Beverage: Primary Packaging
Primary packaging for beverage producers begins with the introduction of empty containers onto the line. Before moving onto secondary packaging, containers will be rinsed, filled and finally capped at very high-speeds. All along the beverage filling line, each phase in this process poses unique challenges to equipment and operators.
Banner is a leader in the design and development of products and solutions that bottlers, all around the world, rely on to perform in this challenging area. From stainless steel, IP67, IP68 and IP69k rated sensors that withstand wet, washdown conditions to heavy duty safety light screens that guard access points to depalletizers and blow molders, Banner offers a broad range of products that solve difficult primary packaging applications in beverage production.
Our application experts have years of experience and industry knowledge and can draw on our impressive catalog to help your company find and implement products and solutions that ensure a smooth and continuous flow of containers through the system.
Primary Packaging Beverage Applications
View Applications by Machine Type
Featured Applications
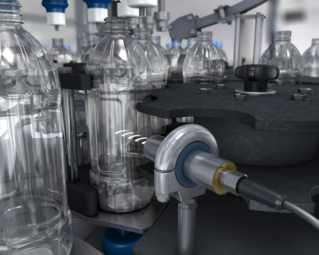
Clear Container Detection in a Clean-in-Place Rotary Filler
Track bottles as they move through the rotary filter.
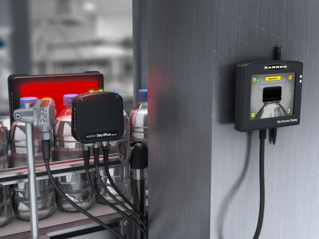
Identifying Presence and Height of a Bottle Cap
The iVu Plus Gen 2 vision system, paired with a Q4X and LEDRB backlight, offer a solution that will provide dependable results.
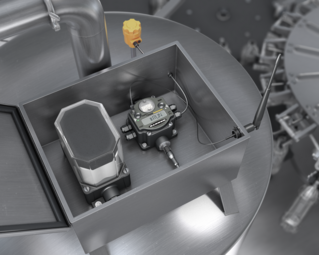
Slip Ring Replacement with Wireless Solutions
Slip rings are subject to constant movement which in turn leads to continuous maintenance in order to avoid degradation of the rotating electrical connection caused by normal wear and debris. Slip ring failure bring production to a halt, resulting in unexpected and costly downtime. The DX80 wireless radios provide a non-contact solution for transmitting the sensor signals from inside the filler bowl to the control panel. The wireless node located on the rotary filler can be battery powered thus providing power to the sensors for a wire-free installation. The DX80 wireless solution eliminates the need for slip rings, helping to decrease downtime and maintenance.
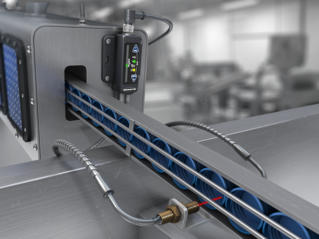
Cap Sorter Detection
Banner’s R55F fiber optic sensors have the capability to detect the presence of caps regardless of their color or size – a clear advantage in an industry that has a wide variety of bottle caps and frequent line changes. In this type of application, the fiber optic sensors are used to recognize long pauses between the caps which would then signal a jam to the operators of the machine. The fibers are compact and can be easily mounted in confined and typically inaccessible spaces.
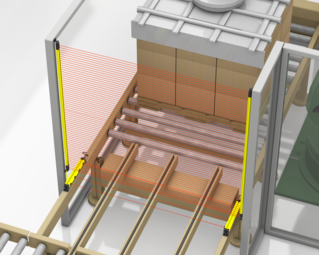
Depalletizer Guarding with Muting
LS light curtains are intuitive, easy-to-use safety devices used for machine safeguarding. They are built to withstand challenges commonly found in manufacturing and packaging environments. LS-S models require no PC software, DIP switches, or other devices for quick, easy configuration. Highly visible alignment indicators and intuitive diagnostics simplify setup, facilitate troubleshooting, and minimize system downtime.
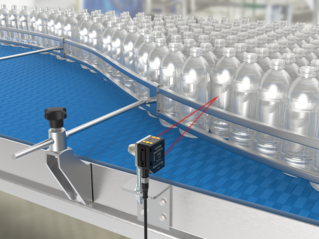
In-Line Accumulation on Single Filer
The Q5X laser sensor reliably detects when the staging area is clear of bottles and the system is ready for the next layer of containers, despite the transparency of the bottles and unstable signal.
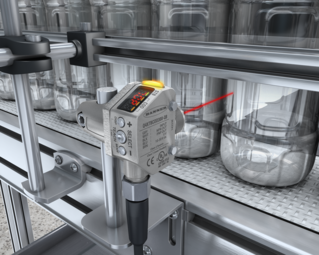
Detecting Bottles in Washdown: Glass & PET Plastic
Washdown environment, IP69K ratings required
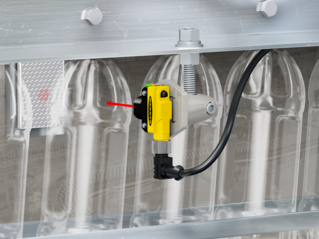
Detecting PET Bottles to Regulate Product Flow
Identifying gaps and accumulations to regulate product flow
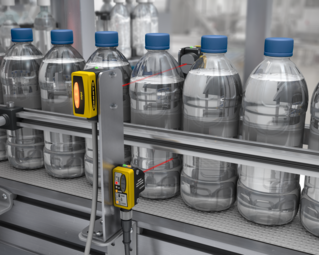
Non-Contact Fill Level Verification
Banner’s QS30H2O sensor is a specialized sensor developed to address challenges with sensing the presence of water and water-based liquids. The QS30H2O operates in a through beam sensing mode and the emitter uses a wavelength that is tuned to not pass through water. The high excess gain of the sensor makes it powerful enough to see through an assortment of plastic and glass containers. Two pairs of sensors can be utilized to determine that the fill level has met minimum but is not overfilled and wasting product. Apertures can be placed on the receiver end to minimize the beam pattern and increase accuracy of the application. This ensures products that do not meet fill level criteria are not processed or shipped.