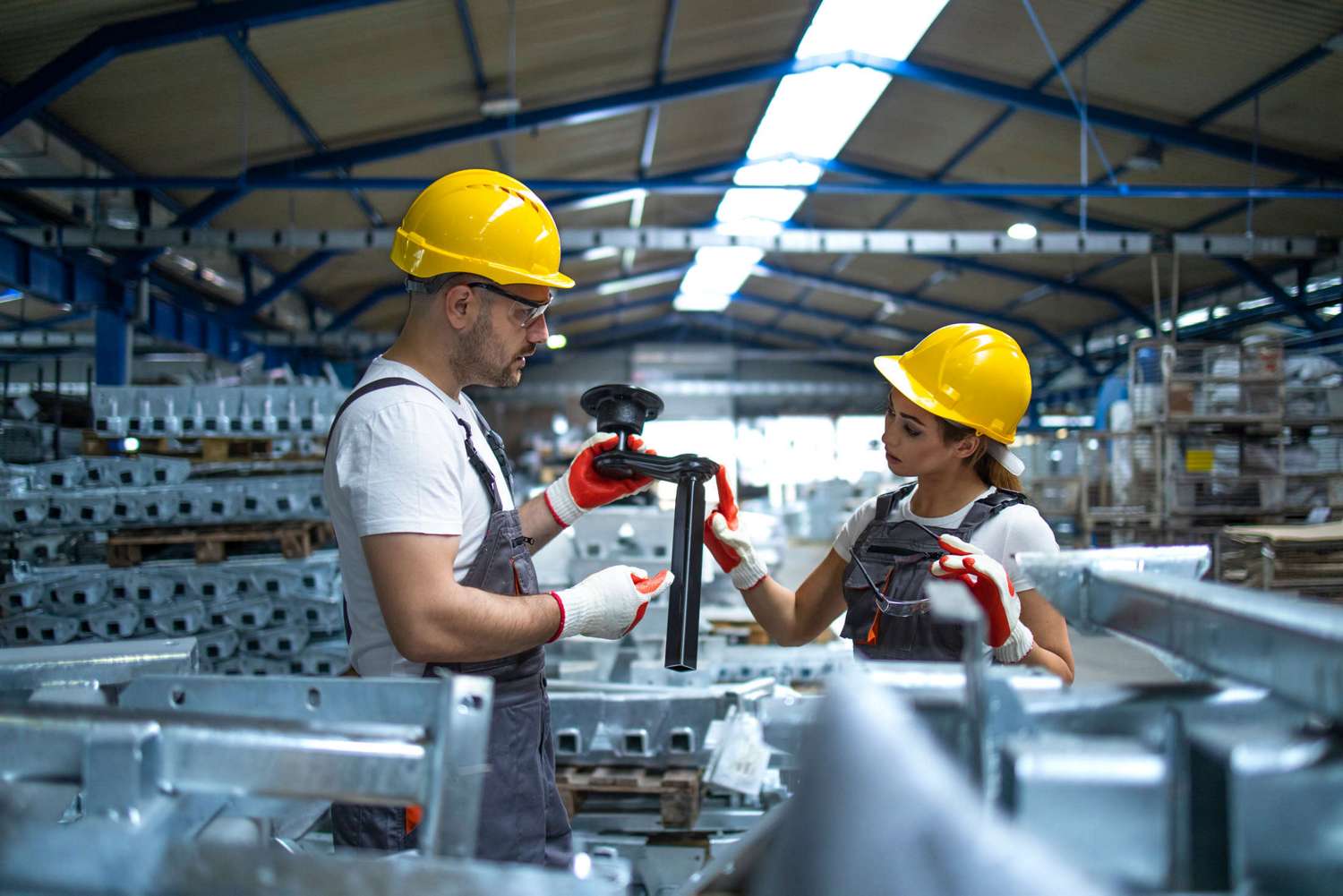
Intelligente Sensoren: Verwendung von IO-Link für Fernüberwachung und OEE
In diesem Artikel wird eine Schlüsseltechnologie beschrieben -IO-Link-Kommunikation-, die den Benutzern Fernüberwachungsfunktionen auf der Ebene der Feldgeräte bietet. In diesem Artikel wird auch erläutert, wie die durch diese Technologie zugänglich gemachten Ferndaten dazu beitragen können, die Maschinenbetriebszeit, die Produktivität und den Durchsatz zu erhöhen - alles Faktoren, die sich auf das Endergebnis eines Unternehmens auswirken.
