Rinser Filler Capper Solutions for Beverage Packaging
Bottle filling machines are an all-in-one system with bottle rinser, filler, and capper (RFC). RFC machines as a whole are meant to protect product from damage, contamination, and spoiling. These machines frequently handle large amounts of bottles that come in a variety of shapes, sizes, and colors.
Rinsing empty bottles before moving onto the filling station is an incredibly important step because it helps prevent contaminated product from being distributed. From there, the filling mechanisms of the machine need to make sure that the correct amount of product is put into each bottle to maintain brand consistency. And the last step, the capper, needs to create a reliable seal on the bottle to make sure that liquids do not leak and a high-quality end product is delivered to each consumer. Failure to clean, fill, or seal bottles properly could lead to potential recall and wasted product, which can cost companies a great deal.
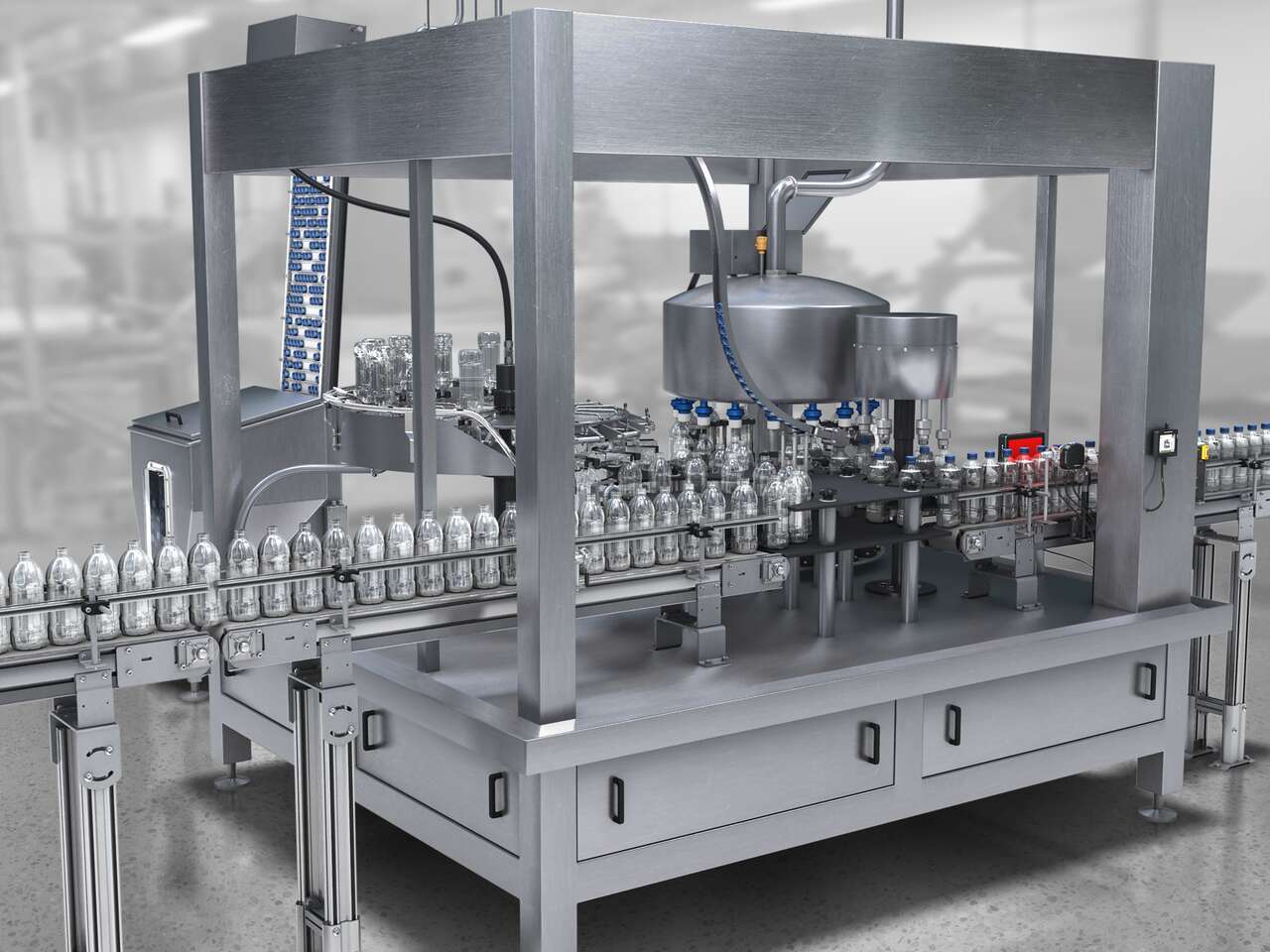
RFC machines on beverage lines need to be suitable for high-pressure and high temperature washdowns, have quick response times for a high-speed environment, and be low maintenance. Finding the best automation equipment for these machines greatly increases a factory’s output without adding additional labor and overhead costs.
