Shrink Wrapper Solutions for Beverage Packaging
End-of-line packaging in the beverage industry consolidates bottles and prepares them for shipment. Proceeding through a shrink packaging machine is one of the final steps. Shrink wrap equipment prepares assembled cases of filled bottles by surrounding filled pallets in shrink wrap, preparing it for transportation to the next facility.
Grouping individual products into larger packages commonly means that there will be bigger machines in operation during this final stage, requiring additional solutions to safely perform the required duties. By using automated solutions such as leading edge detection, LED indication, and work area and machine safeguarding, shrink wrap machines work quickly and lead to a more efficient end-of-line packaging.
Beverage containers have gone through many changes as the industry has become more competitive. As companies take steps to lower packaging costs and produce less waste, the final stages of packaging become increasingly important. Banner Engineering offers a wide variety of products that can be successfully used throughout the entire beverage filling line, making end-of-line solutions more versatile to better fit customer’s needs.
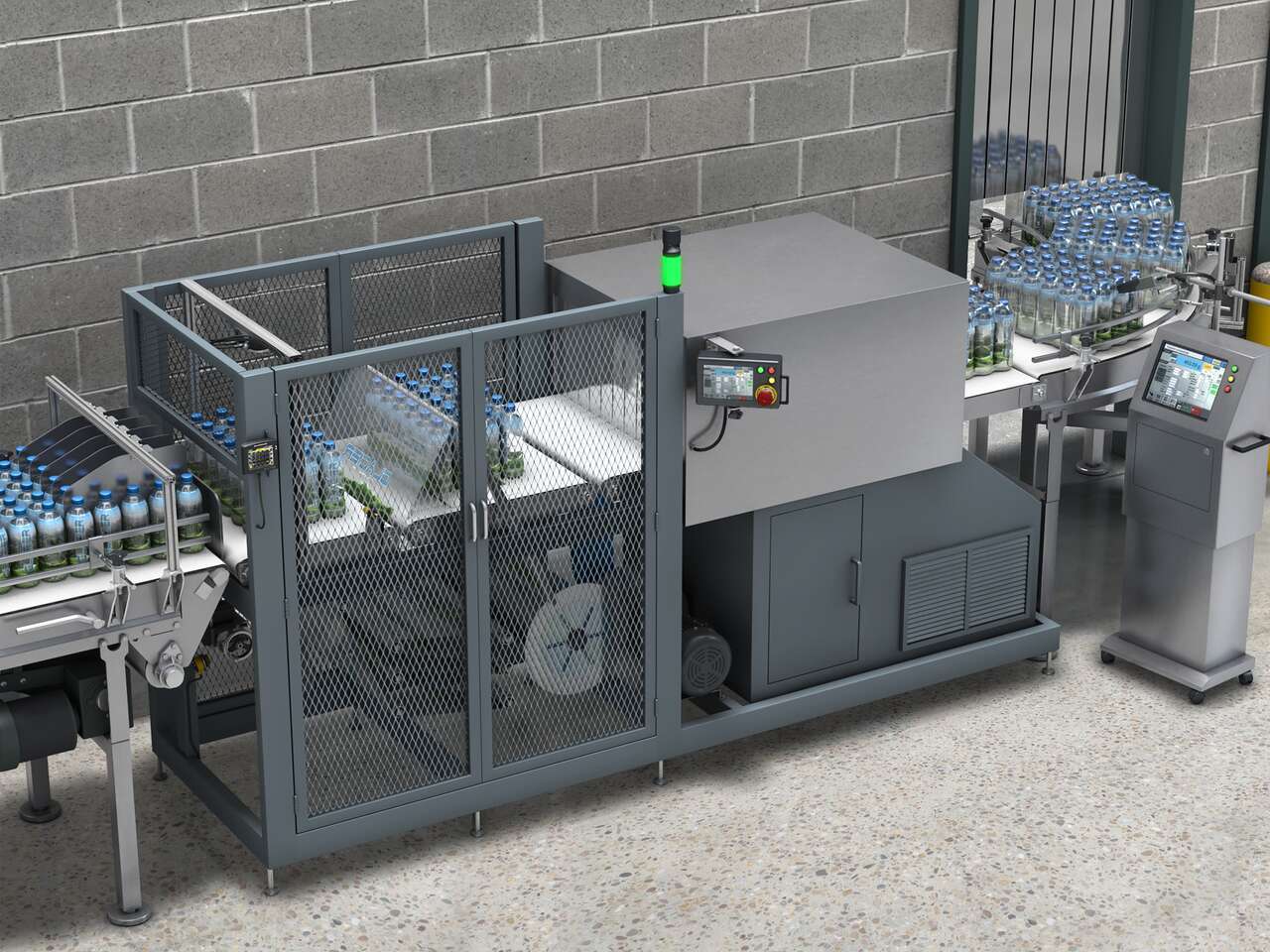
Featured Applications
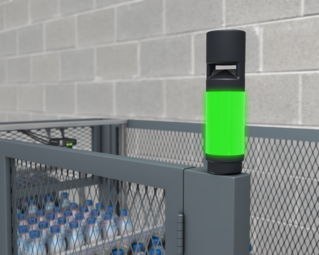
Enunciation of Safety Conditions with Visual Indication
In order to maintain an efficient manufacturing line in the beverage industry, immediate notification of any safety issues is fundamental. Using visual and audible indication to identify safety concerns helps workers quickly find and fix the errors – returning the system to its normal operating state in a timely fashion.