Fernüberwachung auf der Sensorebene
Daten von Sensoren und anderen Feldgeräten waren früher nur schwer oder gar nicht zugänglich. Für viele Hersteller bieten diese Geräte ein ungenutztes Potenzial für einen besseren Einblick in ihre Abläufe und eine fortschrittlichere, datengesteuerte Entscheidungsfindung.
Mit dem Aufkommen des Industrial Internet of Things (IIoT) können Daten auf Geräteebene nun für Bediener und Betriebsleiter zugänglich gemacht werden, was wertvolle Einblicke in die Maschinenleistung, Prozessineffizienzen und vieles mehr ermöglicht. Die Echtzeit-Fernüberwachung des Sensorstatus ermöglicht es den Bedienern, Probleme zu lösen, sobald sie auftreten, und häufig Probleme zu beheben, bevor sie zu einer Abschaltung der Anlage führen.
Die IO-Link-Kommunikation ist eine Technologie, die dem Anwender Fernüberwachungsmöglichkeiten auf der Ebene der Feldgeräte bietet.
Wie IO-Link funktioniert
IO-Link (IEC61131-9) ist ein offenes, standardisiertes serielles Kommunikationsprotokoll, das den bidirektionalen Austausch von Daten von Sensoren und Geräten ermöglicht, die IO-Link unterstützen und an einen Master angeschlossen sind. Der IO-Link-Master überträgt Daten von IO-Link-Geräten wie Sensoren und Anzeigen über verschiedene Netzwerke, Feldbusse oder Rückwandbusse. Die Gerätedaten sind somit für sofortige Maßnahmen oder langfristige Analysen über eine Steuerung wie eine SPS oder ein HMI zugänglich. Das gibt Anwendern mehr Informationen über ihre Geräte und ermöglicht die Fernüberwachung der Maschinenleistung.
Dank der Möglichkeit, die Sensorausgänge zu überwachen, Statusmeldungen in Echtzeit zu erhalten und Einstellungen von praktisch jedem Ort aus anzupassen, können Benutzer Probleme, die auf der Sensorebene auftreten, rechtzeitig erkennen und beheben. Dies bedeutet auch, dass Anwender Entscheidungen auf der Grundlage von Echtzeitdaten von den Maschinenkomponenten selbst treffen können. Hierdurch können kostspielige Ausfallzeiten verringert und die Effizienz insgesamt verbessert werden.
Weitere Informationen zur IO-Link-Technologie finden Sie unter Was ist IO-Link und die 5 wichtigsten Vorteile.
3 Möglichkeiten zur Verwendung von IO-Link für die Fernüberwachung
1. Geräteparameter aus der Ferne lesen und ändern
Mit IO-Link können Anwender Geräteparameter über die Software des Steuersystems ablesen und ändern. Dies ermöglicht eine schnelle Konfiguration und Inbetriebnahme und spart Zeit und Ressourcen. Darüber hinaus können IO-Link-Sensoren mehrere Formeln verarbeiten, die über das Steuersystem bei Bedarf schnell und dynamisch geändert werden können − z. B. bei einem Produktwechsel. Beispielsweise gibt es Verpackungsanlagen, die zu unterschiedlichen Zeiten Produkte in verschiedenen Größen verarbeitet. Hierfür müssen die Abstandsschwellenwerte der Sensoren geändert werden.
Bei der Umschaltung schreibt der IO-Link-Master einfach den neuen Schwellwert in die Sensoren, und die Sensoren müssen zum Teachen nicht anwesend sein. Dies spart viel Zeit bei der Sensorkonfiguration für die Umrüstung, was die Ausfallzeiten reduziert, die Produktivität und den Durchsatz erhöht und es den Maschinen ermöglicht, eine größere Produktvielfalt zu bewältigen.