Banner Engineering offers a wide variety of products that have environmental ratings up to IP69K and can withstand the harsh environments that the bottling industry is used to. Banner provides automation solutions for container detection, cap sorting and placement verification, fill level verification, slip ring replacement, and improve overall equipment effectiveness (OEE). Our products are versatile and reliable, which means the machines can be easily adapted to meet the needs of a highly competitive beverage market.
Featured Applications
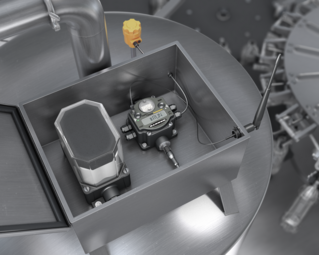
Slip Ring Replacement with Wireless Solutions
Slip rings are subject to constant movement which in turn leads to continuous maintenance in order to avoid degradation of the rotating electrical connection caused by normal wear and debris. Slip ring failure bring production to a halt, resulting in unexpected and costly downtime. The DX80 wireless radios provide a non-contact solution for transmitting the sensor signals from inside the filler bowl to the control panel. The wireless node located on the rotary filler can be battery powered thus providing power to the sensors for a wire-free installation. The DX80 wireless solution eliminates the need for slip rings, helping to decrease downtime and maintenance.
Related Articles
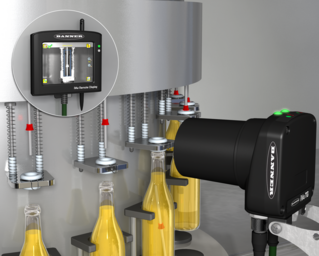
Vent Tube Presence on Filler
A high-volume brewery needed a solution capable of detecting spreader washers on the vent tubes as well as loose or missing tubes. However, the movement of the rotary filler and the wet washdown environment made close proximity deployments difficult and the range required for a remote solution could compromise inspection reliability.
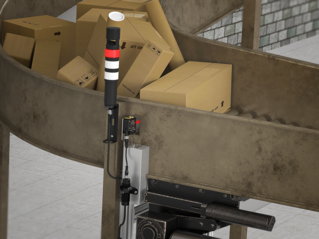
In A World of Jams
Jam Detection is a serious issue for material handling and logistics. Read about what Banner is doing to help solve these occurrences.
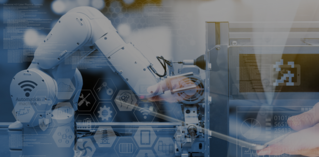
The Smart Factory: IIoT Capabilities for Manufacturers
This article highlights three critical IIoT capabilities of the smart factory: remote monitoring, predictive maintenance, and process optimization.
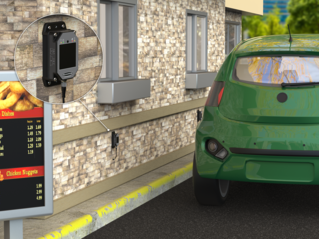
Radar Sensor Frequently Asked Questions
Answers to frequently asked questions about radar technology and Banner's radar sensor products.
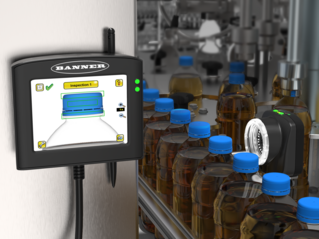
Vision 101: When to Use a Vision Sensor
Many users find vision challenging, and complex vision systems certainly can be overwhelming, but vision is a powerful tool for many applications. Vision sensors are an especially great choice for users getting started with vision. This article explains what vision sensors are, when to use a vision sensor, and when to upgrade to a smart camera.