Related Articles
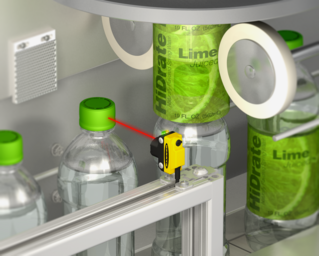
Shrink Sleeve Labeling at High Speeds
A leading manufacturer of labeling equipment offers high-speed shrink sleeve label applicators designed to process 800 bottles per minute. To maximize the machine’s performance potential, the company wanted to install sensors capable of consistent detection and output for high-speed bottling.
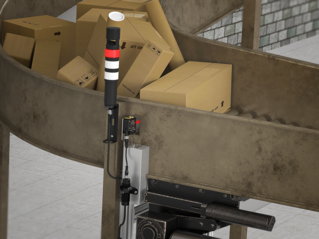
In A World of Jams
Jam Detection is a serious issue for material handling and logistics. Read about what Banner is doing to help solve these occurrences.
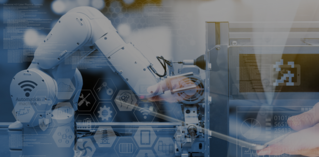
The Smart Factory: IIoT Capabilities for Manufacturers
This article highlights three critical IIoT capabilities of the smart factory: remote monitoring, predictive maintenance, and process optimization.
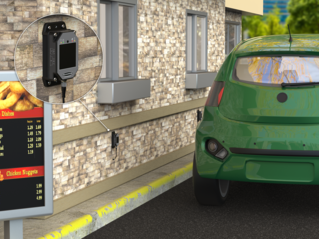
Radar Sensor Frequently Asked Questions
Answers to frequently asked questions about radar technology and Banner's radar sensor products.
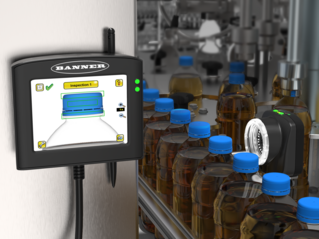
Vision 101: When to Use a Vision Sensor
Many users find vision challenging, and complex vision systems certainly can be overwhelming, but vision is a powerful tool for many applications. Vision sensors are an especially great choice for users getting started with vision. This article explains what vision sensors are, when to use a vision sensor, and when to upgrade to a smart camera.
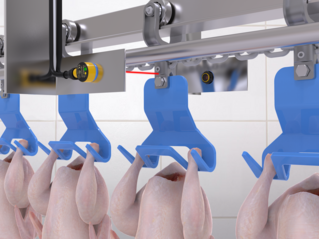
3 Food Safety Hazards & How to Choose Sensor Solutions
Learn 3 of the most common food hazards that can result in product recall and the sensor technologies that can help ensure food safety in each scenario.
