機械の安全性:リスクアセスメントとは?リスクアセスメントが大切である理由
画像:リスクアセスメントは危険を最小限に抑えるために必要な対策の決定に役立つ
概要: 機械の安全性に関して、リスクアセスメントは特定の機械またはプロセスにおける危険性の特定、記録、排除または低減に使用されます。リスクアセスメントを計画するには各種規格を参照するのが最良の方法ですが、ここではよくある質問に対する回答をいくつかご紹介します。
この記事は教育上の目的のみに作成され、発行された時点で正確であったものです。 バナーでは、安全措置を履行する前に各用途について安全の専門家に相談することを推奨します。
質問:リスクアセスメントとは?
極端に言うと、リスクアセスメントとは次のことを特定するのに役立つプロセスです:
- 潜在的な危険
- 潜在的な危険の程度
- 危険にさらされる頻度
- 危険を最小限に抑えて危害が生じるのを防ぐ方策
このプロセスは、あらゆる安全性の問題に対応した手っ取り早い解決法ではなく、100%怪我のない作業場を保証するものでもありません。そうではなく、作業場での危険について文書に記録するために使用するリスク診断および安全規定として、リスクの許容レベルを特定し、リスクを軽減するための一連の措置を決めるために役立ちます。
質問:リスクアセスメントではどのような処置を講じる必要がありますか?
リスクアセスメントプロセスの基本的な処置とは:
- 作業場でのタスクとそれに関連した危険を特定する
- 危害が及ぶ可能性とその程度を評価する
- 危険を排除すること、または防護措置をとることで危害が生じるリスクを軽減する
- プロセスとその結果を文書に記録する
リスクアセスメントプロセスとその記録により、機械メーカーや事業手は安全な作業場と高品質の製品を提供してデューディリジェンスの実施を証明できます。
質問:どの規格に準拠するべきですか?
規格や基準は数多くの種類があります。その一例:
- ANSI/RIA R15.06 -1999、産業用ロボットおよびロボットシステムに関する安全性要求事項
- ANSI B11 TR3、リスクアセスメントとリスク軽減
- ISO 14121(EN 1050)、リスクアセスメントの原則
- OSHA 3071 作業ハザード分析
- IEC 812 FMEA
リスクアセスメントプロセスと安全装置のカテゴリーについて大綱が定められているEN 1050およびISO 13849-1も参照しください。
規格はリスクアセスメントプロセスの全体的にまとまりのある方策またはアプローチを特定するために役立ちます。規格に従うことでより良い決定およびリソースのより効率的な利用につながります。
質問:OSHAにより承認されている規格はありますか?
OSHA (米国労働安全衛生局) からは指示が与えられるのではなく、目標のみが提示されます。業界で認められているリスク軽減方法を各企業でできる限り適用することが一般的に期待されています。
質問:リスクアセスメントの実施に責任を負うのは誰ですか?
米国では ANSI (米国規格協会) 規格のリスクアセスメントについて定義されているB100.0 2010やRIA 15.06 2012などで、機械サプライヤとユーザーの両者が安全の確保に責任を持つことが要求されています。
OSHAでは、リスクアセスメントを実施すること、リスク回避計画の履行がそれに伴うべきであること、そしてプロセス全体を細部に至るまで文書に記録してデューディリジェンスの実施を証明できるようにすることを強く推奨しています。
欧州では、安全な機械が供給されることに主に責任を負うのは機械サプライヤであるとされています。そして、基本的なリスクアセスメントを実施するのは、通常はサプライヤとなります。
質問:リスクアセスメントのプロセスには誰が関与するのですか?
さまざまな業種から、尊敬されている従業員を集めてください。候補者としては、オペレータ、メンテナンスエンジニア、電気技術者、機械技師、シフトリーダー、製造監督者、安全の専門家が挙げられます。これらの従業員は、リソースの配分を担当する会社役員から必要な権限を与えられます。このプロセスを信ぴょう性があるものにするために、経営者側がリーダーシップを発揮してそれを従業員に見せる必要があります。
質問:リスクアセスメントを実施するためにコンサルタントを雇うことはできますか?
有能なコンサルタントの助けがあればリスクアセスメントのプロセスは大いに強化されると思われますが、人的な安全性に最終的に責任を負うのは事業主です。従業員も危険を認識して適切に行動できるようにトレーニングが必要です。
質問:リスクアセスメントはいつ実施するべきですか?
理想としては、何らかの変化があったとき、特に新しい機械やシステムを導入したとき、新しいタスクが加わったとき、新しいルーチンが考案されときにそのつどリスクアセスメントを実施することが望ましいとされています。新しいプロセスが加わったときに、どのタスクによって危険が生じる可能性があるのかを評価するのです。
質問:何を評価する必要がありますか?
潜在的な危険だけではなく、すべてを評価する必要があります。作業環境、エルゴノミクス、雑音などすべてです。侵害や訴訟の場合、特定のリスクに対してリスクアセスメントが十分であったことを証明しなければならなくなりますので、そのことを覚えていてください。
質問:このプロセスはどのように開始するべきですか?