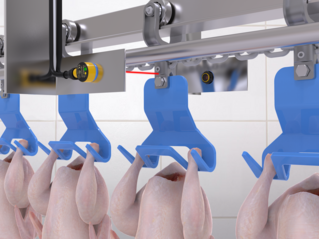
3 Food Safety Hazards & How to Choose Sensor Solutions
Learn 3 of the most common food hazards that can result in product recall and the sensor technologies that can help ensure food safety in each scenario.
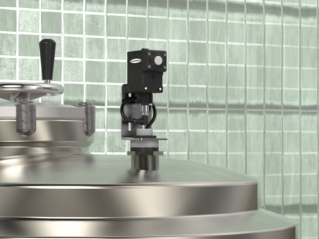
Tank Level Monitoring: Benefits of Wireless Solutions
Properly monitoring and managing tank levels can help improve efficiency and increase productivity and profitability. Read this article to learn about the advantages of wireless remote tank level monitoring.
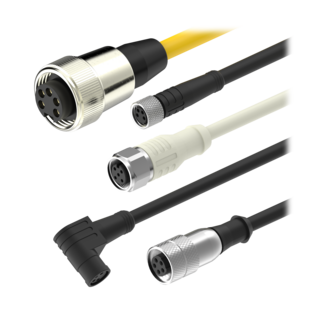
PVC Cable or PUR Cable: How to Choose
PVC and PUR are two of the most common cable jacket materials. Which one should you choose? This guide helps you determine the right one for your application.
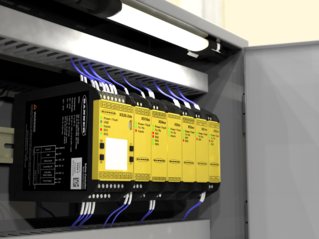
How to Choose an Industrial Safety Controller
Read the article to learn 5 features to look for when choosing an industrial safety controller.
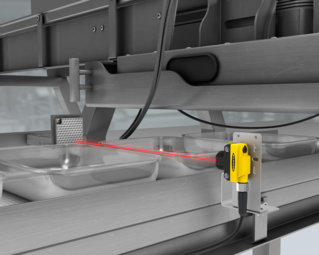
3 Photoelectric Sensing Modes and How to Choose
Sensing mode is one of the most important criteria when selecting a photoelectric sensor. Learn the most common sensing modes and typical applications for each.
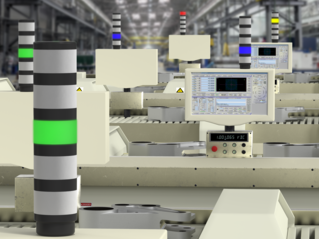
How Remote Monitoring Improves Machine Maintenance
Read the article to learn more about how wireless IIoT technologies are making machine maintenance easier and more effective.
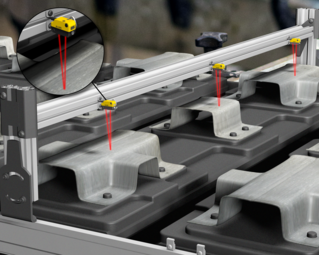
What is Excess Gain and How to Use It To Choose a Sensor
This article explains what excess gain is, how it is measured, and general guidelines for how much excess gain is needed for industrial sensing applications.
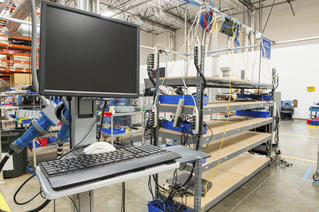
Smart Sensors: IO-Link for Remote Monitoring and OEE
This article describes how IO-Link provides users with remote monitoring capabilities for sensors and can help increase uptime, productivity, and throughput.

Plastic or Glass Fiber Optics? How to Choose
This article explains the differences between glass and plastic fiber optics and how to choose the right fiber optic technology for your application.
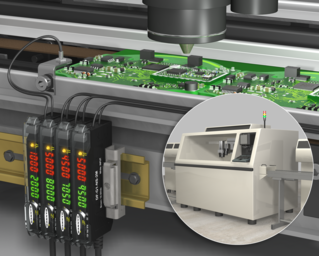
Fiber Optic Sensing Technology: What It Is and How it Works
This article explains what fiber optics are and how they work in industrial applications. Learn important terms and the basics of fiber optic systems and assemblies.