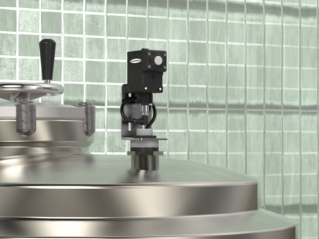
Tank Level Monitoring: Benefits of Wireless Solutions
Properly monitoring and managing tank levels can help improve efficiency and increase productivity and profitability. Read this article to learn about the advantages of wireless remote tank level monitoring.
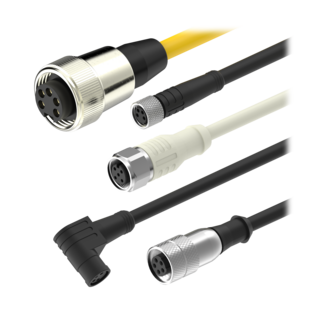
PVC Cable or PUR Cable: How to Choose
PVC and PUR are two of the most common cable jacket materials. Which one should you choose? This guide helps you determine the right one for your application.
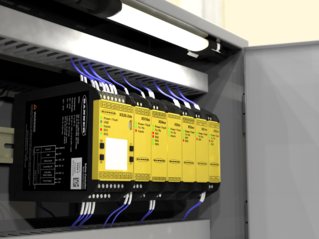
How to Choose an Industrial Safety Controller
Read the article to learn 5 features to look for when choosing an industrial safety controller.
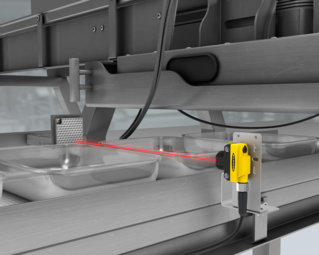
3 Photoelectric Sensing Modes and How to Choose
Sensing mode is one of the most important criteria when selecting a photoelectric sensor. Learn the most common sensing modes and typical applications for each.
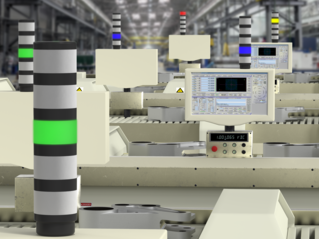
How Remote Monitoring Improves Machine Maintenance
Read the article to learn more about how wireless IIoT technologies are making machine maintenance easier and more effective.
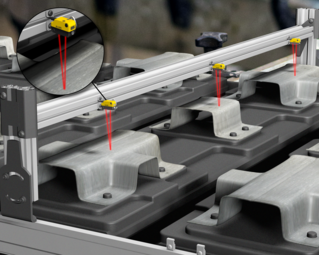
What is Excess Gain and How to Use It To Choose a Sensor
This article explains what excess gain is, how it is measured, and general guidelines for how much excess gain is needed for industrial sensing applications.
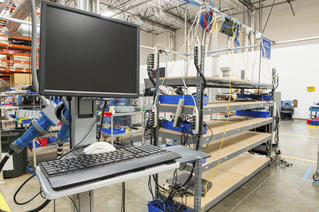
Smart Sensors: IO-Link for Remote Monitoring and OEE
This article describes how IO-Link provides users with remote monitoring capabilities for sensors and can help increase uptime, productivity, and throughput.

Plastic or Glass Fiber Optics? How to Choose
This article explains the differences between glass and plastic fiber optics and how to choose the right fiber optic technology for your application.
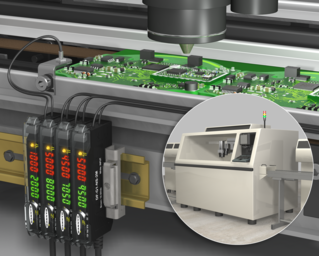
Fiber Optic Sensing Technology: What It Is and How it Works
This article explains what fiber optics are and how they work in industrial applications. Learn important terms and the basics of fiber optic systems and assemblies.
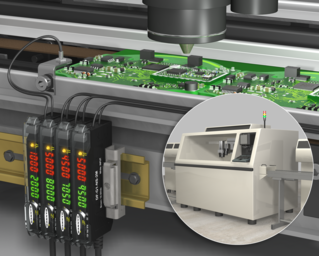
When to Use Fiber Optics for Photoelectric Sensing
This article describes advantages, considerations, and common applications for fiber optic sensors.
