety devices with LED indication for fast commissioning, visual management, and remote monitoring of safety systems.