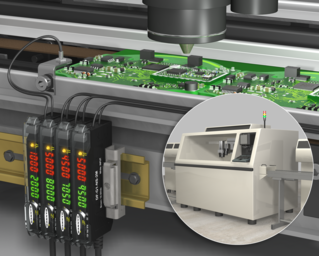
When to Use Fiber Optics for Photoelectric Sensing
This article describes advantages, considerations, and common applications for fiber optic sensors.
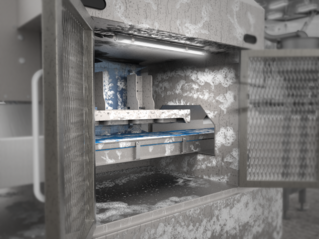
How to Choose Lighting for Harsh Industrial Environments
This article explains common challenges for lighting in industrial environments and considerations for extreme conditions.
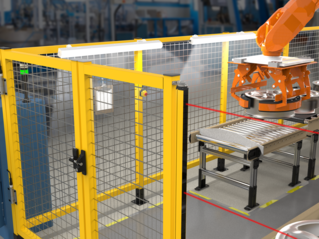
Lighting for Manufacturing: The Costs of Ownership
Are LEDs right for your application? Learn the costs of ownership for lighting in manufacturing environments.
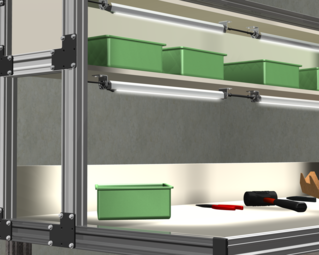
Lux/Lumens Calculator: How Much Light Do You Need?
Use our lux/lumens calculator to determine how much light is needed for your industrial lighting application.
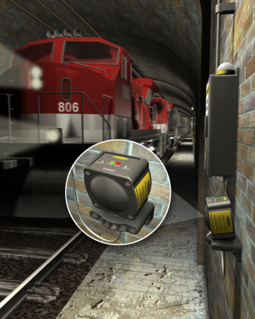
When to Use Radar Sensors for Vehicle Detection
Learn how to use a radar sensor for vehicle detection and find out the top 3 advantages of this technology.
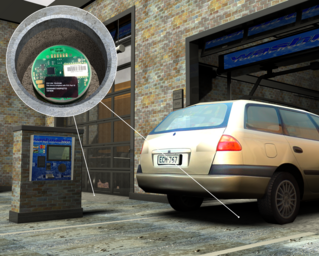
3 Advantages of Wireless Magnetometers for Vehicle Detection
Learn how to use a wireless magnetometer for vehicle detection and find out the top 3 advantages of this technology.
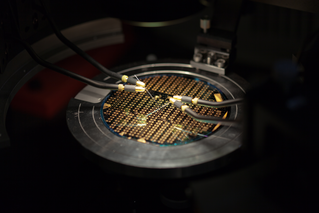
3 Solutions for Semiconductor Wafer Presence Detection
See 3 solutions to reliably detect clear and reflective semiconductor wafers in a vacuum chamber.
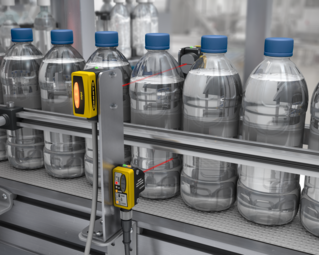
How to Use an Infrared Photoelectric Sensor for Water-Based Liquid Detection
Learn how Banner’s QS30 H2O photoelectric sensor uses a unique optical property of water to reliably detect the presence or absence of water.
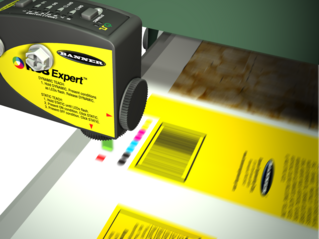
Registration Mark Detection: Why Use RGB Color Mark Sensors
Learn how color mark sensors with RGB technology detect registration marks, when to use a color mark sensor versus true color sensor, and more.