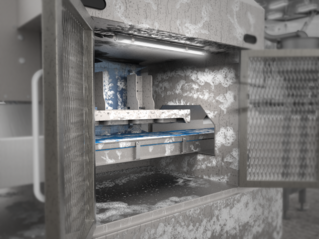
How to Choose Lighting for Harsh Industrial Environments
This article explains common challenges for lighting in industrial environments and considerations for extreme conditions.
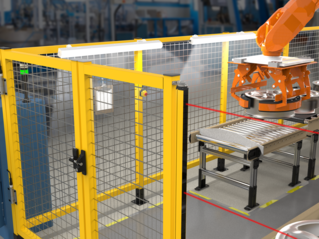
Lighting for Manufacturing: The Costs of Ownership
Are LEDs right for your application? Learn the costs of ownership for lighting in manufacturing environments.
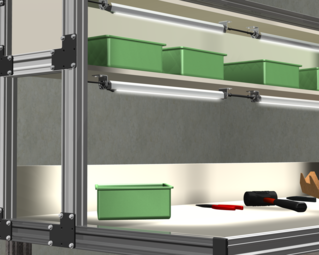
Lux/Lumens Calculator: How Much Light Do You Need?
Use our lux/lumens calculator to determine how much light is needed for your industrial lighting application.
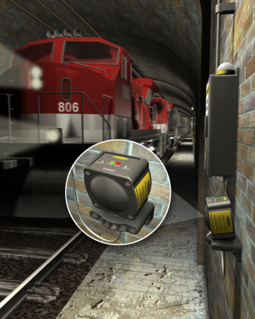
When to Use Radar Sensors for Vehicle Detection
Learn how to use a radar sensor for vehicle detection and find out the top 3 advantages of this technology.
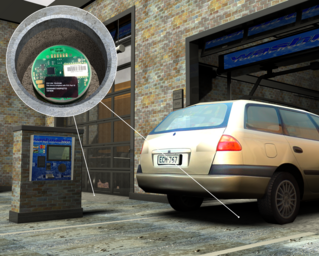
3 Advantages of Wireless Magnetometers for Vehicle Detection
Learn how to use a wireless magnetometer for vehicle detection and find out the top 3 advantages of this technology.
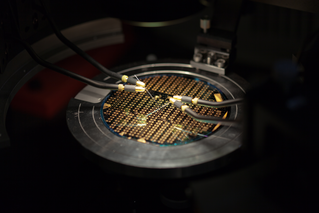
3 Solutions for Semiconductor Wafer Presence Detection
See 3 solutions to reliably detect clear and reflective semiconductor wafers in a vacuum chamber.
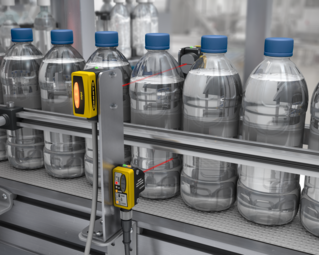
How to Use an Infrared Photoelectric Sensor for Water-Based Liquid Detection
Learn how Banner’s QS30 H2O photoelectric sensor uses a unique optical property of water to reliably detect the presence or absence of water.
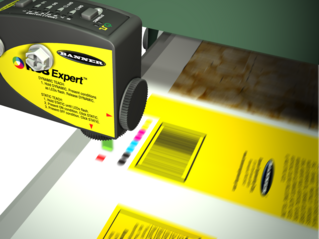
Registration Mark Detection: Why Use RGB Color Mark Sensors
Learn how color mark sensors with RGB technology detect registration marks, when to use a color mark sensor versus true color sensor, and more.