最初に行うことは、リスクアセスメントの目標が危険のない作業場であることを説明して、現場の第一線の従業員にやる気を起こさせることです。そのとき、従業員一人ひとりが自分の安全に責任を持つことを強調します。危険を認識したらそれを報告するのは従業員の責任になります。
質問:防護が難しい危険な機械で怪我を負うリスクを軽減するには何をすればいいですか?
設計の観点からできることをしてみてください。安全装置を設置し、個人用保護具を使用し、危険性に対する全般的な認識のレベルを上げます。そして、危険要因を排除または管理できないタスクには安全に作業するための手順を策定します。最終的に、危険性が許容できるレベルになるようにしてください。
質問:リスクの優先度はどのように判断しますか?
常に最も危険性が高い場所を優先してください。人間工学を考慮した作業場は、防護措置がとられていない打抜きプレス機より優先度が低くなります。
質問:どの危険要因が他のものより危険であるとどのようにして決めていますか?
そのプロセスをサポートするための産業リスクアセスメントモデルが策定されています。
質問:リスクアセスメントはどの産業分野で採用されているのですか?
リスクアセスメントは、作業場での事故を最小限に抑える必要があり、製品の品質と性能が非常に重要であるさまざまな産業分野で実施されています。その中には、危険性を評価するプロセスを標準化するに至った産業分野もあります。その一例は:
- 金属成形/切断
- 医療装置
- 産業用ロボット
- 保険
- 航空宇宙産業
- 半導体
- 輸送
質問:小規模の企業でリスクアセスメントの結果を記録する必要はありますか?
あります。規模に関係なくすべての企業で、実施されたリスクアセスメントについて余すところなくすべて文書に記録することを強く推奨します。安全に関連して何らかの出来事が起こったとき、リスクアセスメントが適切に実施されたこと、必要とされるあらゆるリスク回避方策がとられていたことをこの文書で証明することができます。
質問:OEMもリスクアセスメントを実施する必要がありますか?
あります。通常想定できる範囲内での装置の使用および/または誤使用に関連した危険性について考慮すること、そしてそれらの危険性をできる限り取り除いたり最小限に抑えることは最低限の責任です。OEMは、設備の運用に関連したあらゆる残存リスクについて顧客に知らせる義務を負っています。
そしてエンドユーザーは、監視、警告の標識、トレーニングなどの管理上の措置や安全対策を取り入れることで、さらなる既知のリスクを軽減します。
質問:リスクアセスメントの正確さはどのようにして確認できますか?
一般に、特定の産業分野で確立された最小限の要件をすべて満たすかそれを超えており、結果が定期的に見直され確認されていることを証明できれば、リスクアセスメントが正確であると見なされます。
質問:他の国々で規格に準拠しているかどうか知ることはできますか?
たいていの国ではISO (国際標準化機構)規格が採用されています。 きちんとしたリスクアセスメントが実施されていれば、大部分の国々の規格も満たしていると考えられます。
質問:リスクアセスメントは安全プログラムのどのポジションに含まれていますか?
OSHAが提案する安全プログラムのルールでは、リスクアセスメントは安全プログラムの中核となる5つの要素のうち2番目に位置付けされています。これは、経営陣のリーダーシップと従業員の関与のすぐ後に来ます。
質問:FMEAとは何ですか?
FMEA (Failure Mode and Effect Analysis、故障モード影響解析) とは、リスク分析に使用される特別な手順です。危険要因を識別するとき、時には危険を抑制したり人々を危険から守るコンポーネントを体系的に見る必要があります。例えば、バルブの減速、ブレーキの摩耗、機械的なドアスイッチの故障など。安全のために当てにされるコンポーネントであれば、その故障モードと安全性への影響を分析する必要があります。
この記事は教育上の目的のみに作成され、発行された時点で正確であったものです。 バナーでは、安全措置を履行する前に各用途について安全の専門家に相談することを推奨します。
この記事で取り上げられた製品
関連記事
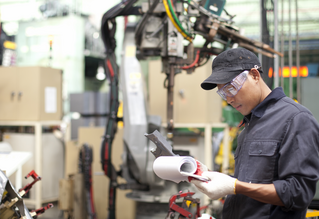
リスクアセスメントとは?リスクアセスメントが大切である理由
リスクアセスメントを計画するには各種規格を参照するのが最良の方法ですが、ここではよくある質問に対する回答をいくつかご紹介します。
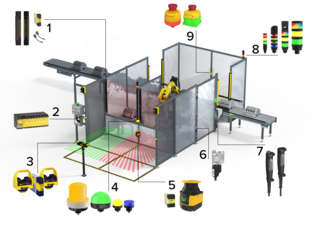
インフォグラフィック:9つの一般的な機械安全装置
一般的な機械安全装置
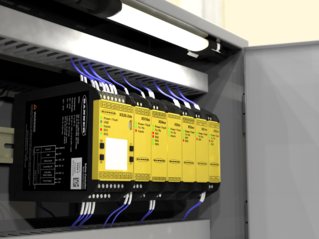
産業用安全コントローラの選び方
産業用セーフティコントローラを選ぶ際に注目すべき5つの機能について、記事をお読みください。