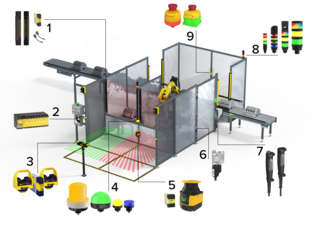
Infographic: 9 Common Machine Safety Devices
Common Machine Safety Devices
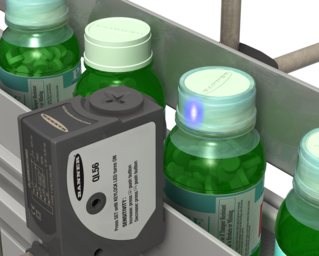
Luminescence Sensors: Answers to Frequently Asked Questions
Luminescence sensors use UV light, invisible to the human eye, to cause the target material to glow in the visible spectrum. This article provides answers to commonly asked questions about luminescence sensors.
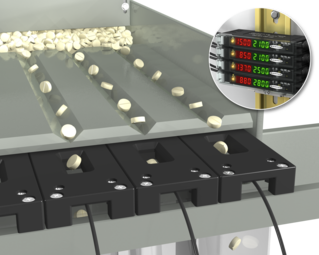
How to Use Photoelectric Sensors for Tablet Counting
Photoelectric sensors offer many important benefits for tablet counting such as high accuracy, fast response speed, and a clean non-contact approach.
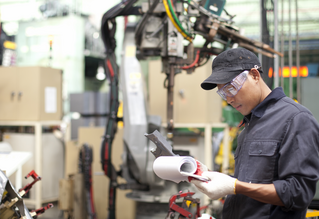
What is a Risk Assessment and Why is It Important?
While it is always best to refer to the standards when planning a risk assessment, here are a few answers to some commonly asked questions.
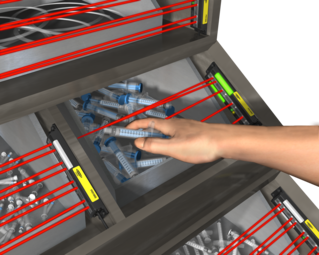
Lean Manufacturing: 4 Lighting Solutions for Pharma Industry
This article describes several ways lighting can help increase efficiency and reduce waste while ensuring product quality & FDA compliance in the pharmaceutical industry.
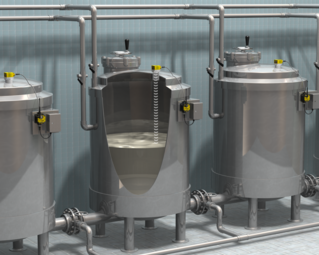
Ultrasonic Sensors: Answers to Frequently Asked Questions
Ultrasonic sensors use sound waves to detect and measure in many different applications. This article answers your questions about how ultrasonic sensors work.
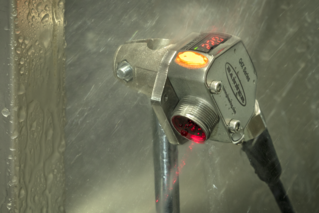
How To Use IP & NEMA Ratings To Choose The Right Sensor
Understanding enclosure NEMA and IP ratings is a necessity. This article explains IP ratings vs NEMA so you can choose the right device for your application.
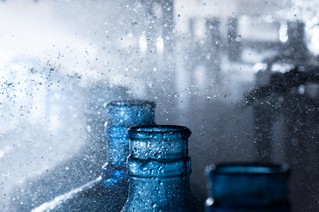
How to Choose the Best Sensor for Clear Object Detection
Understand the differences between common sensor types in Clear Object Detection applications, such as ultrasonic vs. photoelectic retroreflective sensors.
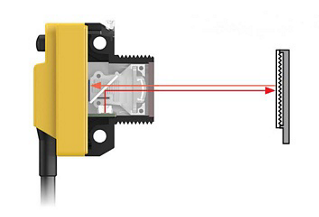
Why Use Polarized Coaxial Optics For Detecting Clear Objects
Clear object detection sensors are sensitive to variations in light and benefit from polarized coaxial optical design to reduce false detection from reflected light.
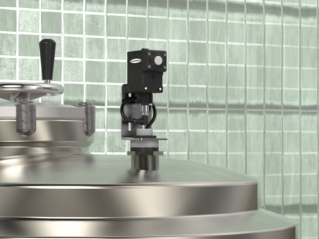
Tank Level Monitoring: 3 Benefits of a Wireless Solution
Properly monitoring and managing tank levels can help improve efficiency and increase productivity and profitability. Read this article to learn about the advantages of wireless tank level monitoring.