2. Gerätezustand und Laufzeit aus der Ferne überwachen
Die IO-Link-Kommunikation bietet auch die Möglichkeit, Alarme zu erstellen und vorausschauende Wartung Aufgaben auf der Grundlage von Echtzeit-Sensordaten. Sensoren wie der Q4X Laserdistanzsensor mit IO-Link liefern beispielsweise Daten zur Überschussverstärkung über IO-Link, die dazu verwendet werden können, zu erkennen, wann ein Sensor gereinigt werden muss (wenn sich Staub und andere Partikel auf der Sensorlinse ansammeln, nimmt die Überschussverstärkung ab). Es können Warnmeldungen eingerichtet werden, damit die Sensoren gereinigt werden können, bevor die Ablagerungen die Erkennungsfunktion beeinträchtigen. Probleme mit der Geräteverbindung werden ebenfalls in Echtzeit gemeldet, so dass sie zeitnah behoben werden können.
IO-Link liefert nicht nur wertvolle Informationen über den Zustand der Geräte, sondern ermöglicht es den Benutzern auch, die Gesamtlaufzeit zu verfolgen, um vorherzusagen, wann ein Gerät ersetzt werden muss. Anhand dieser Informationen können die Sensoren während der geplanten Wartung ausgetauscht werden, wodurch unnötige Ausfallzeiten vermieden werden. Laufzeitdaten können auch für OEE-Berechnungen verwendet werden (siehe Punkt 3).
Darüber hinaus zeigt die Erkennungsfunktion mit IO-Link an, welcher Sensor Aufmerksamkeit benötigt, insbesondere wenn viele Sensoren gruppiert sind. In dem Beispiel in der Abbildung unten befinden sich mehrere Q4X-Sensoren auf engem Raum, so dass es schwierig ist, festzustellen, welcher Sensor gereinigt werden muss. Die Erkennungsfunktion lässt den problematischen Sensor blinken, so dass das Problem schnell erkannt und behoben werden kann.
3. Nutzen Sie aufgezeichnete Daten zur Maximierung der Gesamtanlageneffektivität (OEE)
IO-Link-Geräte sind auch für die Bereitstellung von Daten für OEE-Berechnungen von Bedeutung. Die Gesamtanlageneffektivität (GAE) ist eine Berechnung der Effizienz des Herstellungsprozesses unter Berücksichtigung von drei Hauptfaktoren: Verfügbarkeit, Leistung und Qualität.
Der Verfügbarkeitsfaktor berücksichtigt Ereignisse, die die Gesamtlaufzeit verringern, einschließlich geplanter Stopps (z. B. für Produktumstellungen) und ungeplanter Stopps. Der Faktor Leistung erfasst alles, was die Geschwindigkeit des laufenden Herstellungsprozesses verlangsamt. Und der Qualitätsfaktor berücksichtigt Teile oder Produkte, die nicht den Qualitätsstandards entsprechen (Teile, die verschrottet oder nachbearbeitet werden müssen, was zu Zeitverlusten führt).
Die OEE-Berechnung bewertet diese Faktoren und drückt das Ergebnis als Prozentwert aus, wobei 100% bedeutet, dass nur gute Teile hergestellt werden (Qualität), und zwar so schnell wie möglich (Leistung) und ohne Unterbrechungen (Verfügbarkeit). Die Ergebnisse dieser Berechnung liefern umsetzbare Erkenntnisse über die ausschlaggebenden Quellen für Verschwendung im Herstellungsprozess.
Um Verschwendung zu reduzieren und die OEE zu verbessern, ist es wichtig, dass man weiß, wo und wann Ineffizienzen auftreten, und zwar bis hinunter auf die Sensorebene. Der Zugriff auf Leistungs- und Laufzeitdaten von IO-Link-Sensoren und -Indikatoren ist daher entscheidend für die Berechnung der OEE und die Ermittlung von Maßnahmen zur Verbesserung der Effizienz Ihrer Maschinen, Prozesse und Mitarbeiter.
Empfohlene Produkte
Artikel zu verwandten Themen
-
Tankfüllstandsüberwachung: Vorteile von drahtlosen Lösungen
-
Wie die Fernüberwachung die Maschinenwartung verbessert
-
Die 5 heißesten Trends in der industriellen Automatisierung für 2017
-
Intelligente Sensoren: IO-Link für Fernüberwachung und OEE
-
Temperatur-Fernüberwachung und FSMA
-
Lean Manufacturing: Vier Beleuchtungslösungen für die Pharmaindustrie