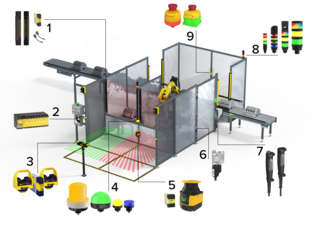
Infographic: 9 Common Machine Safety Devices
Common Machine Safety Devices
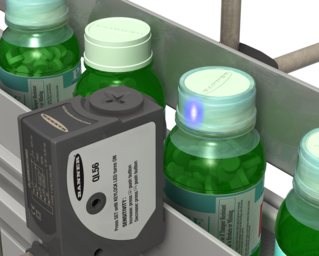
Luminescence Sensors: Answers to Frequently Asked Questions
Luminescence sensors use UV light, invisible to the human eye, to cause the target material to glow in the visible spectrum. This article provides answers to commonly asked questions about luminescence sensors.
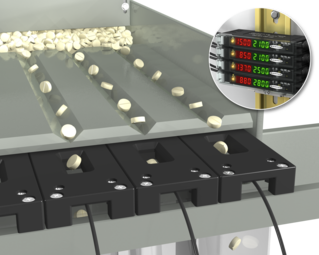
How to Use Photoelectric Sensors for Tablet Counting
Photoelectric sensors offer many important benefits for tablet counting such as high accuracy, fast response speed, and a clean non-contact approach.
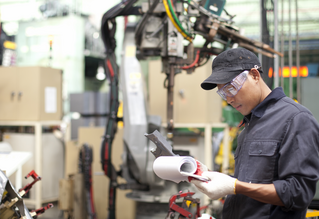
What is a Risk Assessment and Why is It Important?
While it is always best to refer to the standards when planning a risk assessment, here are a few answers to some commonly asked questions.
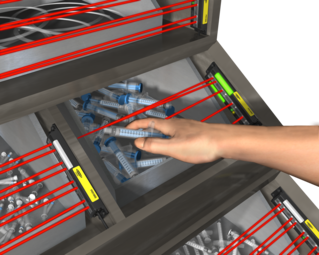
Lean Manufacturing: 4 Lighting Solutions for Pharma Industry
This article describes several ways lighting can help increase efficiency and reduce waste while ensuring product quality & FDA compliance in the pharmaceutical industry.
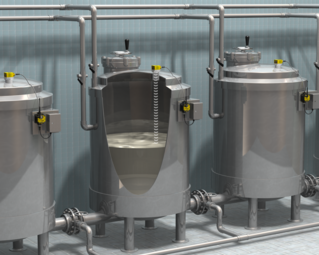
Ultrasonic Sensors: Answers to Frequently Asked Questions
Ultrasonic sensors use sound waves to detect and measure in many different applications. This article answers your questions about how ultrasonic sensors work.
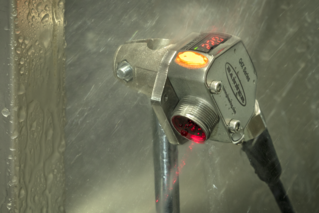
How To Use IP & NEMA Ratings To Choose The Right Sensor
Understanding enclosure NEMA and IP ratings is a necessity. This article explains IP ratings vs NEMA so you can choose the right device for your application.
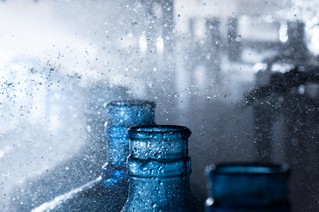
How to Choose the Best Sensor for Clear Object Detection
Understand the differences between common sensor types in Clear Object Detection applications, such as ultrasonic vs. photoelectic retroreflective sensors.
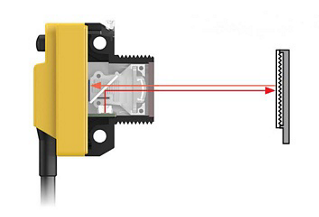
Why Use Polarized Coaxial Optics For Detecting Clear Objects
Clear object detection sensors are sensitive to variations in light and benefit from polarized coaxial optical design to reduce false detection from reflected light.
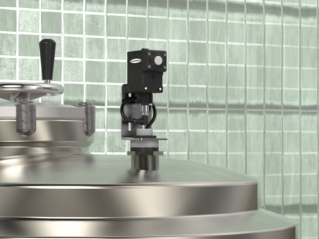
Tank Level Monitoring: 3 Benefits of a Wireless Solution
Properly monitoring and managing tank levels can help improve efficiency and increase productivity and profitability. Read this article to learn about the advantages of wireless tank level monitoring.